In a study published in Minerals, a 3D laser scanning technology-based deformation measurement and monitoring method is proposed for safe and effective tunnel construction. A greedy triangulation and B-spline interpolation were used to fit the tunnel point cloud and characterize the tunnel deformation.
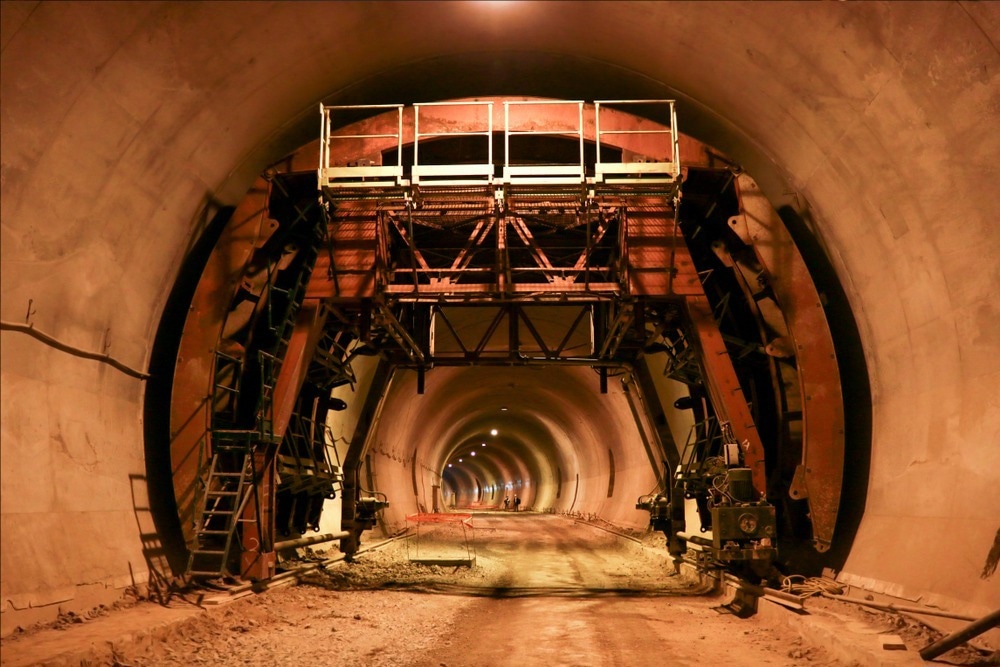
Study: Research on Tunnel Construction Monitoring Method Based on 3D Laser Scanning Technology. Image Credit: Sasa Dzambic Photography/Shutterstock.com
New Austrian Tunneling Method
Tunneling is a dangerous but rapidly growing sector in the construction industry. It is regarded as one of the most challenging construction methods due to the presence of debris material, shear zones, water channels, and the unpredictable behavior of the rocks during the construction phase.
An efficient and safe procedure is necessary for saving time while providing a safer workplace for construction.
The new Austrian tunneling method is regarded as the most efficient technique in geologically diverse regions as it employs an analytical approach. However, the new Austrian tunneling method necessitates efficient tunnel monitoring and measurement for estimating tunnel deformation.
Significance of Monitoring and Measurement in Tunnel Construction
Tunnels are symmetrical constructions that must withstand unpredictable loads. Therefore, monitoring and measuring the deformation and stability of the surrounding surface, rock, and supporting structure is crucial to collecting the necessary information for safe tunnel construction.
Current Monitoring and Measurement Methods and their Limitations
A total station is often used for monitoring and measurement, with reflective indicators at the measuring stations. However, this method has significant drawbacks, including:
- Falling vault blocks cannot be avoided because of the limited number of measurement locations.
- Construction blasts and pollutant reflectors invalidate monitoring and measuring results.
- The lengthy monitoring and measuring method compromises the inspectors' health and safety and slows construction.
- The biased tunnel measuring points' deformation is inaccurate, causing measurement and monitoring results to be misinterpreted.
3D Laser Scanning Technology
3D laser scanning enables contactless measurements and can directly generate enormous 3D data clouds with irregular spatial distribution. It can also penetrate rocks and is less susceptible to environmental factors.
Due to its strong environmental adaptability, high level of automation, fast detection speed, and good adaptability, 3D laser scanning technology has been increasingly used in tunnel construction. It aids in identifying over and under excavation by comparing the tunnel's design surface to the predicted model by the point and fitted point cloud.
However, 3D laser scanning faces two significant obstacles: abnormal denoising points and random distribution of point clouds.
Using Spline Interpolation and a Greedy Triangulation with 3D Laser Scanning to Assess and Forecast Tunnel Deformation
3D laser scanning obtained distributed clouds of irregular surroundings and structures in the new Austrian tunneling method. The tunnel surfaces were fitted using a greedy triangulation and B-spline interpolation to address the scattered point cloud analysis issue.
The tunnel fitting surface deformation was inventively expressed using the normal vector matrix, which resolved the issue of scattered point clouds in three-dimensional laser scanning.
The maximum entropy method computed the deformation eigenvalues and the normal vector's probability density function. The deformation eigenvalues generated a curve to forecast and assess tunnel deformation.
Significant Findings of the Study
The values of the greedy triangulation method corresponded well with the fitting surface, demonstrating a better fit than those of the B-spline interpolation method. In addition, the fitted surface's triangles' curvature was reduced as the point cloud density increased.
When the sudden shift in curvature is minor, tunnel displacement and tunnel surface deformation are perpendicular to the tunnel's surface. However, this is only valid if the tunnel is sufficiently flat before monitoring.
By removing the aberrant points brought on by the tunnel surface's lack of flatness, the maximum entropy approach can reliably determine how the tunnel has deformed. However, the maximum entropy method's calculation of the probability density function does not converge when the tunnel deformation and normal vector are small.
Accurate assessment and measurements can be carried out using either the 1% or 5% feature deformation values. However, the exceedance probability is more likely to be disrupted by construction variables when it is too low. The deformation value based on the 5% probability feature may better represent the deformation of each tunnel segment.
In future studies, researchers will implement AI systems to determine the change in the standard vector matrix and the probability density function for estimating the tunnel's deformation trend.
Reference
Wei, Z., Wang, Y., Weng, W., Zhou, Z., & Li, Z. (2022) Research on Tunnel Construction Monitoring Method Based on 3D Laser Scanning Technology. Symmetry. https://www.mdpi.com/2073-8994/14/10/2065/htm
Disclaimer: The views expressed here are those of the author expressed in their private capacity and do not necessarily represent the views of AZoM.com Limited T/A AZoNetwork the owner and operator of this website. This disclaimer forms part of the Terms and conditions of use of this website.