Oct 28 2014
An insight on the positioning mechanisms and limitations is critical to achieve precision from the positioning devices. This article describes about the motion control technology employed in Zaber's positioning devices, quantification of inaccuracies and strategies to reduce the effects.
Zaber’s computer-controlled positioning devices feature stepper motors to obtain open loop position control, and are controlled by a constant angle called a step for every electrical signal transmitted. This enables designing a system without requiring a feedback for accurate positioning. The motor can also be rotated by microstepping.
However, there are certain limitations in using open-loop position control systems. If the torque becomes higher than maximum, a stall condition will occur, and the rotation of the motor stops. Figure 1 shows some of the critical characteristics of the stepper motors and mechanics employed in Zaber’s devices.
.jpg)
Figure 1. Motor and lead screw properties of Zaber devices
Resolution
The resolution, also known as microstep size or addressability is defined as the smallest incremental distance moved by the device or the rotational/linear displacement which corresponds to a single microstep of movement.
Certain models have different types of lead screw pitches. The resolution of T-LSMXXXA models is 0.047625µm while the T-LSMXXXB model has a resolution of 0.1905µm. Finer pitch versions in the same model can generate greater thrust, while the models with coarser pitch screws can attain a maximum speed.
Sticktion
Because of friction, the device may not move at all when requested to move by one microstep. After a certain number of requests to move one microstep, the motor’s torque will exceed the static friction, resulting in the motor jumping by the accumulated number of microsteps, and then it will stick again. This phenomenon is called sticktion, which is very much dependent on the load and amount of wear on the lead screw.
Friction can prevent the device from moving one microstep. At a certain point, however, the motor may tend to jump a number of microsteps and stick again due to higher torque than the static friction. This process is known as sticktion which is based on the amount and load of wear on the lead screw.
Most of the positioning devices undergo this problem to a certain extent. However, following the backlash, some devices with a small load will move on each microstep. The accuracy of microstep position is +/-0.1µm. A test is carried out with a small load of 5N and repeated with a 20N load. Figure 2 shows the testing of same device with different loads.
.jpg)
Figure 2. Graph showing the measured vs requested position of same device with different loads
Repeatability
The repeatability is defined as the maximum deviation of the device’s position while trying to return to a position from a different position. Figure 3 shows the determination of repeatability of a T-LA28A actuator moved 1mm from a given position to the same position. The number of times the actuator stops can be observed in the histogram.
The two peaks correspond to the direction of approach, and a Gaussian distribution having a full width at 1/e2 of about 0.3µm is present within each peak. This shows the typical repeatability for Zaber's T-LA actuators. The backlash between the two peaks is 2.2µm.
.jpg)
Figure 3. Graph showing the number of trials vs final position of the T-LA actuators.
Backlash
Backlash is the deviation of the final position of the device resulting from the reversal of direction of approach. The backlash is complex for small movements that involve a change of direction. The determination of the actual position of the device depends not only on the requested position, but also on the exact trajectory.
A test is carried out with a T-LA28A actuator that is made to stop at 5µm, move back to 0µm and forward to 1.5µm. Figure 4 shows the graph of the actual position measured and plotted as a function of the requested position.
.jpg)
Figure 4. Backlash hysteresis graph showing the measured vs requested position of T-LA28A actuator
Anti-sticktion and Anti-backlash Features
Sticktion and backlash are the key factors that affect the movement of device by small amounts. In order to overcome these limitations, Zaber T-Series devices are designed with built-in anti-backlash and anti-sticktion routines which do not affect the motion.
The anti-backlash mode increases the absolute position without affecting the motion in the positive direction. However, with negative motion, the desired position was overshot by 600 microsteps. Following this, the device will return to the requested position from below.
Accuracy
The accuracy is defined as the maximum deviation of the device from its actual position to the requested position over the full range of motion. Figures 5 and 6 show the determination of accuracy in T-LA28A actuator. In a typical lead screw system, a cyclic error of +/-3 µm peak deviation with a one period motor rotation is desirable.
The poor resolution of the gauge results in the big jumps. Addition of cyclic error improves the actual accuracy of the device. This increases the maximum deviation to 5.5µm maximum deviation from 0 error. Hence, the accuracy of the tested actuator is +/-5.5.
.jpg)
.jpg)
Figure 5 and 6. Graphs showing the determination of accuracy in T-LA28A actuator
Stability
A stability of the positioning device is defined as its ability to remain in a position for a long time period. The main factors affecting the stability of the device are internal and external temperature changes which produce thermal expansion and generate payload motion.
Figure 7 shows a time constant of about 20 to 30 minutes and a maximum amplitude of 37µm. Due to creep of the bearing holding the rotor or lead screw in the rotor thread, the position of the device does not return to zero after cooling. The temperature rise of the motor is 75°C.
It is necessary to consider temperature effects while involving high duty cycles or larger movements. Upon repeating the same readings during an experiment and observing constant increasing or decreasing trend in readings, thermal effects can be considered.
.jpg)
Figure 7. Position vs time graph of T-LA28A electronics
Conclusion
A clear understanding of the effects and methods of various positioning mechanisms described above enables a user to employ low-cost, simple devices with wide range of applications. In addition, knowing the limitations of the device further helps in scrutinizing the performance of the device.
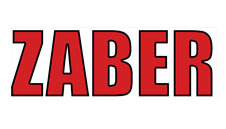
This information has been sourced, reviewed and adapted from materials provided by Zaber Technologies Inc.
For more information on this source, please visit Zaber Technologies Inc.