In a pre-proof article recently published in the journal Optics & Lasers Technology, researchers discussed the utility of machine learning and molecular dynamics in the optimization of the multistage femtosecond laser drilling process.
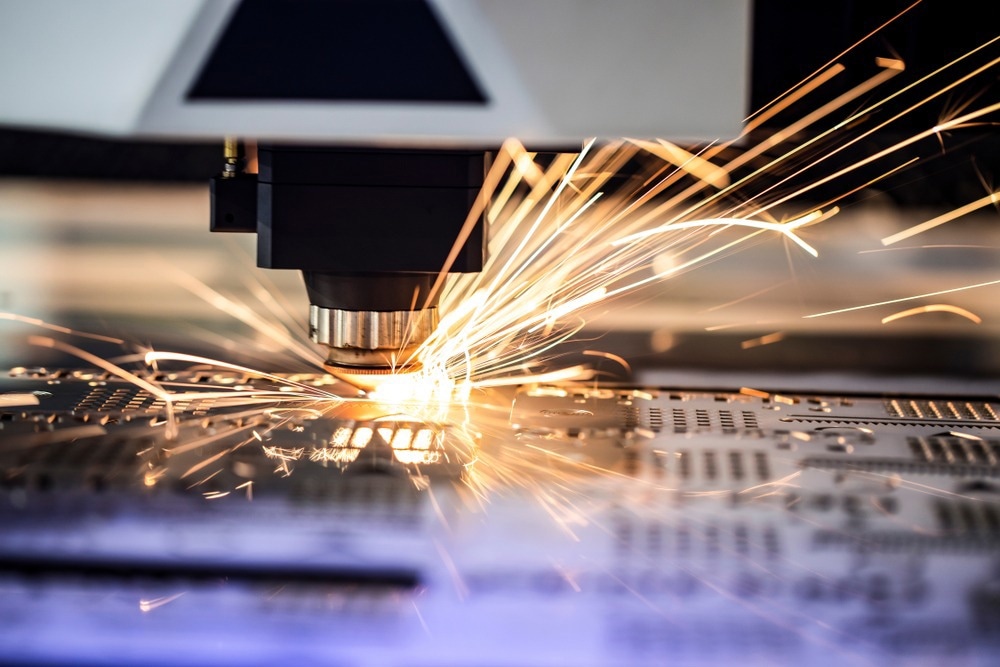
Study: Optimization of multistage femtosecond laser drilling process using machine learning coupled with molecular dynamics. Image Credit: RUl8let/Shutterstock.com
Femtosecond Laser Percussion Drilling
Due to its high accuracy, high efficiency, and minimal thermal damage, femtosecond laser drilling is becoming increasingly popular across various engineering sectors.
In essential manufacturing industries, femtosecond laser percussion drilling is frequently employed as a dependable micro-hole processing technique. However, the laser percussion drilling method still faces several difficulties, significantly reducing the micro-holes' precision and caliber. Laser machining has a complicated variable system, making the worldwide quantitative optimization of the processing parameters for laser machining challenging.
Theoretical calculations, such as molecular dynamics (MD) and the two-temperature model (TTM), lead the optimization process. For complex drilling techniques, a more thorough tiered approach is required. Unfortunately, TTM-molecular dynamics cannot offer any more direct quantitative advice for process design or optimization as an ideal model.
Machine Learning in Laser Material Processing
Recently, machine learning and global optimization algorithms have become widely applied in the field of laser material processing to achieve high-efficiency and low-cost process optimization, overcoming the shortcomings of the conventional trial and error approaches or physical models. Because machine learning can analyze data, it is possible to build a quick and precise correlation between laser parameters (inputs) and target machining performance (outputs). Consequently, machine learning and optimization algorithms are trustworthy approaches for process optimization (including drilling) in laser material processing.
In this study, the authors proposed a process optimization framework incorporating machine learning, molecular dynamics simulation, and a high-throughput optimization algorithm for femtosecond laser percussion drilling process optimization.
The data set utilized to train the machine learning model was enriched by the physical information discovered by molecular dynamics, which lowered the amount of data needed.
High-throughput optimization algorithms were in charge of choosing the best process in the process space after the fast and reliable establishment of the regression model between target machining performance and laser parameters.
Novel Four-Stage Drilling Process
For femtosecond laser percussion drilling, a novel four-stage drilling process was presented and optimized, utilizing the coupled process optimization framework to overcome efficiency and quality challenges. The experimental validation confirmed the reliability of the optimized method for the Ni-based single crystal superalloy. The framework could be expanded to other complex systems to implement process optimization in laser material processing technology with low cost and high efficiency.
The team combined a TTM-molecular dynamics model, machine learning, and a high-throughput optimization algorithm to offer an optimization strategy for the femtosecond laser machining process. The suggested method optimized a four-stage femtosecond laser percussion drilling process, which significantly improved the material removal rate and the recast layer.
The four-stage femtosecond laser percussion drilling process was successfully built using the coupling process optimization framework, and the processing quality and efficiency of micro-holes have been greatly enhanced. Furthermore, experiments were used to confirm the robustness of the optimized procedure.
Efficiency of the Proposed Four-Stage Drilling Process
The taper degree was decreased to 2.19°, and the designed plan's material removal rate and recast layer thickness were 2.61 x 108 μm3/s and 2.03 μm, respectively.
The addition of physical data from TTM-molecular dynamics significantly raised the machine learning model's predictive accuracy and ensured the process design's dependability.
Ideas for resolving the issue of small samples were provided by the reliable physical variables supplied by the physical model. These solutions could be applied to more sophisticated laser processing techniques. It was also feasible to fully comprehend the physical importance of the optimized process thanks to the addition of physical variables.
According to the statistical results of the optimized process physical factors, it was appropriate to guarantee the most significant number of clusters, vapor-phase atoms, ablation ratio, and the smallest average cluster size at each drilling step.
A phased drilling strategy led by machine learning was required in place of traditional drilling technology, as seen by the difference in ablation behavior and final micro-hole quality. To maximize the quality and effectiveness of micro-holes, more studies could be directed toward the machine learning-led femtosecond laser drilling method with continually changing process parameters.
Conclusions
This study elucidated a femtosecond laser machining process optimization framework that combined TTM-molecular dynamics, machine learning, and a high-throughput optimization algorithm.
The suggested framework was successfully used to optimize a new, four-stage femtosecond laser percussion drilling technique, improving quality and efficiency.
The authors mentioned that this study's coupling framework offers a viable approach for optimizing effective and affordable complex laser processing technology.
They stated that a machine learning model must be trained using a significant amount of experimental data. These drawbacks significantly constrain the widespread use of machine learning in laser machining. It also makes laser machining processing modifications expensive and inefficient.
The researchers emphasized that this study significantly reduced the data needed to train a machine learning model using a molecular dynamics model to provide intermediate parameters. Therefore, the processing modification of laser machining is significantly more effective and affordable owing to the proposed design method.
Reference
Wang, C., Zhang, Z., Jing, X., et al. (2022) Optimization of multistage femtosecond laser drilling process using machine learning coupled with molecular dynamics. Optics and Lasers Technology. 108442. https://www.sciencedirect.com/science/article/abs/pii/S0030399222005990
Disclaimer: The views expressed here are those of the author expressed in their private capacity and do not necessarily represent the views of AZoM.com Limited T/A AZoNetwork the owner and operator of this website. This disclaimer forms part of the Terms and conditions of use of this website.