Digital technological advancements have made laser additive manufacturing (LAM) a revolutionary technique for industrial production.
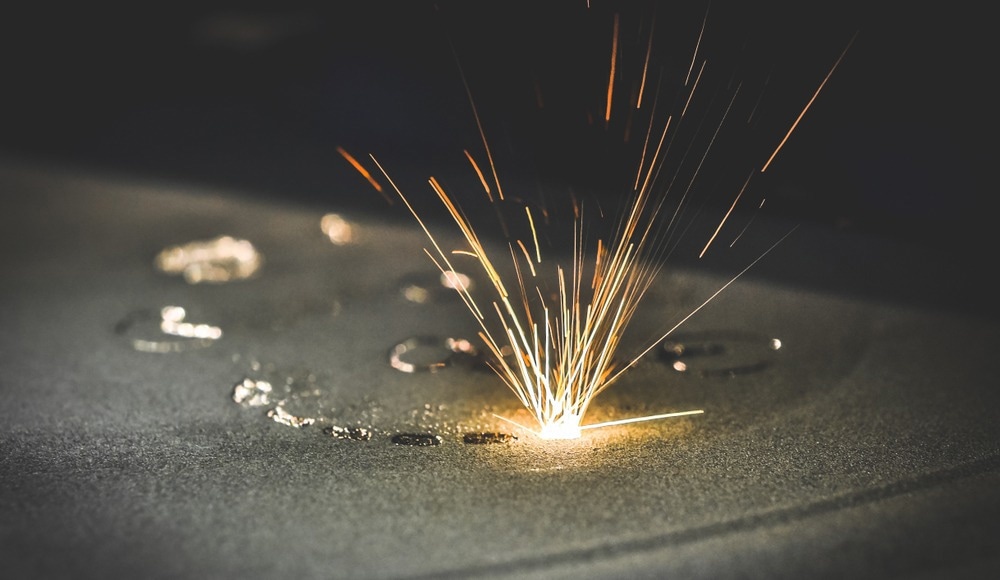
Image Credit: MarinaGrigorivna/Shutterstock.com
Also referred to as 3D printing, LAM is the process of building an object by layering materials precisely to the shapes delineated by a digital design. The layers can be in the form of liquid, metal, cement or powdered plastic. Each layer is fused to form a 3D object.
Laser Additive Manufacturing Processes
LAM employs laser technology to harden the material in a powder bed by melting it.
Rapid growth in laser innovations has enabled new possibilities in LAM-based product design and creation.
Processes for laser additive manufacturing fall into three categories. These are:
- Selective Laser Sintering (SLS)
- Stereolithography (SLA)
- Selective Laser Melting (SLM).
High-powered CO2 lasers are used in the SLS method of additive manufacturing to fuse or bind finely powdered materials into solid objects. In this procedure, a printer applies an even layer of powder before carefully sintering that layer. This process is repeated until the desired item is produced.
One of the most widely used processes in additive manufacturing is SLA, also known as SLA 3D printing. It functions by employing a high-energy UV laser to build the desired 3D shape by hardening liquid resin that is kept in a reservoir. This technique turns photosensitive liquid into 3D solid plastics.
SLM uses fiber lasers to construct the 3D structure. The product is created by selectively melting a series of powder layers with the help of the laser beam. When exposed to radiation, the powder material heats up and melts and forms a liquid pool if enough power is used. Once the molten pool is cooled and solidified, the final structure begins to take shape.
Laser Scanners for Laser Additive Manufacturing
A laser beam scanner is used to steer the laser beam quickly across the target areas according to the blueprint specified by the 3D model.
Each of the three LAM processes described above uses laser scanners. The laser scanner must accommodate different laser powers and beam sizes depending on system requirements. The complexity of the laser scanning system and its integration is determined by the physical size of the finished item, build rate, and minimum feature size.
To coordinate the laser beam scanner’s motion with the laser trigger, software commands translate the design protocol into a sequence of control commands to move the laser.
The choice of scanner and controller essential for laser beam steering directly impacts the structural construction performances. For instance, the geometric precision of a part is determined by how precisely the scanner directs the laser beam to the build plane's intended point.
The laser beam delivered to the sample has to be uniform with minimal power fluctuations. This ensures that the final product is homogeneously composed in its interior and is of high quality.
Applications of Laser Additive Manufacturing
LAM has successfully transformed many industries. For example, over three decades, 3D implant structures and prototype parts have been created using SLA. The creation of individualized implants has benefited from using clearly designed 3D models.
Prototyping components produced by the SLS technique are employed frequently in the design of transport, combat, electronic and electrical systems. The SLS process can quickly produce more significant 3D parts, which is an attractive prospect for commercial enterprises.
SLM has grown in popularity in recent years since it can produce complex geometries and lightweight structures. These properties make SLM adaptable and economical. The medical, automotive and aerospace industries have significantly benefited from SLM technology.
Current Innovations and Future Outlooks of Laser Additive Manufacturing
The components and materials used in LAM continuously evolve through advanced research efforts.
Many academic and industrial organizations are pursuing innovative technological innovations to improve LAM. For example, a government-funded project in Germany is developing dental implants using titanium.
High strength and resistance to corrosion are two characteristics of titanium alloy. Because of its exceptional biocompatibility, titanium has been used in numerous medical applications, including orthopedic surgery and prosthetics.
The new LAM-based dental implant development is expected to offer a comfortable fit for the wearer and long-term functionality.
Another innovative application of LAM is in the space industry. Since 2014, private businesses such as SpaceX have used LAM to produce parts for their rockets. Many robotic vehicle components used to examine the surfaces of planets are also built using LAM.
Many initiatives are being taken to employ LAM in microgravity environments in space. Several research teams are also looking into the prospect of printing living structures on the Moon using LAM technology. These initiatives seek to create large-scale LAM construction methods to build dwellings on the moon's surface using loose rock, dirt, and lunar regolith.
Exciting new developments in LAM are transforming industrial production. Many unique geometries with unprecedented features can push the boundaries of scientific exploration.
References and Further Reading
Optics.org. (2022) LZH develops customized dental implants in a new DFG research group. [Online] Optics.org. Available at: https://optics.org/news/13/8/20
AZoOptics.com. (2019) Advancing Alloys to Suit Laser Additive Manufacturing. [Online] AZoOptics.com. Available at: https://www.azooptics.com/Article.aspx?ArticleID=1764
Sivarajah, I. (2022) Applications of 3D Printing in Space. [Online] AZoQuantum.com. Available at: https://www.azoquantum.com/Article.aspx?ArticleID=345
Disclaimer: The views expressed here are those of the author expressed in their private capacity and do not necessarily represent the views of AZoM.com Limited T/A AZoNetwork the owner and operator of this website. This disclaimer forms part of the Terms and conditions of use of this website.