3D printing offers almost limitless freedom of design using a continuous process and the ability to print products directly on a range of substrates, resulting in a functioning, ready-to-use element.
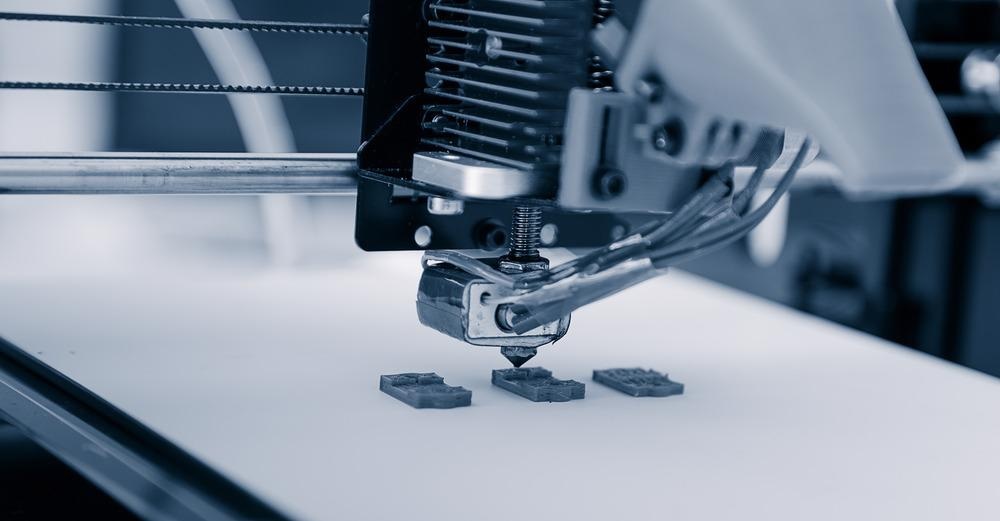
Image Credit: Alex_Traksel/Shutterstock.com
The 3D printing process is based on layers of materials. 3D printing optical devices helps fabricate 3D helical structures, beam-driven submicron probes, photonic crystals, and confocal imagers, overcoming the constraints of conventional planar patterning techniques.
New advances and future research are developed in the additive manufacture of functional optics, such as lenses, photonics, optoelectronics, and metamaterials. 3D printing offers cost-effective, practically limitless design freedom and extra material flexibility on being directly printed on a range of substrates, resulting in a fully functioning 3D-printed part.
3D Printing Optical Lens: Macro, Micro, and Nanoscale Lens
3D printing has proved the capacity to produce a wide range of freeform optical elements with submicron quality features and high optical performance. Dimensional precision and surface smoothness seem to be two characteristics that play a key role in producing high-quality optics.
Polydimethylsiloxane (PDMS) is an optically transparent ingredient for macroscale lenses and has become an exciting material for dropwise 3D printing to develop the complex surface morphology necessary for high optical performance.
Using 3D printing technologies with faster production rates and cost-effective material prices, new high-quality optics may be produced, resulting in greater precision of micro and nano features.
Using modern 3D printing technology, custom lenses of steep gradients, highly regulated surface roughness, and complex micro and nanostructures, which are difficult to make using conventional manufacturing techniques, may be effectively fabricated.
3D Printing on Photonics
3D printing is also instrumental in photonics production. Photonics may be utilized for more than transferring signals to electronics. Photonics is also used to capture sceneries in 3D imaging.
To produce structural colors by emulating natural patterns and material systems, many alternative 3D printing processes have been explored. Self-assembling nanostructures and bioinspired objects, for example, might be manufactured using a commercially fused deposition modeling FDM 3D printer with a color representation.
A grating surface was initially created by nanoimprinting. Ink was then dropped onto the grating surface, and finally, a laminate index-matching polymer was placed on top.
3D Printing on Optoelectronics
Optoelectronic instruments are transducers that convert photons to electrons, lights to an electrical current, or vice versa. As a revolutionary production technique, 3D printing technology offers significant promise for developing optoelectronic devices.
The newly proposed method permits the coupling of polymer nanowire waveguides with any object without physical touch, facilitating the simplicity of photonic circuit designs and the enhancement of integration density.
Further advancement of the 3D printing process will give a tool for the unorthodox construction of LEDs. Several methods for producing LEDs by integrating active nanoelectronics, such as employing an extrusion-based 3D printing (EBP) based 3D printing process, demonstrate the adaptability of printing various kinds of material.
In addition to creating 3D printing processes for LED production, several studies concentrate on discovering LED 3D printing materials. Thermoplastics are often used as filament in fused deposition modeling (FDM) printers. Future testing of various solutions or material mixes will determine the best combination and concentration for optoelectronics 3D printing.
3D Printing of Metamaterials
Optical metamaterials are innovative artificial structures made up of subwavelength components. Negative refractive index, dielectric constant, permeability, and inverse Doppler effect are some of the exceptional physical qualities of optical metamaterials that standard materials cannot match.
The inherent characteristics of the unit materials do not affect the properties of metamaterials; instead, the form and distribution of the unit structures do. An ultra-thin arching stealth carpet cloak appropriate for microwave band was produced by merging 3D printing process with liquid metal injection molding.
3D printing enhances the diffraction effectiveness of multilayered diffractive lenses featuring high resolution. It provides a quick and cost-effective method for creating complicated lenses—further development from the micro to the macro fields, as from classical to the quantum optical fields. The relevant spectral range will be extended further, and additional supernatural and peculiar properties will be achieved.
3D Printing Applications: Rapid Prototyping
Rapid prototyping is the rapid production of a physical component, model, or installation utilizing computer-aided design (CAD) in the 3D printing process. The item, model, or assembly is often completed via an additive manufacturing process, also known as 3D printing. Rapid prototyping continues to be the most popular use for 3D printing technologies.
The Benefit of 3D Printing Further Advancement
Lead times and inventories may be minimized with 3D printing technology. This is perceived as an even more significant advantage in the industrial products industry, with almost 60% identifying lead times as a benefit. Optics is a substantial field of science. The additive manufacturing process, often known as 3D printing, is a new manufacturing technology that offers advantages such as great dimensional precision for optics functional.
References and Further Reading
Shaik, Y., et al. (2021). 3D Printing under High Ambient Pressures and Improvement of Mechanical Properties of Printed Parts. https://doi.org/10.3390/jcs6010016
Zhu, Y., et al. (2022). Recent advancements and applications in 3D printing of functional optics. https://doi.org/10.1016/j.addma.2022.102682
Disclaimer: The views expressed here are those of the author expressed in their private capacity and do not necessarily represent the views of AZoM.com Limited T/A AZoNetwork the owner and operator of this website. This disclaimer forms part of the Terms and conditions of use of this website.