In a study published in Applied Sciences, researchers have proposed an automatic evaluation method based on 3D laser scanning technology to measure the geometric accuracy of subway stations. The technique enables high precision and all-around geometric evaluation of underground systems.
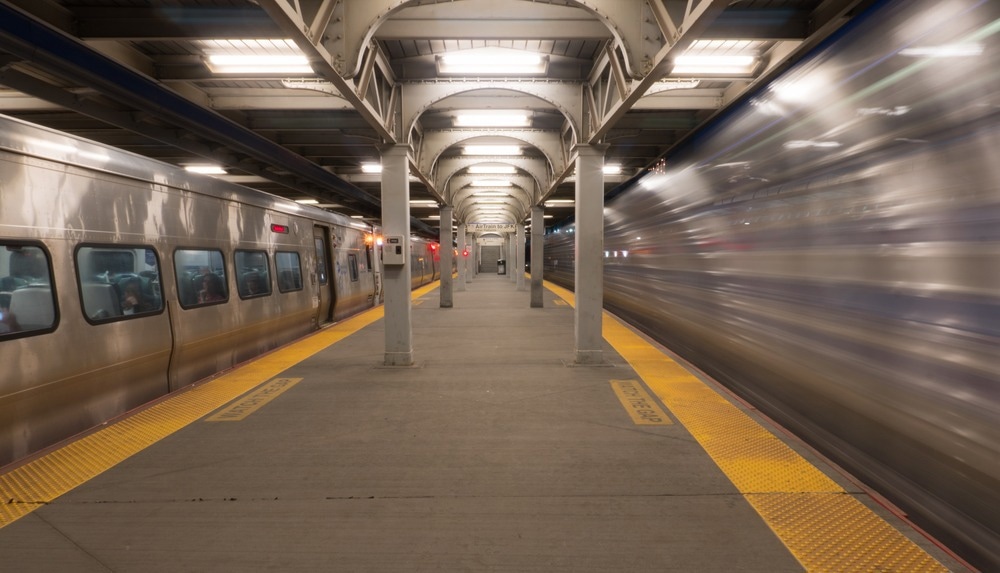
Study: Geometric Accuracy Evaluation Method for Subway Stations Based on 3D Laser Scanning. Image Credit: BrandonKleinPhoto/Shutterstock.com
Subway Station Construction
Subway train systems have quickly advanced globally, considerably easing daily commuting and promoting economic growth. The development of subway stations is essential to the success of underground rail networks.
However, building subway stations is technically demanding and challenging. Geometric precision is crucial while building urban subway systems. Subway station construction involves several dynamic processes.
The accurate evaluation and efficient construction monitoring of subway stations are critical to ensuring the quality of subway stations and avoiding construction complications.
Construction Monitoring Methods and Their Limitations
Traditional subway station construction monitoring depends on point-to-point measurements by workers using total stations or steel rulers.
However, the construction site is complicated, and the target sites to be measured are scattered in regular or irregular surface patterns, making it impossible for conventional measuring methods to get comprehensive measurements of the building's surface.
3D laser scanning enabled the fast, high-precision, and panoramic acquisition of object surface information. As a result, it is extensively used in numerous civil engineering applications, including automated construction and modeling, managing construction safety and progress.
In addition, some researchers have employed laser scanning techniques in project quality inspection to identify possible construction quality issues by comparing the project infrastructure's position, shape, and size parameters with design models.
However, when design building information modeling's (BIM) survey coordinate system is not implemented during data acquisition or lost during the interaction, the subject's coordinate positions will differ between the BIM and point cloud, reducing the accuracy of the 3D laser scanning instrument.
Current accuracy inspection methods are developed for the precise assembly of prefabricated parts, and they cannot evaluate the geometric correctness of the entire subway station's building site. Evaluation systems and systematic evaluation indexes must be developed beforehand to give effective direction for the accurate geometric evaluation of the subway stations.
Various researchers have attempted to mitigate the potential difficulties during subway station development by regulating assembly accuracy or using prefabricated component technologies. However, these techniques focus on the accuracy control of limited regions and do not include a complete assessment of the subway.
Using 3D Laser Scanning-Based Technology for High Precision Geometric Evaluation of Subway Systems
The successful integration of point cloud and BIM to a single survey coordinate reference was proposed using a coarse-to-fine registration approach. Researchers used an inner wall line-based iterative closest point (PL-ICP) algorithm to obtain fine registration.
The PL-ICP algorithm employs the point-to-line distance as the error measurement function. The point cloud serves to extract the structural features of the subway station.
Through statistical analysis and visualization, a hierarchical evaluation index and a method adaptable to the subway's structural surface were developed to accomplish a practical geometric evaluation.
Study area
Researchers applied the proposed method to evaluate the Hongqi Road subway station's (China) geometric accuracy to test its efficacy.
Significant Findings of the Study
The proposed laser scanning method rectified the inconsistent coordinate reference problem between the point cloud and design BIM. The structural column accuracy and surface accuracy evaluation were completed using evaluation indices.
The over-limit locations can be identified automatically, and structural column deviations can be quantified using statistical visualization and analysis. The coarse-to-fine registration accuracy was 17.8 ± 0.94 mm. High-level precision was observed at large-scale subway stations with floor surface sizes of more than 10,000 m2.
PL-ICP is a powerful algorithm that can successfully reduce the impact of outlier points (incorrectly positioned walls) on the same results. This algorithm implies that the registration involves only the correct position construction. However, the transmission and accumulation of deviations will still increase the structural column deviation.
Grid-based coarse matching cannot be employed when construction items do not fit cleanly with the subway station's grid. Then, coarse matching has to be performed manually.
The resulting deviation distributions of the four facades in the north, west, east, and south were relatively similar. The deviation ranges were very small, which verified the accuracy of the proposed coarse-to-fine registration method.
The successful deployment of this technology in the Hongqi Road subway station in China verified its practical viability.
Reference
Wang, Q., Qian, P., Liu, Y., Li, T., Yang, L., & Yang, F. (2022). Geometric Accuracy Evaluation Method for Subway Stations Based on 3D Laser Scanning. Applied Sciences. https://www.mdpi.com/2076-3417/12/19/9535
Disclaimer: The views expressed here are those of the author expressed in their private capacity and do not necessarily represent the views of AZoM.com Limited T/A AZoNetwork the owner and operator of this website. This disclaimer forms part of the Terms and conditions of use of this website.