Gas analysis is a critical technique used to identify and control contamination in the production process of optoelectronics, avoiding defects in the devices, financial loss, and reducing safety risks. This article explores the importance of contamination control in optoelectronics manufacturing, gas analysis techniques, applications, and recent advancements.
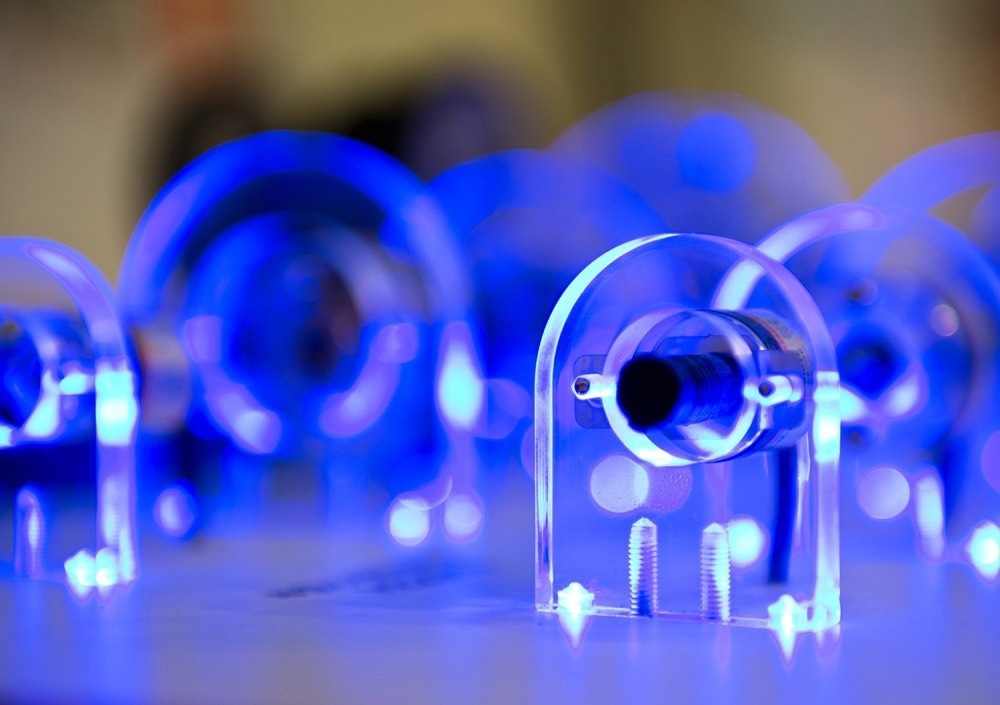
Image Credit: hxdbzxy/Shutterstock.com
Optoelectronics is a crucial sector of the electronics industry that produces devices for converting electrical signals into light and vice versa, which are used in various modern-day technologies. However, the manufacturing process of optoelectronics requires a controlled environment to avoid contamination that can affect the devices' performance and reliability.
As such, contamination control is a significant challenge in optoelectronics manufacturing. In this light, gas analysis offers a reliable method to detect and control contamination in real-time.
Importance of Contamination Control in Optoelectronics Manufacturing
Contamination control is a critical aspect of optoelectronics manufacturing, as even small particles can cause significant damage to the delicate electronic components involved. Contaminants can affect the performance of the devices, shorten their lifespan, and even render them completely useless.
The importance of contamination control extends beyond the manufacturing process itself. Optoelectronic devices are used in a variety of applications, including medical, military, and communication systems. Ensuring the reliability and performance of these devices is crucial for their successful use in these applications.
Gas Analysis Techniques Used For Contamination Control in Optoelectronics Manufacturing
Two of the most commonly used gas analysis techniques are gas chromatography-mass spectrometry (GC-MS), and Fourier transform infrared spectroscopy (FTIR). GC-MS separates and identifies individual gas components, while FTIR measures the absorption and transmission of infrared light by a gas sample.
GC-MS offers high sensitivity and specificity, making it ideal for trace-level analysis of complex mixtures. It can also detect a wide range of gas molecules, from volatile organic compounds (VOCs) to inorganic gases like nitrogen and oxygen. However, GC-MS requires a skilled operator and a longer analysis time.
FTIR, on the other hand, provides fast and non-destructive analysis, making it ideal for real-time monitoring of gas concentrations. It also has a lower cost and simpler operation than GC-MS. However, FTIR is less sensitive than GC-MS and cannot identify individual gas components in mixtures.
Both techniques have applications in optoelectronics manufacturing. For example, GC-MS can be used to detect impurities in gas delivery systems and gas storage tanks, while FTIR can be used for real-time monitoring of gas concentrations in manufacturing environments.
Photoacoustic Spectroscopy (PAS) and Ion Mobility Spectrometry (IMS) can also be used to monitor contamination in optoelectronics manufacturing.
PAS is a sensitive technique for detecting and quantifying trace amounts of gases in a sample. It works by measuring the acoustic signal generated when a sample absorbs light. PAS is particularly useful for detecting gases that absorb in the infrared region of the spectrum, such as CO and CO2, which are common contaminants in optoelectronics manufacturing.
IMS is a fast and sensitive technique for detecting trace amounts of volatile compounds. It works by ionizing the gas molecules and then measuring their drift time through an electric field. IMS is particularly useful for detecting volatile organic compounds (VOCs), which can be emitted from adhesives, solvents, and other materials used in optoelectronics manufacturing.
Gas Analysis Applications in Optoelectronics Manufacturing
Gas analysis plays a critical role in contamination control in optoelectronics manufacturing. By analyzing gases emitted during the manufacturing process, scientists can identify potential sources of contamination and take proactive steps to prevent it. This approach can help ensure the quality and reliability of the final product.
Gas analysis can also be used to identify sources of contamination. For example, during the manufacturing process, unwanted gases may be introduced due to faulty equipment or poor handling practices. By analyzing the gases emitted from the production line, scientists can identify the source of the contamination and take corrective action.
In addition, gas analysis is an essential tool for quality control. By analyzing the gases emitted during manufacturing, scientists can ensure that the production process is consistent and that the final product meets specific quality standards. This helps to ensure that the product is reliable and meets customer expectations.
Advancements in Gas Analysis for Contamination Control In Optoelectronics
New gas analysis technology advancements, such as laser-based techniques and real-time monitoring systems, are revolutionizing contamination control in optoelectronics manufacturing. These advancements offer high sensitivity and selectivity, allowing for the detection of trace amounts of contaminants and providing continuous monitoring of the manufacturing environment.
The implications are significant, improving product quality, reducing waste, increasing efficiency, and having broader societal impacts. Future advancements are expected to improve sensitivity, selectivity, and speed, further enhancing the quality and reliability of optoelectronic devices.
Conclusion
Contamination control is a critical aspect of optoelectronics manufacturing, as even small particles can cause significant damage to the delicate electronic components involved. Gas analysis offers an effective solution to this challenge by providing a reliable method to detect and control contamination in real time.
The latest advancements in gas analysis technology have revolutionized the way contamination is detected and controlled in optoelectronics manufacturing. These advancements have significant implications for the industry and broader society, enabling manufacturers to improve product quality, reduce waste, and increase efficiency.
Considering the potential for further improvements in sensitivity, selectivity, and speed, gas analysis technology will continue to enhance the quality and reliability of these critical devices.
More from AZoOptics: A Guide to Laser Beam Shaping Techniques
References and Further Reading
Dodds, J.N., Baker, E.S. (2019). Ion Mobility Spectrometry: Fundamental Concepts, Instrumentation, Applications, and the Road Ahead. Journal of the American Society for Mass Spectrometry 30, 2185–2195. https://doi.org/10.1007/s13361-019-02288-2
IEEE. (2010). Contamination and ESD Control in High-Technology Manufacturing. [online] Available at: https://ieeexplore.ieee.org/book/5201423/ [Accessed 10 Apr. 2023].
Kwaśny, M., Bombalska, A. (2023). Optical Methods of Methane Detection. Sensors 23, 2834. https://doi.org/10.3390/s23052834
PDA. (2022). Contamination Control Strategies: A Path for Quality & Safety. [online] Available at: https://www.pda.org/pda-letter-portal/home/full-article/contamination-control-strategies-a-path-for-quality-safety [Accessed 10 Apr. 2023].
Laser Focus World. (2016). Contamination Control: Improve yield and quality by monitoring particle contamination during optics manufacturing. [online] Available at: https://www.laserfocusworld.com/software-accessories/positioning-support-accessories/article/16546976/contamination-control-improve-yield-and-quality-by-monitoring-particle-contamination-during-optics-manufacturing [Accessed 10 Apr. 2023].
Bose P. (2021). The Different Types of Gas Analysis Techniques. [online] AZoM.com. Url: https://www.azom.com/article.aspx?ArticleID=20277 [Accessed 10 Apr. 2023].
Disclaimer: The views expressed here are those of the author expressed in their private capacity and do not necessarily represent the views of AZoM.com Limited T/A AZoNetwork the owner and operator of this website. This disclaimer forms part of the Terms and conditions of use of this website.