Australian laser heat treating technology pioneer, LaserBond, has just announced a $1 million technology sale to Curtin University, Western Australia. Curtin University will use LaserBond’s innovative laser metal deposition (LMD) system to advance materials development with its capacity for cutting-edge 3D metal printing, laser additive manufacturing, laser welding, and other laser cladding solutions.
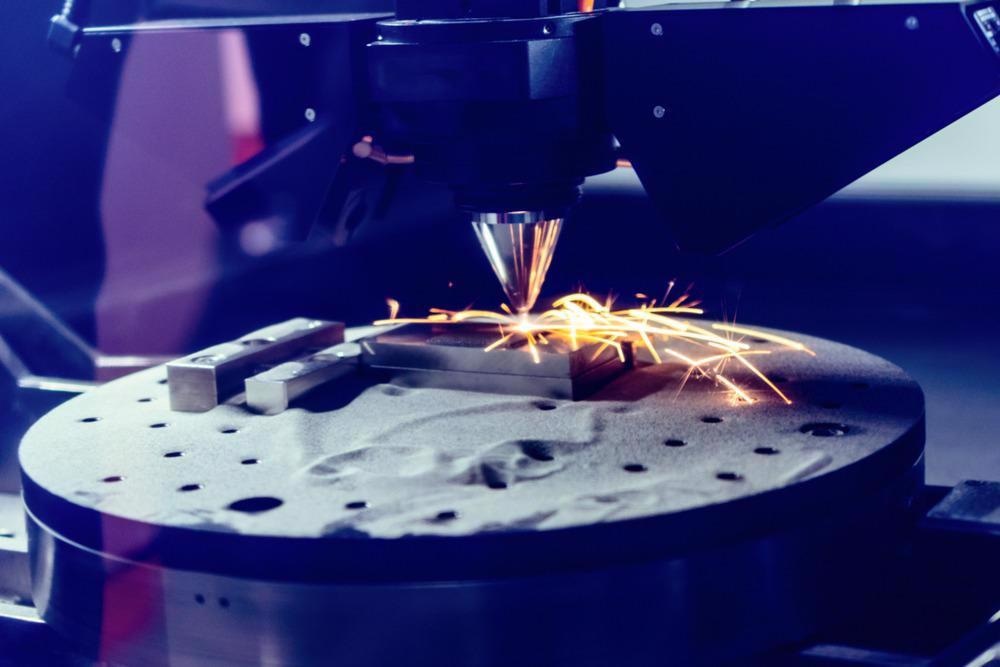
Image Credit: Nordroden/Shutterstock.com
Sale Reinforces LaserBond’s Position at Cutting-Edge of Materials Development
LaserBond is a specialist surface engineering company with offices in Sydney, Adelaide, and Victoria, Australia. The company’s deal with Curtin University is the next step in an ongoing partnership.
According to LaserBond, the LMD system that they will manufacture and install will help Curtin University with:
- Research
- Training
- Demonstration
- Micro-scale manufacturing
The system is capable of fabricating and processing metal products using:
- 3D metal printing
- Laser additive manufacturing
- Laser cladding
- Laser welding
- Laser heat treating
With its investment, Curtin University will advance materials development and next-generation manufacturing techniques for metal parts and products.
This latest $1 million deal is part of an ongoing partnership between LaserBond and Curtin University. The University is supporting LaserBond’s research and development, looking to develop materials and applications for laser heat treating technology.
The partners will also develop a demonstration facility to showcase the technology to industry partners in Western Australia. The largest university in Western Australia, Curtin University also has a focus on industry partnerships, especially in the energy and resource sectors.
What is LMD?
LMD, also called laser cladding, is a laser additive manufacturing technique used to bond surfacing materials to almost any metallic substrate. A high-powered laser is precisely controlled and focussed on the surfacing material, creating a metallurgical bond between surfacing material and substrate.
This process creates high-performing surfaces and can be applied to new and old parts for an extended operating life. Extremely durable surfaces are created by the metallurgical bond fashioned in the LMD process. High bond strength is achieved with rapid coating solidification, and the fine microstructures this results in on the newly surfaced material.
There are minimal effects from excess heat with this process, both on the substrate and surfacing materials. This makes LMD suitable for a wider range of applications than traditional welding methods.
Another advantage over traditional welding is that LMD can be used to bond surfacing materials to almost any metallic substrate. Cobalt alloys, nickel alloys, copper alloys, stainless steel, steel, and cast iron are all suitable substrate materials for this technique.
What are the Benefits of LMD?
Limited Coating Dilution
Surfacing materials need minimal dilution to be applied using the LMD technique. Laser cladding therefore results in much better purity and overall performance.
Precision
As a laser additive manufacturing process, LMD is CAD-driven and robot-operated. This means that deposit layers are precisely clad and fully fused, with no defects.
High-Performance Materials
This precision and purity lead to better overall performance for materials that have undergone laser cladding.
Cost-Effective
LMD is a good way to maximize the operational lifespan of expensive, heavy-duty machinery and equipment, reducing the costs of repairs and new equipment.
Reclaim Worn Components
LMD can be used to restore components that were previously considered too fatigued for further use. This reduces the need for more manufacture, saving money, resources, and energy in the process.
Works with Sensitive Components
LMD is a highly precise laser additive manufacturing technique. This makes it suitable for work on sensitive components, or components that need to satisfy tight engineering tolerances.
Better than Conventional Arc Welding
Compared to traditional arc welding or plasma transferred arc (PTA) welding, LMD has several benefits:
- Shorter processing times
- Localized heat input, minimal excess heat, and smaller distortion and heat-affected zones
- Less dilution of coating materials (under 5%)
- Can clad smaller and thinner pieces
Laser Additive Manufacturing
LMD is a laser additive manufacturing technique that progresses the wider field of additive manufacturing as well as offering new opportunities for advancing materials development.
LMD builds up multiple layers of surfacing material with extremely high bond strengths, as is the case in other metallurgical bond techniques such as traditional arc welding. However, it can be applied with much more precision, as well as computer-aided efficiencies.
With LMD, manufacturers can apply an engineered surface only to the specific areas of the component that will need it. Coupled with modern CAD software, manufacturing processes can be streamlined and made as efficient as possible, eliminating wasted time and resources.
As an additive manufacturing technique, LMD is also very flexible. This offers greater design freedom for engineers who are not limited by the shapes and sizes of existing machinery and manufacturing equipment. Complex geometry and forged casting can be accurately surfaced with the LMD technique.
Like other 3D metal-printed parts and components, equipment made using LMD can be rapidly prototyped and iterated through different designs. Unlike with conventional manufacturing, changes to design do not entail any expensive refitting of manufacturing facilities, just a different set of instructions to the computer system.
What is Next for Laser Heat Treating Technology?
As demonstrated by its ongoing partnership with Curtin University, LaserBond is committed to innovation projects, advancing materials development. The company’s research is focused on three project areas:
- Tribology
- Materials science
- Applications for additive manufacturing
LaserBond’s LMD laser heat treating technology is a forerunner in an emerging field of laser-aided manufacturing. Laser additive manufacturing and other advanced manufacturing techniques have the potential to revolutionize the world of physical products.
References and Further Reading
Dinda, G. P., A. K. Dasgupta, and J. Mazumder (2009). Laser Aided Direct Metal Deposition of Inconel 625 Superalloy: Microstructural Evolution and Thermal Stability. Materials Science and Engineering: A. https://doi.org/10.1016/j.msea.2009.01.009
LaserBond Announces $1m Technology Sale Agreement with Curtin University. (2021) Australian Manufacturing. [Online] Available at: https://www.australianmanufacturing.com.au/143106/laserbond-announces-1m-technology-sale-agreement-with-curtin-university
LaserBond. [Online] Available at: https://laserbond.com.au/
Disclaimer: The views expressed here are those of the author expressed in their private capacity and do not necessarily represent the views of AZoM.com Limited T/A AZoNetwork the owner and operator of this website. This disclaimer forms part of the Terms and conditions of use of this website.