Users can be faced with an uncertainty regarding the performance of their beam profilers and whether these profilers are measuring precisely. There is no standard calibration methodology where users can validate their camera-based beam profiling measurement precision. Spiricon’s camera-based profilers have been developed to provide reliable results, increasing customer’s confidence.
The existing problem can be divided into two major areas: the input (camera) and the output (from software algorithms). The input (camera) has two parts; the physical imager and the electronic processing and A/D conversion accuracy.
Camera - The Physical Imager
Digital cameras come with an array of a fixed number of pixels in the X and Y direction. Accurate semiconductor photolithography processes are used to make these pixels, and the precision of the pixel pitch is maintained in the angstroms range (1 x 10-10 m). This extent of pixel-to-pixel distance difference is not a key factor and the accuracy of the resulting beam profiling measurement is not adversely affected.
Conversely, all imagers are not equally produced and some are more suitable for operating at specific wavelengths and under varied conditions when compared to others. Here, an imager can offer worse or better precision depending on the way it is utilized.
Electronic Processing and A/D Conversion Accuracy
Areas like signal to noise, gain, linearity, and black level, including the A/D conversion into several bits that represent the intensity of light from individual pixels, are covered by electronic processing and A/D conversion. In the past, a camera featuring an 8 bit converter was considered to be a high end product, but today most of the cameras include 12 or 14 bit converters, producing 4096 or 16,384 independent levels of intensity.
In the case of a current camera optimized to regulate all the above variables, most will produce signal to noise ratios from 58 to 63 dB rms. However, using 60 dB for a standard 12 bit camera will yield approximately 24 counts of peak-to-peak noise out of 4096. Cameras with higher signal to noise ratios, which can effectively digitize into the noise, are known to exhibit better capability when making precise quantitative measurements.
In order to validate the effect of signal to noise error on precision, Spiricon's BeamMaker® mathematical laser beam/camera simulator can be used. Integrated with BeamGage, the BeamMaker is a mathematical beam modeling tool that is capable of producing an ideal synthetic laser beam through TEM mode values.
It is possible to superimpose camera signal to noise on the beam and precision can be checked at different bits per pixel levels. By utilizing the generated image as input and replicating a 12 bit camera, BeamGage can compare the resulting measurement precision against the input model of known value. This article also verifies the software algorithms that are elucidated in the following section.
It is important to ensure that the output is precise and repeatable. Irrespective of the quality of a camera, the precision of results will eventually depend on the way the camera's image data is processed as well as on the integrity of the computational algorithms used on the data. These algorithms are split into two key topics: image processing and data computations.
Image Processing
Spiricon know that appropriate image processing with respect to establishing a zero baseline is critical for making suitable laser beam measurements. The company’s patented Ultracal baseline correction algorithm was used nine years in advance of ISO proposing the protocol in ISO 11146-3:2004. Measurements of second moment beam width are no more than good approximations, unless the computational algorithms are preceded by accurate image processing.
Data Computations
Two separate algorithm verification techniques are used by BeamGage - the latest beam profiling software from Spiricon. Each algorithm was separately compared to a MATLAB® simulation of the same input data, and the algorithms used by the MATLAB designer were written, independent of the BeamGage programmer, so that the process is not cross contaminated.
This approach proved that the results generated by BeamGage and those produced by MATLAB® were exactly the same. Further validation was made by utilizing the BeamMaker utility within the BeamGage software. A mathematically perfect laser beam, produced by BeamMaker, can be applied as an input data for BeamGage measurements.
Next, measurements obtained from the BeamGage software were subsequently compared to the known modeled input parameters and these were validated to be the same. Both of these techniques showed that computational algorithms and BeamGage image processing are reporting repeatable and precise results. Spiricon's regression test suite is integrated with these two test systems, which were validated on each software release.
So What Kind of Accuracy Can One Expect From a Spiricon Laser Beam Analyzer?
Unlike a caliper or power meter that can be subjected to some type of industry standard, no industry standard laser is available as a reference. It is not easy to control, quantify, simulate, and standardize lasers.
Spiricon's BeamMaker was specifically developed to address this. Although the BeamMaker system was developed years ago, its integration in the latest BeamGage product is what holds the present interest. This was mainly done to help users, so that they gain confidence about their results based on different conditions.
The following is a set of problems, and each requires its own discussion on its effects on precision:
- Camera gain setting as it impacts s/n ratio
- Camera/Laser drift with temperature
- Camera blooming or smearing effects based on beam brightness, wavelength and exposure settings.
- Proper use of baseline correction
- Beam is ≤ ½ the imager size in each direction.
- Laser beam second moment width is ≥ to 10 pixels
- Laser noise and other time varying properties such as shot to shot variability of pulsed lasers or pointing stability of CW lasers
- Beam amplitude variability over the cameras dynamic range
- Beam attenuation and external beam handling distortion effects
- Where in the beam propagation path one performs the measurement, or am I measuring the right thing in the right place
- Knowledge of the user to understand what is being measured and what choice of methodology is being employed
- Proper use of aperturing to improve accuracy
- Proper trigger mode selection and exposure timing when capturing pulsed lasers
- Camera damage, especially due to over exposure and extended UV exposure
- Failure to employ a Manual or an Auto Aperture
Considering that most of the above applicable items have been taken into account by users, a good effort has been made to reduce external sources of errors, and users can present their beam to the camera with good signal versus the camera dynamic range. The following factors can be expected in this regard:
- Power tracking across the range from 5 to 98% of dynamic range, +/- 5%.
- Second moment beam width precision using Auto-Aperture and Ultracal, +/-2%, all modes and mode – When Auto- Xposure is used, the above applicable items is reduced to roughly +/- 5%. However, this results in less favorable beam presentation conditions, like reduced beam intensity or size.
- Centroid precision about 1/10th pixel pitch, modified for scaling factors.
- Precision of other beam measurement techniques - Knife-Edge second moment equivalent techniques will create similar precisions for TEMoo beams; however, these tend to exhibit erratic systemic errors as the beam mode mix modifies.
- 90/10 approach is somewhat more precise when compared to the ISO technique.
- % of Power/Energy and % of Peak are less sensitive to noise, but lack industry traceable outcomes for beams except for circular TEMoo diameters. Except in terms of a user defined context, mixed mode results are not quite meaningful. The same rule applies to encircled power smallest slit and encircled power smallest aperture.
- When measured using second moment beam widths, divergence measurements relate only to beam propagation theory. In other user-defined results and techniques, users have to validate for their own purposes.
What Else Can Be Done to Maintain Confidence in Beam Analysis Systems?
As cameras are designed to give an optimum performance for imaging laser beams, the 'window' is taken off from the front of the sensor array. Consequently, the unguarded array becomes a target in a laser beam shooting gallery, and is vulnerable to abuse, damage, and deterioration.
The imaging array and subsequent images, exposed to the effects of local environment and generated from the array, may deteriorate based on the elements. These would be minor degradation, such as increased appearance of poor pixels; however, in extreme cases fractures and corrosion can lead to considerable deterioration or catastrophic failure.
Conclusion
In order to maintain the performance of a camera, Spiricon proposes that customers return their camera on a customary basis for a validation and recertification process. Such measures will help to rectify bad pixels whenever possible, cleaning the imager, and certifying that the camera is still operating to factory specifications. Alternatively, customers will be advised of any changes that require replacement, repair, or limited usage.
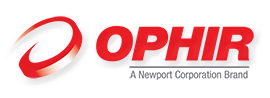
This information has been sourced, reviewed and adapted from materials provided by Ophir Optronics Group.
For more information on this source, please visit Ophir Optronics Group.