Specular surfaces are notoriously difficult to measure, but a new method combines deflectometry and polarization techniques to capture their 3D shapes with precision, enabling advances in industry and cultural preservation.
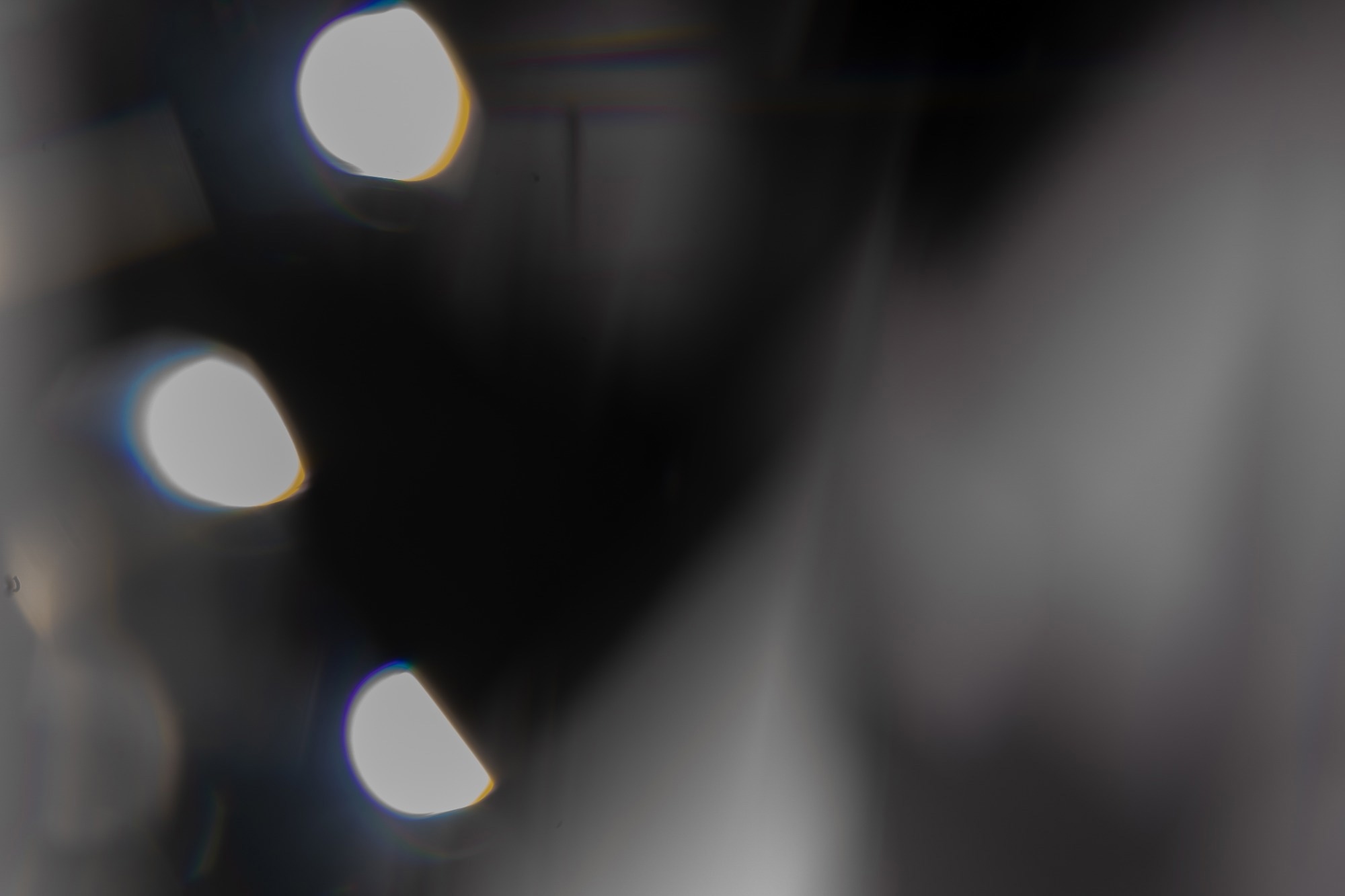
Image Credit: photo-lime/Shutterstock.com
Most tools have little trouble analyzing matte or diffuse surfaces, as they scatter light in many directions. But specular, mirror-like surfaces behave differently. They reflect light in a single, sharp direction.1
This creates significant challenges for 3D imaging and surface inspection, which rely on light bouncing around a bit before reaching the camera. With the sharp, directed light reflected off specular surfaces, light does not become more diffuse before reaching the imaging system detectors, and they cannot reconstruct surface geometry.
However, recent developments, particularly the fusion of Phase Measuring Deflectometry (PMD) with Shape from Polarization (SfP), are beginning to change that.1-3
These limitations make quality control and process automation in industrial applications difficult. They're even more of a problem in fields like cultural heritage preservation, where non-contact, non-destructive methods are essential, preventing scientists from being able to accurately image shiny artifacts.3
PMD and SfP: Strengths and Limitations
PMD works by projecting a structured light pattern onto a screen and observing its distorted reflection on a shiny surface. From that, it can be inferred the surface’s geometry. It’s accurate, relatively straightforward, and works well at sub-micron levels. However, it cannot reliably determine a point's distance from the sensor. This ambiguity, known as the height-normal problem, has long limited PMD's usefulness.4
SfP is a slightly different approach. It looks at how light becomes polarized when it reflects, then uses this data to estimate the orientation of the surface. While promising, SfP suffers from multiple ambiguities in determining surface normals, particularly when applied to specular materials. Standard SfP methods often rely on simplified models of how light behaves, leading to inaccuracies when those models don’t match the real world.5-6
What if you combined the two to overcome their separate shortcomings?
A Breakthrough: Fusing PMD and SfP
That’s exactly what researchers led by J. Wang at Northwestern University have done. Their new hybrid system merges PMD and SfP into a single method that resolves the limitations of both.
Their hybrid system uses the geometric strengths of PMD with the polarization-based orientation cues from SfP to resolve ambiguities in normal estimation of height and surface surface. The two datasets disambiguate each other, producing a much more accurate 3D map.7
What sets this method apart is that it doesn't require any prior assumptions about the object's shape or light conditions. By capturing polarization information and structured reflections in a single or multi-shot setup, the system calculates the degree of polarization and combines it with known geometric constraints to compute the exact surface point and normal.
This approach allows it to disambiguate multiple candidate normals and calculate depth simultaneously, all with impressive precision. It also avoids relying on the simplified “orthographic” model of light projection, which assumes all rays are parallel. That’s rarely the case in real-life setups using standard perspective cameras.7
The team tested their system using both simple and complex reflective objects. A precision-engineered bearing ball came back with a mean angular error in surface normals of just 0.56 °, and a depth error of 70µm. More complex objects, such as small chrome animal figurines, also fared well, showing that the system can handle real-world variation in shape and material. 7
Toward Real-Time, Mobile, and Adaptive Inspection
The success of this PMD-SfP fusion method points toward a future where high-precision reflective surface inspection could be integrated into mobile or real-time platforms. The need for fixed alignment between the display, object, and camera often constrains traditional PMD setups.
The new system offers greater flexibility by reducing reliance on multiple viewpoints or prior assumptions, making it suitable for hand-held devices or robotic inspection arms.
Integrating machine learning models to further improve the PMD-SfP system may also be possible. For instance, training models on various material properties or reflection profiles could allow the system to compensate for real-world inconsistencies like material heterogeneity or environmental lighting changes.
The Broader Trend: Optical Metrology Meets Computer Vision
This fusion of PMD and SfP is part of a broader trend in imaging: merging physical measurement with computational interpretation. The line between sensing and analysis is becoming increasingly blurred. Where older systems simply captured data, newer ones interpret it in real time, turning raw light into meaningful 3D models with minimal guesswork.
So, the PMD-SfP system is not just measuring light; it's decoding a complex interaction between light and matter in real time.
These advances in imaging could open doors across sectors. Medical imaging could enable non-invasive inspection of specular anatomical structures, while in cultural heritage, fragile shiny artifacts can be captured with unprecedented detail.
Challenges and Considerations
Despite its promise, the PMD-SfP fusion method does face practical challenges. Accurate knowledge of the refractive index of the surface material is vital for computing the correct polarization-derived angles.
While the system is tolerant to small mismatches, variations across a surface can introduce errors. Polarization cameras typically have a lower signal-to-noise ratio, which can require longer exposure times or higher-intensity light sources.
Another consideration is the system's angular coverage. Because it relies on active illumination, typically from a screen, it can only measure parts of a surface that reflect that light back toward the camera. If the angle between the object and the screen is too steep, the light won’t return to the sensor, and those regions are invisible to the system.
Despite this, the fusion of PMD and SfP marks a turning point in specular surface imaging.
As the technology matures, its potential only grows. From real-time quality control in manufacturing to the detailed documentation of cultural artefacts, these tools promise to bring precise, real-time measurement of reflective surfaces into mainstream applications.
References and Further Studies
- Shimizu, Y. et.al., An Insight into Optical Metrology in Manufacturing. Measurement Science and Technology 2021, 32, 042003.
- Marrugo, A. G.; Gao, F.; Zhang, S., State-of-the-Art Active Optical Techniques for Three-Dimensional Surface Metrology: A Review. Journal of the Optical Society of America A 2020, 37, B60-B77. https://opg.optica.org/josaa/fulltext.cfm?uri=josaa-37-9-B60&id=434236
- Catalucci, S.; Thompson, A.; Piano, S.; Branson III, D. T.; Leach, R., Optical Metrology for Digital Manufacturing: A Review. The International Journal of Advanced Manufacturing Technology 2022, 120, 4271-4290. https://link.springer.com/article/10.1007/s00170-022-09084-5
- Zhang, Z. et. al., Phase Measuring Deflectometry for Obtaining 3d Shape of Specular Surface: A Review of the State-of-the-Art. Optical Engineering 2021, 60, 020903-020903. DOI: 10.1117/1.OE.60.2.020903
- Baek, S.-H.; Heide, F. In All-Photon Polarimetric Time-of-Flight Imaging, Proceedings of the IEEE/CVF Conference on Computer Vision and Pattern Recognition, 2022; pp 17876-17885. https://collaborate.princeton.edu/en/publications/all-photon-polarimetric-time-of-flight-imaging
- Kadambi, A.; Taamazyan, V.; Shi, B.; Raskar, R. In Polarized 3d: High-Quality Depth Sensing with Polarization Cues, Proceedings of the IEEE international conference on computer vision, 2015; pp 3370-3378. DOI:10.1109/ICCV.2015.385
- Wang, J.; Cossairt, O.; Willomitzer, F., 3d Imaging of Complex Specular Surfaces by Fusing Polarimetric and Deflectometric Information. Optica 2025, 12, 446-450. https://opg.optica.org/optica/fulltext.cfm?uri=optica-12-4-446&id=569660
Disclaimer: The views expressed here are those of the author expressed in their private capacity and do not necessarily represent the views of AZoM.com Limited T/A AZoNetwork the owner and operator of this website. This disclaimer forms part of the Terms and conditions of use of this website.