In a study published in Sensors, researchers developed a Brillouin scattering-based spiral deployment arrangement of distributed fiber optic sensors to assess and monitor the cable forces in concrete during tensioning processes. On-time condition assessments and monitoring of these cables provides critical data for effective decision-making, ensuring post-tensioned concrete structures’ structural safety.
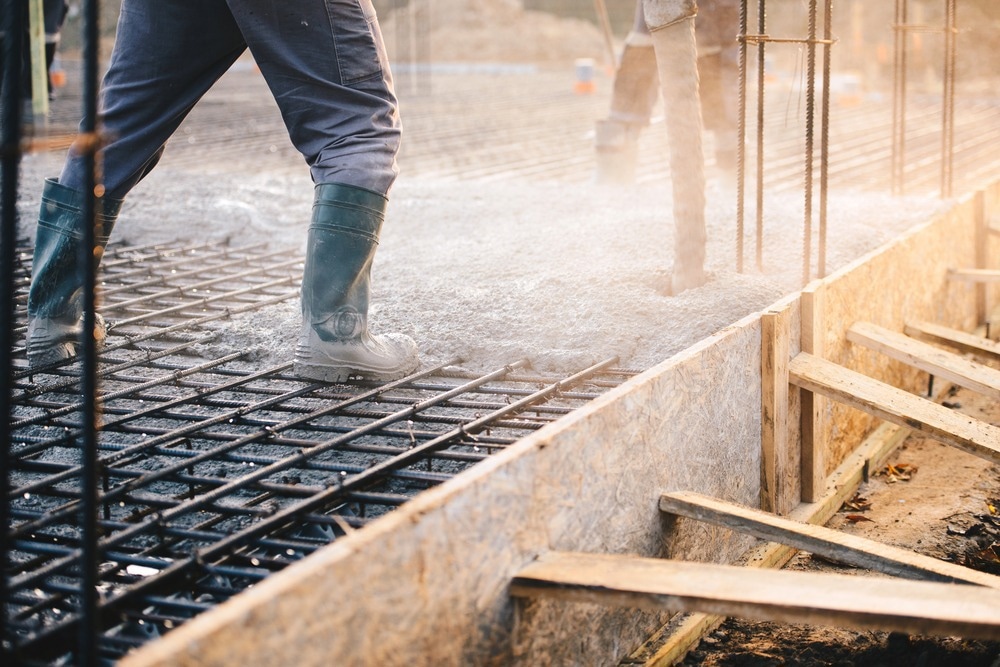
Study: Spiral Deployment of Optical Fiber Sensors for Distributed Strain Measurement in Seven-Wire Twisted Steel Cables, Post-Tensioned against Precast Concrete Bars. Image Credit: bubutu/Shutterstock.com
Impact of Cable Forces on Structural Safety and Performance
Steel cables are widely utilized in prestressed concrete structures and bridges, where their vast cross-sectional areas are exposed to high tension levels. The cable’s rupture results in the gradual collapse of the structures and disastrous consequences.
The prestressing force and long-term and short-term prestress losses influence the load-bearing capacity, deflection, cracking resistance, and longevity of prestressed concrete structures. Therefore, a system’s structural integrity and operational efficacy are closely related to the state of the cables employed in its construction and operation.
Limitations of Current Cable Force Measuring Methods
Monitoring and evaluating the sustainability of cable-based constructions can be aided by measuring the cable force. Direct strain measurement, low-cost vibration frequency, oil pressure meter, high-precision laboratory magnetic flux sensors, and acoustic emission technology are just a few methods to detect cable forces.
However, while these techniques have been widely successful in measuring cable forces in engineering constructions, they also have significant drawbacks. For example, indirect vibration-based measurements are slow and have low accuracy; magnetic flux sensors are susceptible to interference from electromagnetic fields; strain gauge sensors must be compensated for temperature, and their reliability is a concern, particularly in harsh environments.
In addition, many strain sensors are required to detect forces along the cables, which increases the complexity and expense of the project. Furthermore, the large number of wires required to link these sensors makes them difficult to work with, degrading structural performance and complicating construction and maintenance.
Therefore, improved techniques for measuring cable forces are needed for real-time monitoring in the field.
Advantages of Fiber Optic Sensors in Cable Force Measurements
Fiber optic sensors have recently become increasingly popular for measuring cable stresses. Fiber optic sensors have a minimal impact on the performance of cables during installation due to their lightweight and compact size. Their resilience to electromagnetic interference enhances the robustness and dependability of measurements.
In addition, complete distributed strain measurements throughout the optical fiber have been achieved using Brillouin and Rayleigh scatterings. This helps identify local interactions induced by frictional contact between the duct and the cable and local slippage along the cable buried in the concrete due to unequal strain distributions.
Cable forces have been measured using distributed sensing systems based on Brillouin scattering. However, the application of distributed fiber optic sensors (DFOSs) to directly detect cable forces based on the Brillouin optical time domain analysis is still inaccurate and incomplete.
Using Brillouin Scattering-Based DFOSs to Measure the Cable Force in Concrete Bars
Each distributed fiber optic sensor was spirally inserted between two steel cable surface wires and secured to the cable using epoxy. Image observations examined the comprehensiveness and bonding quality of the optical fiber and steel wires.
Eight concrete bar specimens were created with a metal duct or pre-embedded plastic in the center. After installing two temperature and two strain sensors, they were post-tensioned by a steel strand via the duct.
The strand was loaded and unloaded, and the Brillouin frequency changes were measured and correlated with the applied stresses and the resultant cable force. The maximum, average, and minimum cable forces evaluated from stain data were compared and verified against those from a load cell.
The efficiency of the proposed cable force measurement was verified by comparing the recorded distributed fiber optic sensors’ data to the load cell readings.
Important Findings of the Study
All distributed fiber optic sensors survived the tensioning and force release processes, and strain distribution along the strand was derived using the strain–frequency coefficient.
After removing any initial slack in the test setup, there was a linear relationship between the maximum cable force and the ground truth data with an error of less than 10%. Using the designed test configuration, the post-tensioned force loss was confined by approximately 30 %.
The epoxy type may have greatly influenced the recorded cable forces, necessitating more research. The epoxy construction process may have caused optical fiber location uncertainty and void flaws in the vicinity of the setup.
Possible solutions to the void defect include using a small epoxy coating as a cushion layer in the valley before placing the optical fiber. The top layer might then be covered with a second coat of epoxy. However, the robot-assisted autonomous building would be preferable to eliminate optical fiber location uncertainty in the future.
Reference
Zhu, Y., & Chen, G. (2022) Spiral Deployment of Optical Fiber Sensors for Distributed Strain Measurement in Seven-Wire Twisted Steel Cables, Post-Tensioned against Precast Concrete Bars. Sensors. https://www.mdpi.com/1424-8220/22/19/7636
Disclaimer: The views expressed here are those of the author expressed in their private capacity and do not necessarily represent the views of AZoM.com Limited T/A AZoNetwork the owner and operator of this website. This disclaimer forms part of the Terms and conditions of use of this website.