May 22 2012
Just pieces of wood? Think again.
The production of parquet wood flooring places high demands on the quality of the raw material. A machine vision system utilizing five IDS cameras is checking parquet wood to capture any defects, helping a German flooring manufacturer maintain its profitability and reputation.
The Reinlein Parkett Company maximizes the capabilities of its premises. Large stacks of wood fill up almost every inch of space. Enough wood for a half a year of production is kept here to dry. The path to the machine vision system passes numerous machines in the large hall that process the raw material. Debarked trunks are sawed into planks and then cut into boards for various wood flooring types. Boards of low quality end up as 16 cm long, 3 cm wide pieces of wood, literally puzzle pieces for composite or mosaic parquet.
"Mosaic parquet is actually made from wood scraps. If it can't be used whole, it's sawed into blocks," explained George Blank, the CEO of ATB Blank imaging specialist who's company designed the machine vision system for Reinlein Parkett. "This means that a parquet manufacturer has to check closely to determine which of the so-called slats are suitable for the classy floor covering. The test criteria are dimensional stability, color, sapwood, knots and cracks. If a piece of wood exhibits a flaw, it may at best still be acceptable for industrial parquet laid edgewise."
Prior to installing its new machine vision system, Reinlein Parkett sorted pieces of wood by eye and by hand. The blocks dropped onto a conveyor belt, and up to three employees would separate them into three lanes according to their quality. Additional employees carried out follow-up checks to ensure that flawed pieces don't end up in the final product. This was a tedious process and only took one side of the pieces into consideration. Cracks in the end faces or knot holes on the underside could slip through undetected.
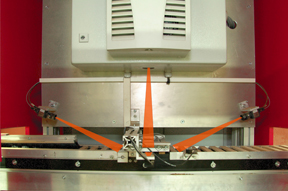
To improve cycle rate and production quality, the company hired ATB Blank to install an ARGUS Spectra vision system that checks each piece of wood with five IDS cameras.
"The Reinlein company is one of the last manufacturers of mosaic parquet in Germany," explained Blank. "The price pressure from abroad is enormous. Thanks to the testing system, efficiency has increased considerably, and quality flooring remains affordable."
The system quality checks about 140,000 square meters of parquet annually, an area that corresponds to more than 20 football fields. And not even the smallest detail can slip through the cracks.
Here is how it works: A conveyor belt pushes up to ten pieces per second through the testing system under the watch of the IDS cameras. Two light barriers send an electrical trigger signal to all five cameras as soon as a piece of wood moves into the field of view. The image field of the CCD and CMOS sensors is limited in height by an AOI function (Area Of Interest), whereas the full image width is utilized. This increases the speed and reduces the data quantity and computer load simultanuously. At a rate of 50 images per second, the programs only use up about half of a conventional PC's resources. In fact, the IDS USB 2 uEye SE cameras could run at twice this speed, but the system can't physically feed and unstack wood pieces faster.
One color camera and four monochrome cameras capture every piece. The movements are fast, which is why the light-sensitive sensors are only exposed for a few hundred microseconds. Four rails with white LEDs light up all the sides of the wood strips. Two CCD models of type UI-2230SE-M monitor the long sides. Their primary task is to detect cracks that are almost indistinguishable from the natural grain of the wood. The XGA sensors resolve details of the wood structure down to 0.16 mm using 1,024 x 768 pixel resolution. Whether or not the dimensional stability is in line with the required 100 µm is also checked on all sides.
Blank chose two UI-1220SE-M CMOS cameras for the short ends of the slats. Both feature global-shutter sensors, which is important for capturing quick movement. Through the smaller field of view, the 768 pixel-wide image capturing device achieves speeds four times higher than the other three cameras.
To George Blank, precision is not only a question of resolution. Just as important is the workmanship of the camera, so as to ensure that the flange focal length is correct and the sensor is positioned precisely on the focal plane. He praised the precise and robust uEye housing design. On other cameras, he said, the sensors were apparently mounted too low, which caused the image to be blurry.
"We've never had this happen with IDS cameras," Blank confirmed.
The fifth USB uEye supplies color images of the top of the wood piece, which will later form the visible parquet surface and must therefore be flawless. The trouble is determining what is a flaw, and what's just a variation of the wood grain? Blank's answer almost sounded like a lesson in botany: "It really is a science. Different criteria apply for different wood types. Indeed, about two thirds of all natural wood parquet flooring is made of oak, but about 20 other tree types are also available."
Each tree type is checked using its own unique program. The customer can teach-in new types themselves if they have enough time and experience. Blank suggests that at least five thousand pieces of wood be used to teach-in a wood type.
While the user ranks each piece of wood in categories such as "exquisite", "natural" and "rustic", the system learns to differentiate between pieces on its own.The detection of so-called sapwood is especially challenging. These parts are too soft for parquet flooring and are characterized by discoloration in the wood blocks.
In addition to checking the color of the entire piece of wood, the ATB Blank system evaluates other criteria, such as the distribution and variation of color and the local arrangement of discoloration. Depending on the structure of discoloration, it can be reliably determined whether or not the wood is sapwood. For such evaluations, it is critical that the camera be able to reproduce colors consistently and true-to-life.
IDS attaches great importance to high quality during the development process, both with regard to the housing and the software. Every CCD camera produced undergoes adapted sensor calibration, where various parameters are adjusted for optimum image reproduction. The camera driver includes a color correction matrix for all models that is determined with color tables under defined conditions. This makes true-to-life image capture by the cameras possible.
Blank is also satisfied with the business relationship above and beyond the technical aspects. "Cooperation with IDS has always gone very well. Contact is direct, delivery times are quick and they are very flexible."