By Owais AliReviewed by Lexie CornerApr 3 2024
As modern infrastructure continues to expand and evolve, structural health monitoring (SHM) has become crucial for ensuring safety, identifying structural damage, and establishing early warning systems. However, traditional resistive strain gauge systems lack the stability, durability, and measurement range required for these intelligent systems.
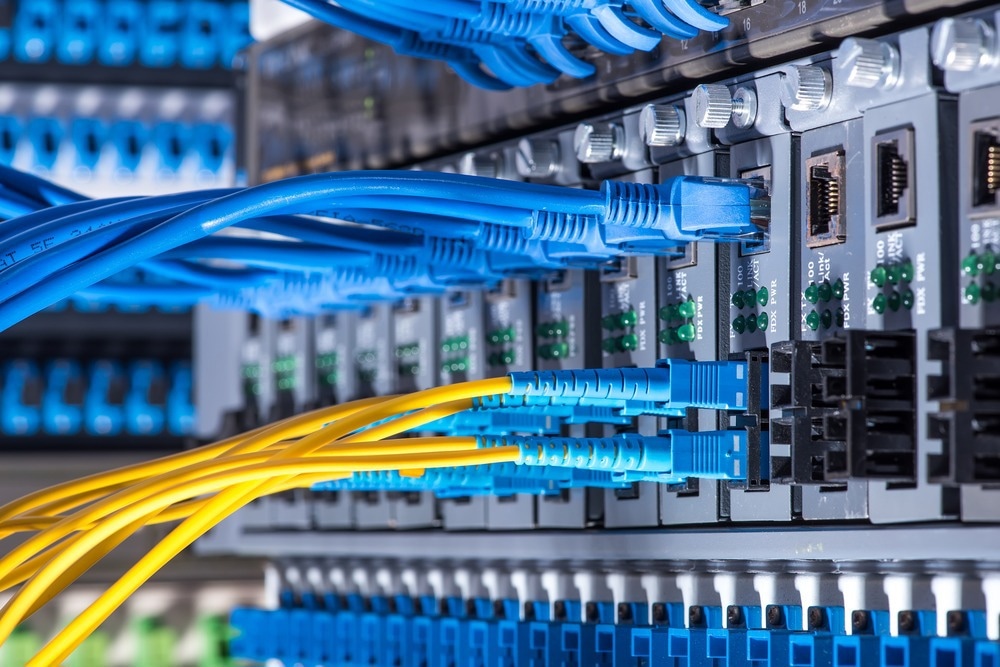
Image Credit: asharkyu/Shutterstock.com
Fiber optic sensors (FOS) have emerged as a promising alternative, offering advantages such as compact size, corrosion resistance, and easy embedding, facilitating the rapid development and widespread adoption of SHM.
The Principles of Fiber Optic Sensing
Optical fiber sensing techniques leverage the interaction between light and the fiber's properties, enabling highly accurate and reliable measurements of various physical parameters. This principle is manifested through several types of fiber optic sensors, each leveraging unique mechanisms to detect and quantify changes in strain, temperature, vibration, and other critical indicators of structural health.
Fiber Bragg gratings (FBGs), for instance, rely on periodic variations in the refractive index of the fiber core, acting as highly reflective mirrors at specific wavelengths. Any deformation or temperature change alters the spacing of these gratings, resulting in a measurable shift in the reflected wavelength. This provides a highly sensitive and localized means of monitoring strain and temperature.
Complementing FBGs are distributed fiber optic sensors (DFOS), which utilize techniques like Brillouin scattering and optical time domain reflectometry (OTDR). These sensors capture strain and temperature profiles along the entire length of the fiber, enabling continuous monitoring over vast distances with unparalleled spatial resolution. This makes them invaluable for large-scale infrastructures.1
Key Benefits of Fiber Optic Sensors
Compared to traditional sensing technologies, fiber optic sensors provide numerous advantages, including a compact size, immunity to electromagnetic interference, and the ability to withstand harsh environments.
Their multiplexing capabilities facilitate the integration of numerous sensing points along a single fiber, significantly reducing installation costs and complexity.2
Technological Innovations in Fiber Optic Sensing
Continuous advancements in technology further enhance the capabilities of fiber optic sensing solutions. Recent innovations have focused on miniaturization, improved sensitivity, and novel sensor designs.
Advancements in Miniaturization
Researchers at the University of Southampton developed a compact, cost-effective FBG interrogator using flat optical fiber and machine learning algorithms.3 This innovation reduces the interrogator's size and cost (approximately 25 USD/meter for fiber), making FBG monitoring more accessible and practical for real-world applications.4
Enhanced Sensitivity
The integration of exceptional point (EP) dynamics has significantly amplified sensor sensitivity, enabling the detection of minute signals with unprecedented accuracy.
A study published in Opto-Electronic Advances implemented EP dynamics in a fiber-optic bending sensor, achieving exceptional sensitivity with a gauge factor of 1.32 GHz/m-1 over a curvature range of 0.28 to 2.74 m-1, and an accuracy of 7.56 × 10-4 m-1. This breakthrough could enable the early detection of structural anomalies and improve the safety margins of critical infrastructures.5
The Integration of Nanomaterials
The integration of micro/nanofibers (MNFs) has opened up new avenues for highly sensitive and fast-response strain sensors.
Another Opto-Electronic Advances study designed an optical strain sensor with evanescently coupled MNFs in a polydimethylsiloxane (PDMS) film, achieving a gauge factor of 64.5 for strains up to 0.5 % and a strain resolution of 0.0012 %.
Its fast temporal frequency response up to 30 kHz enables sound detection, while its pressure sensitivity of 102 kPa-1 enables real-time micro-displacement detection for structural health monitoring.6
Applications in Structural Health Monitoring
The versatility and robustness of fiber optic sensors have enabled their widespread adoption in SHM across various infrastructures.
Bridge Monitoring
Fiber optic sensors are pivotal in bridge monitoring, detecting minute elastic strains and deflections under static traffic loads and offering invaluable insights into the behavior of aging concrete structures.
A team of European researchers employed DFOS to investigate the impact of static traffic loads on the slight deflection of Amsterdam Bridge 705. By integrating FOS within the bridge, they successfully identified a small elastic strain ranging approximately 2 μm/m, achieving a remarkable spatial resolution of 20 cm. This underscores the exceptional sensitivity of these sensors.7
Sewerage Tunnel Maintenance
In sewerage tunnel maintenance, predicting and preventing damage is crucial to avoid flooding, landslides, and environmental contamination. Traditional remote inspection methods are limited by their periodic nature and the need for tunnel cleaning, prompting the exploration of fiber optic sensors for real-time structural health monitoring.
In a study published in Procedia Technology, researchers installed a fiber optic SHM system within a sewerage tunnel renewal project in Meiningen, Germany. The system, equipped with fiber optic humidity and tilt sensors, was placed at pipe interfaces to detect tunnel misalignments and water outlets.
The post-installation measurements (Sensor 1 recorded 35.73 % relative humidity and 10.56 °C, Sensor 2 recorded 45.01 % relative humidity and 9.36 °C) demonstrated the system's effective operation, paving the way for ongoing long-term monitoring.2
Challenges and Solutions
While fiber optic sensing technology has made significant advancements, several challenges remain to be addressed.
Data Management
One of the primary hurdles is managing the vast amounts of data generated by these sensors, particularly in the case of distributed fiber optic systems. For example, a distributed acoustic sensor (DAS) system covering a 2 km sensing range, sampling at 2000 Hz with 1 m spatial resolution, generates approximately 650 GB of daily data.
Researchers are actively exploring efficient data compression algorithms and leveraging big data analytics to process and extract valuable insights from these data streams.
Cross-Sensitivity
The cross-sensitivity of quasi-distributed FBGs and DFOS systems to various physical parameters poses a challenge. This necessitates the development of advanced machine-learning techniques for multiparameter sensing and discrimination.
Practical issues such as fiber strain, fragility, temperature cross-sensitivity, and the materials surrounding the optical fibers must also be addressed to ensure seamless integration with civil structures.8
The Future of Fiber Optic Sensing
The future of fiber optic sensing in structural health monitoring promises transformative advancements, such as AI-driven anomaly detection, miniaturized self-powered sensors, and autonomous monitoring systems.
These advancements will revolutionize civil infrastructure engineering and maintenance, optimizing operations, enhancing resilience, improving public safety, and enabling smarter urban planning.8
However, collaborative efforts among researchers, industry leaders, and infrastructure stakeholders are essential to navigate challenges and unlock this revolutionary technology's full potential.
More from AZoOptics: From Diagnosis to Precision Treatment: Exploring the Role of Optics in Ophthalmic Surgery
References and Further Reading
- Khonina, S. N., Kazanskiy, N. L., & Butt, M. A. (2023). Optical Fibre-Based Sensors—An Assessment of Current Innovations. Biosensors. doi.org/10.3390/bios13090835
- Bremer, K., Wollweber, M., Weigand, F., Rahlves, M., Kuhne, M., Helbig, R., Roth, B. (2016). Fibre optic sensors for the structural health monitoring of building structures. Procedia Technology. doi.org/10.1016/j.protcy.2016.08.065
- Falak, P., et al. (2023). Compact high-resolution FBG strain interrogator based on laser-written 3D scattering structure in flat optical fiber. Scientific Reports. doi.org/10.1038/s41598-023-35708-1
- Grace Nehls. (2023). University of Southampton develops miniaturized optical fiber condition monitoring technology. [Online] CompositesWorld. Available at: https://www.compositesworld.com/news/university-of-southampton-develops-miniaturized-optical-fiber-condition-monitoring-technology
- Li, Z., Chen, J., Li, L., Zhang, J., Yao, J. (2023). Exceptional-point-enhanced sensing in an all-fiber bending sensor. Opto-Electronic Advances. doi.org/10.29026/oea.2023.230019
- Yu, W., Yao, N., Pan, J., Fang, W., Li, X., Tong, L., Zhang, L. (2022). Highly sensitive and fast response strain sensor based on evanescently coupled micro/nanofibers. Opto-Electronic Advances. doi.org/10.29026/oea.2022.210101
- Wosniok, A., Jansen, R., Toet, P., Doppenberg, E., De Jong, W., Chruscicki, S. (2020). Static load monitoring of a concrete bridge using a high-precision distributed fiber optic sensor system. e-Journal of Nondestructive Testing. https://www.ndt.net/?id=24957
- Venketeswaran, A., et al. (2022). Recent advances in machine learning for fiber optic sensor applications. Advanced Intelligent Systems. doi.org/10.1002/aisy.202100067
Disclaimer: The views expressed here are those of the author expressed in their private capacity and do not necessarily represent the views of AZoM.com Limited T/A AZoNetwork the owner and operator of this website. This disclaimer forms part of the Terms and conditions of use of this website.