A large number of optical systems designed for precision applications (such as optical inspection, DVD mastering, micro-lithography or projection printing) need a substantial optical engineering contribution in order to support the manufacturing team in the fabrication of these systems.
Lenses used in these industries are often subject to performance demands, which in turn dictate diffraction limited wavefront quality, minimal image distortion and the ability to resolve very small features.
Achieving the needed ‘as-built’ performance requirements for the lens assembly may involve optical designers whose role is to select and compensate manufactured parts before these are released to the component assembly team.
Comprehensive engineering involvement at this level is ideal for prototype quantities, but this may hinder the manufacturing stream where the system begins to transition to larger production quantities.
Properly supporting the manufacture of volume assemblies may need to involve a dedicated team of optical design engineers who are able to oversee the day to day project needs of lens selection and compensation, in order to properly keep pace with the rate of delivery.
Another potential means of managing the engineering duties of precision optical systems is the development of a manufacturing stream that enables the transfer and transition designer project support to the teams responsible for assembly and fabrication.
Manufacturing Philosophy and Key Components
When producing high-end optical systems, manufacturing strategies generally rely on a philosophy which sees every fabricated objective modelled before being simulated in optical design software ahead of any commitment to component assembly (Figure 1).

Figure 1. Manufacturing Philosophy. Image Credit: Corning Incorporated - Advanced Optics
A group of lens elements must first be custom selected from the population of manufactured parts in order to minimize aberration build up. The measured fabrication properties of the component (radius, thickness, index, etc.) are then modeled in design code, with additional gains in performance being achieved through optimization with pre-determined air spaces.
Mechanical parts are adjusted accordingly, achieving the preferred lens spacings. This manufacturing approach permits looser optical fabrication tolerances instead of building a static objective. Traditionally, the optical designer is responsible for the fine tuning and computer simulation of each optical assembly.
While this methodology is well suited to small quantity production, it requires some thought before being applied to the production of optical systems in sizeable volumes.
A specific manufacturing strategy has been created to implement a Volume Manufacturing Compensation Platform (VMCP), allowing for largescale production of high performance optical systems. An appropriate software platform, coupled with a suite of compensation tools, was employed to integrate optical design support functions into an existing volume manufacturing stream (VMS).
The primary platform components (Figure 2) are comprised of an integrated computer network that is accessible to design and manufacturing. It also incorporates electronic fabrication records which are stored in a Lens Manufacturing Database (LMD),1 as well as optical design analysis/compensation software, and the ability to provide a lens assembly report which is unique to each individual manufactured lens unit.
This particular infrastructure is also suitable for automating the design compensation process, meaning it is well placed for incorporation into a production VMS.
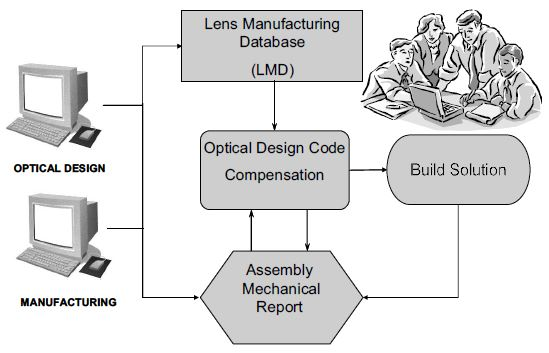
Figure 2. Volume Manufacturing Compensation Platform. Image Credit: Corning Incorporated - Advanced Optics
Project Requirements for VMCP
There are fundamental requirements that a project must meet in order to be integrated into the VMCP. The volume should be substantial enough to justify investing the time and effort to develop the software code needed to manage factors like data collection, design optimization, reporting and solution tracking.
In optical projects where more than one to two dozen lenses are planned for manufacture, the initial investment will be recouped.
However, the strategy for design compensation should be rigorous, thoroughly comprehended and effectively characterized. This will mean that the system compensation algorithm can yield an appropriate solution without the need to be fine-tuned or adjusted on a set by set basis.
Tolerance budgets must be meticulously allocated to various manufacturing parameters such as mechanics, optics, assembly and test. This helps to establish acceptance threshold criteria, allowing engineers to judge whether or not a lens solution should be released to assembly to be built.
VMCP and Operation
The VMCP is designed to be compatible with a range of lens systems, compensation paths, complexities and manufacturing requirements. Each lens system possesses its own distinct built in performance metrics and compensation processes, all of which must be observed.
Parameters are agreed between the manufacturing and lens design teams. Process information is committed to flow diagrams and work procedures, while an optical designer will typically oversee the project’s development and its integration into the VMCP.
The software will calculate design quality metrics made up of parameters designed to assess specifications, adherence to design tolerances and any other advantages quantified in the test laboratory. Theoretical performance merits could include wavefront RMS and spherical aberration, and this could be verified by interferometry in the testing lab.
Evaluating design compensations with the VMCP is straightforward. Optical elements for assembly are chosen from the Lens Manufacturing Database before an implemented LMD enables this process via a point and click user interface (Figure 3).
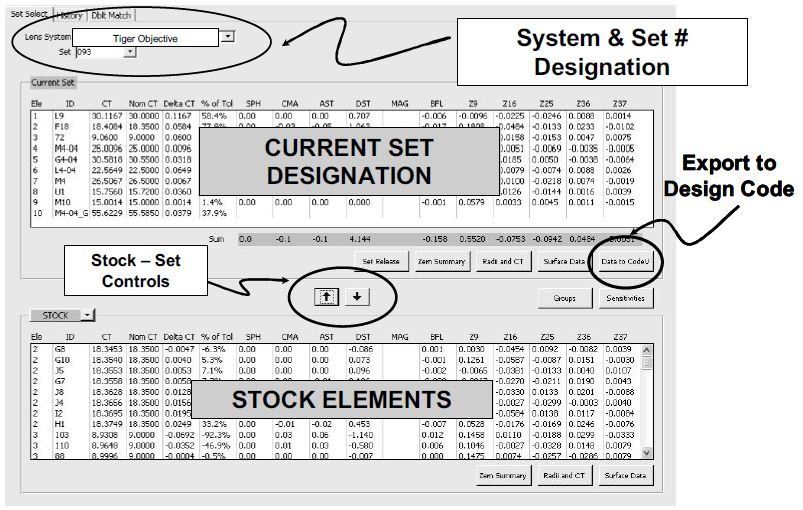
Figure 3. Project Element Selection Interface in LMD. Image Credit: Corning Incorporated - Advanced Optics
Components are organized and grouped by their project designated set number, or by available stock. Each lens component is analyzed according to manufacturing specifications with any potential impact on performance computed.
The information gained is then quickly utilized to ascertain any change in resulting from a specific component being inserted into a lens assembly. The lens set’s manufactured data (radius, ct, index, etc.) can then be exported to optical design code for appropriate analysis and optimization.
Additional set unique mechanical and as-built air space data, which has been stored in the assembly mechanical report, may be exported before being combined with the element LMD information and compensated with the VMCP.
Following the lens compensation phase, performance merits are measured against the threshold criteria. If acceptable performance is achieved, the manufacturing solution is reported and then released to assembly (Figure 4).
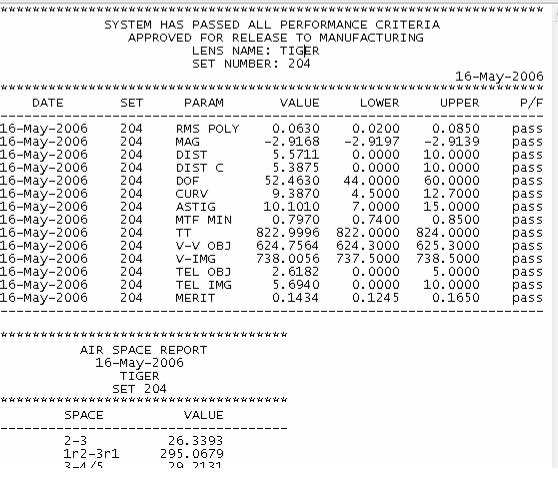
Figure 4. Objective performance and solution report. Image Credit: Corning Incorporated - Advanced Optics
If the design does not achieve satisfactory performance, the solution is not released to manufacturing. Additionally, the user is prompted to adjust the mix of selected elements before re-running the compensation.
The VMCP includes history information. Every time a lens system is run on the platform, compensation and performance data is stored in an archive. Historical project data can then be retrieved and reviewed to examine manufacturing performance patterns or trends, adherence to specification and other useful statistics.
Design Transition to Volume Production
VMCP architecture facilitates straightforward transition of lens system support from prototype to largescale production. This platform provides a number of advantages to the manufacturing community. Manufacturing staff can take on various routine project support design duties which have historically only been performed by optical designers.
This lessens dependency of manufacturing on engineering staff for everyday project support. The design compensation cycle time is significantly decreased as the process is automated. Within a project, each system is consistently compensated using the same suite of tools, variables, and methodology. Several users can be trained to run the VMCP with ease, granting an additional layer of staff versatility within programs.
Each project maintains its own individual, customized compensation strategy and distinct set of performance merits.
Threshold criteria determine whether or not it is acceptable to build a specific lens set. This removes many subjective performance decisions which are normally made by an optical designer. However, modifications and alterations in compensation philosophy should be evaluated by an optical designer prior to implementation into the VMCP.
Summary
As can be seen here, a manufacturing compensation and analysis stream was developed to aid in the manufacturing support tasks related to production optical systems. This model can be used to transition/transfer optical designer engineering system support activities to other manufacturing personnel.
This may involve the selection of system parts for assembly, analysis, and compensation of these parts before any commitment to building. It is possible for manufactured lens data and mechanical assembly measurements to be built into design models, allowing predictions of performance levels that could be achieved by a particular assembly.
Where performance is satisfactory, the parts can then be released for assembly. This streamlined process bypasses engineering involvement in production activities, allowing manufacturing to easily transition designs from prototype to largescale production.
References
- Tienvieri, C., et al, “Modern lens design using a lens manufacturing database”, SPIE Proceedings, IODC 1998, vol 3482, pp. 508-518.
Acknowledgments
Produced from materials originally authored by C. Theodore Tienvieri and Tim Rich from Corning Tropel.
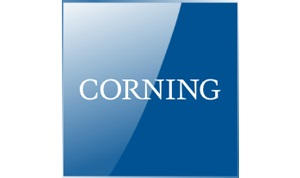
This information has been sourced, reviewed and adapted from materials provided by Corning Incorporated - Advanced Optics.
For more information on this source, please visit Corning Incorporated - Advanced Optics.