A pre-proof study from the journal Materials Science and Engineering: A utilized a neutron diffraction method and FEM simulation to demonstrate that substrate characteristics can alter the residual stress created within direct energy deposition parts.
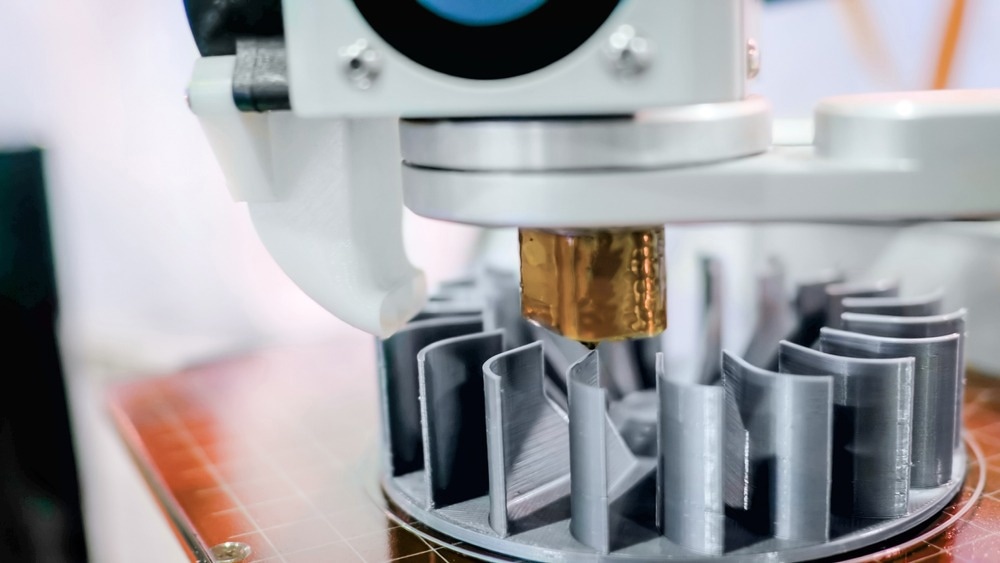
Study: Effect of substrate yield strength and grain size on the residual stress of direct energy deposition additive manufacturing measured by neutron diffraction. Image Credit: Zyabich/Shutterstock.com
The direct energy deposition (DED) process can produce near-net-shaped items and repair damaged ones. Residual stress is generated inside the parts processed with this method.
In an upcoming study, researchers have used a softer substrate with larger grain sizes and low yield strength to lower residual stresses in direct energy deposition parts.
Residual Stress and its Significance in Metal Additive Manufacturing
Direct energy deposition (DED) is a novel metal additive manufacturing process using metal powder as the feedstock. It melts the deposited metal powder by exposing it to a concentrated laser source.
Compared with other metal additive manufacturing processes, direct energy deposition machines are more straightforward, enabling the direct application of the DED process to existing parts. It makes them an excellent choice for parts maintenance and feature addition procedures.
However, rapid and repeated temperature variation during the direct energy deposition process causes the surface temperature to change quickly.
Rapid cooling induces compression in the center of the material.
The outer surface is a restraint on the material in the core as it seeks to cool. As a result, residual tensile stress is generated in the inner region, whereas the outside portion will have residual compressive stress.
Even in the absence of temperature gradients or external loads, these stresses persist in a solid material.
Residual stress substantially impacts the corrosion resistance, dimensional stability, crack development, and mechanical characteristics of metal additive manufacturing samples. It can cause undesired internal cracks or distortion in the geometry of the parts.
The material is permanently deformed when the residual stress exceeds the yield strength. This leads to deflection when the portion separates from the base plate.
Residual stress can be seen as a crucial element in cost management and improving the effectiveness and quality of products. However, evaluating residual stress in metal additive manufacturing processed parts remains difficult.
Limitations of Traditional Residual Stress Measuring Techniques
X-ray diffraction, contour, and hole-drilling methods were previously utilized for determining residual stress. However, X-ray diffraction is solely applicable to subsurface analysis, while contour and hole-drilling techniques can produce inaccurate results due to their destructive measurement methodologies.
Measuring Residual Stresses Using Neutron Diffraction Method
The pre-proof study published in Materials Science and Engineering: A used a non-destructive neutron diffraction method to measure the residual stresses induced during the direct energy deposition process. The neutron's lack of electric charge allows it to penetrate deeper into the material.
The substrates were 10 mm-thick stainless steel plates. The direct energy deposition samples were heat-treated to create two distinct substrates with varied grain sizes and yield strengths to evaluate the influence of the substrate properties on the residual stresses created during direct energy deposition.
Finite element method (FEM) simulations helped study the evolution of residual stresses and the influence of the substrate’s yield strength on the residual stresses of direct energy deposition parts.
The FEM analysis was compared with the residual stress values obtained experimentally.
The electron backscatter diffraction (EBSD) method examined the microstructures of the deposited metal and the stainless steel substrate. Both non-heat (NH) treated and heat-treated (HT) stainless steel substrates were subjected to tensile tests to validate their mechanical properties.
Important Findings of the Study
The majority of the direct energy deposition deposit developed compressive residual stresses as the deposit's height increased, while tensile residual stresses were generated closer to the top surface.
Neutron diffraction and FEM simulation demonstrated that the substrate's yield strength and grain size influence the magnitude of residual stress generation in the deposited metal and stainless steel substrate.
Comparing the residual stresses of the NH and HT stainless steel substrates revealed that the HT substrate has significantly lower residual stresses than the NH substrate. The substrate's low yield strength permits more thermal shrinkage compensation during the direct energy deposition process, lowering residual stress.
The substrate characteristics influence the grain size and texture of the direct energy deposition-deposited metal because of epitaxy development at the deposit-substrate interface.
The grain size influences the yield strength, but the texture affects the resistance to plastic deformation, influencing the residual stress.
However, these microstructural variations had no significant effect on the tensile characteristics of the direct energy deposition deposits.
This work demonstrated that the change in characteristics of the substrate could be used to lower the residual stresses of the direct energy deposition deposits and enhance the quality of the part.
This method can be used when typical stress reduction techniques, such as preheating and post-annealing, are not feasible.
Reference
S.G. Jeong, S.Y. Ahn, E.S. Kim, G.M. Karthik, Y. Baik, D. Seong, Y.S. Kim, W. Woo, H.S. Kim. (2022) Effect of substrate yield strength and grain size on the residual stress of direct energy deposition additive manufacturing measured by neutron diffraction. Materials Science & Engineering: A. https://www.sciencedirect.com/science/article/pii/S0921509322010164
Disclaimer: The views expressed here are those of the author expressed in their private capacity and do not necessarily represent the views of AZoM.com Limited T/A AZoNetwork the owner and operator of this website. This disclaimer forms part of the Terms and conditions of use of this website.