The SLM-310 is an LCOS-based spatial light modulator designed for high laser power durability, supporting 1 kW near-infrared lasers at 1064 nm. It offers precise beam control through 10-bit (1024 grayscale levels) modulation, enabled by its high WUXGA (1920×1200) resolution and excellent phase stability, with a typical value of < 0.003π.
Equipped with a robust water-cooling system, the SLM-310 integrates into laser processing equipment used for welding, drilling, cutting, and metal 3D printing. It enhances processing accuracy, reduces thermal effects, improves beam shaping, enables steering correction, and supports multi-beam control.
Features
- Extended SDK with example code in C#, MATLAB, Python, LabVIEW, and more
- Extended flexible cable for versatile installation
- Built-in memory and I/O trigger functions
- Professional, timely technical support to assist with testing and integration
- Stable operation with integrated water-cooling system
- Phase stability: < 0.003π (typical)
- Resolution: WUXGA (1920×1200)
- Gray level: 10-bit (1024 levels)
- Laser power durability: up to 1 kW
- Wavelength range: 1020–1100 nm
Application
- Metal 3D printing and additive manufacturing
- Wafer cutting and dicing
- Pulse shaping and beam shaping
- Wavefront correction
- Laser material processing: welding, cutting, drilling, chamfering, film removal, surface treatment
Expected Benefits of Spatial Light Modulators in Metal Processing
Improved Processing Precision
Spatial light modulators enable dynamic beam profile adjustments, allowing for highly accurate processing. The SLM-310 delivers a level of precision in fabricating intricate metal parts and fine structures that is difficult to match using conventional methods, helping ensure consistent production of high-quality components.
Faster Processing and Beam Shaping for Increased Efficiency
With the SLM-310, laser irradiation patterns can be rapidly adjusted, reducing overall processing time. Techniques such as donut- or ring-shaped beam configurations help enhance speed while limiting unnecessary heat input, improving processing efficiency.
Simultaneous Multi-point and Multi-region Irradiation
The SLM can divide a single laser beam into multiple points, each with a distinct pattern, enabling the simultaneous processing of several areas. This capability shortens takt time and significantly increases throughput.
Minimized Thermal Effects on Materials
By controlling laser energy distribution with precision, the SLM-310 delivers heat only where needed. This targeted application helps lower spatter, improve processing quality, and reduce the need for post-processing, while preserving the integrity of heat-sensitive materials.
Specifications
Source: Santec Corporation
Item |
min. |
max. |
Units |
Notes |
Wavelength |
1020-1100 |
nm |
|
Panel Size |
(H) 15.36 x (V) 9.60 |
mm |
Active area |
Pixel Resolution 1) |
(H) 1920 x (V) |
1200 |
pixel |
Pixel Size / Pitch |
7.8 / 8.0 |
μm |
|
Panel Reflectivity 2) |
Typ. > 92 |
% |
|
Aperture Ratio |
95 |
% |
|
Gray Level |
10 (1024) |
bit |
|
Frame Rate |
60 or 120 |
Hz |
Factory setting, default 60 Hz |
LCOS Drive Frequency |
1200 |
Hz |
|
Phase Depth |
2π |
- |
rad. |
|
Phase Stability |
Typ. < 0.003π |
rad. |
|
Response Time 3) |
Tr: 250 / Tf: 350 |
ms |
|
Interface |
DVI* / USB 3.0 |
- |
*10-bit using RGB 8-bit, 3 colors |
Operating Temperature
Range |
15 |
35 |
℃ |
No condensation |
Storage Temperature |
0 |
40 |
℃ |
No condensation |
Optical Power Handling 4) |
- |
1000 |
W |
CW @1064 nm |
Dimensions |
117.6 x 117.6 x 33.7 |
mm |
|
Control software |
GUI software and
SDK for Windows |
- |
|
Water Flow |
8 |
L/min. |
15 - 25 ℃ |
Water Inlet and Outlet |
Pipe fittings |
- |
Rc(PT) 3/8 inch female 5) |
1) Pixel defects are not warranted.
2) Zero-order reflection. Depending on wavelength range.
3) Response time is a typical value and is not affected by frame rate.
Tr: Rise time between 10 % and 90 % levels in a phase change of 0 to 1023 bit (2π rad.) at 25 ℃.
Tf: Fall time between 90 % and 10 % levels in a phase change of 1023 to 0 bit (2π rad.) at 25 ℃.
4) The value is not guaranteed. Depending on the conditions of the laser oscillator used, the product's life may be significantly shortened due to accumulated exposure time.
5) Supports NPT standard using attached conversion adapters.
Application
Laser Welding Simulation
This simulation illustrates how precise control over the beam profile enhances laser welding performance. By refining the beam’s intensity distribution, improvements can be achieved in both quality and efficiency, such as (1) reduced spatter formation, (2) minimized bubbles and voids within the weld, (3) less visible weld marking, and (4) increased welding speed.
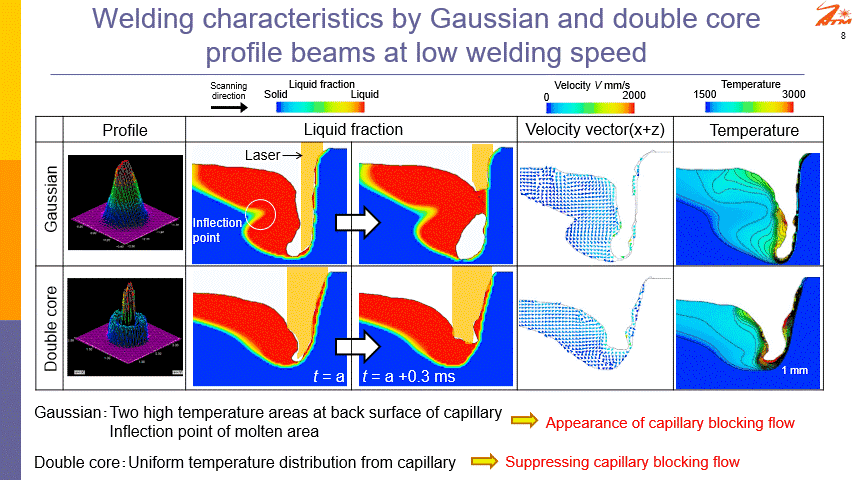
Video Credit: Okayama University Dep. of Mechanical Eng. Nontraditional Machining Laboratory Dr. Yasuhiro.Okamoto