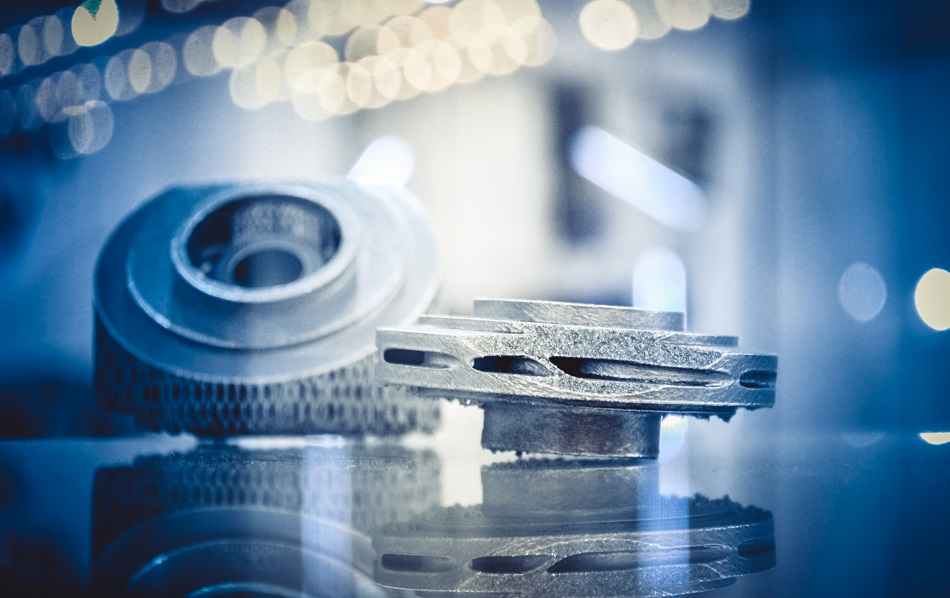
Image Credit: MarinaGrigorivna/Shutterstock.com
From its limited beginnings in the mid-nineteen eighties, 3D printing or additive manufacturing has found applications across numerous industries and business sectors, from a tool for rapid prototyping to a technology that can print buildings on-site in hours rather than days, it has become increasingly useful as the materials it can work with are becoming more varied. Originally producing objects in a narrow range of resins or plastics, it can now print in a variety of useful, production quality materials from glass to concrete. Its ability to produce 3D printed parts in metal is revolutionizing the way things are made.
As with several areas of 3D printing, some terms are often used interchangeably or mean roughly the same thing. Currently, there are two methods used to produce 3D printed objects in metal. The first is referred to as Selective Laser Sintering (SLS) and sometimes as Direct Metal Laser Sintering (DMLS). The second is Selective Laser Melting (SLM) or sometimes you will see Direct Metal Laser Melting (DMLM). The difference between the two is straightforward and is related to the temperature to which the printed material is heated. Selective laser sintering heats the material, a finely powdered metal, to the point where the particles, typically between 20 and 40 micrometers, are welded or fused. As its name suggests, Selective Laser Melting heats the material to the point where it becomes molten, producing metal parts that can be treated in the same way as conventionally produced items. Both systems produce parts that can be machined, heat-treated or given various surface finishes.
Both methods were invented at the roughly same time and developed in parallel. SLS first appearing in the nineties, as described in a patent, now expired, by Carl Deckhard. The technology was brought to market in 1995 by EOS who developed the first commercial DMLS printers. SLM technology was developed at the Fraunhofer Institute for Laser Technology in Aachen, Germany. It was not without legal and licensing issues since the technologies only differ in the temperature that is achieved by the laser, so EOS still retains a commercial interest in SLM through their licensing arrangements.
In each case, the process follows the usual route of a 3D printed part, first model, then slice and print layer by layer. The procedure in each case comprises a powder delivery system, a scanner, a laser, and a fabrication bed or piston. A thin layer of build powder is dispensed onto the bed, it is then sintered or melted. The bed descends to allow a coater blade to lay another thin slice of powder onto the previous layer, the laser targets and the object is built. So, while the pathway of the two processes is identical, the finished product is significantly different as the SLS part will have a degree of porosity and although strong, will not exhibit the same strength as the SLM part. An SLM object also needs supports to be incorporated into the design because unlike SLS, the molten metal can’t be supported by the surrounding powder. This together with a rough surface finish means that an SLM part might need significant post-print finishing. SLM requires that the metals it can print with have certain flow characteristics when molten, so is currently limited to working with titanium, aluminum, cobalt, chrome, tool steel, and stainless steel.
However, despite these current constraints SLM has many advantages and the materials it can work with make it especially useful in certain industries.
NASA has been interested in using SLM parts because they see a real advantage in being able to produce pieces of equipment as a whole, rather than having to produce and assemble individual parts. The 3D printed an injector for a rocket engine in 2013 that was made up of only two parts as against the one hundred and fifteen parts in the previous conventionally produced injector. It was a complete success. Not to be outdone, in 2014 Space X launched its Falcon rocket that utilized a 3D printed a valve body. Compared with the cast part, the SLM produced valve was stronger, with a better fracture resistance and less variability in the properties of the material. Rigorous testing of the part has qualified the printed Main Oxidizer Valve to be used interchangeably with cast parts in the rocket assembly. They also successfully developed a 3D printed engine chamber to be used in their SuperDraco engines.
Because it successfully prints in chrome and titanium, it is also ideal for producing high-value medical devices and implants.
Currently, SLM is an expensive route to manufacture but in certain high value projects its advantages make it a valuable option. Currently, it’s not exactly a desktop device, but with over 40 manufacturers currently offering metal printing solutions, it is set to become increasingly available as an everyday production tool.
Sources and Further Reading
Disclaimer: The views expressed here are those of the author expressed in their private capacity and do not necessarily represent the views of AZoM.com Limited T/A AZoNetwork the owner and operator of this website. This disclaimer forms part of the Terms and conditions of use of this website.