Dec 16 2019
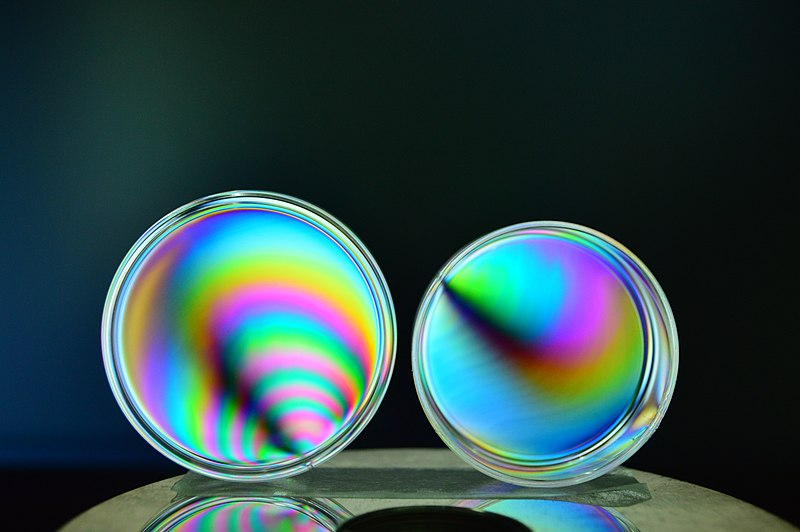
Wikimedia Commons
The ability to detect minor surface defects is essential to many manufacturing industries, and several manufacturers are now using polarized structured light (PSL) to detect crucial minor defects.
PSL is a non-destructive, non-contact technique that makes it possible to conduct quick, three-dimensional inspections of surfaces to identify corrosion, scuff marks, and other flaws with micrometer precision and high repeatability.
Modern handheld instruments founded on PSL technology provide performance and dependability, in addition to high-end assessment capabilities. These qualities make handheld PSL devices an attractive means of assessing machined high-precision surfaces.
Inspectors in high-precision manufacturing industries must be able to precisely figure out the severity of any surface defects; to determine if a product is enough, needs treatment or ought to be scrapped. A tiny pit or scratch may be enough to trigger part failure, especially in high-speed or high-pressure situations. Being able to quantify surface features and defects helps ensure function and durability.
In many cases, inspectors depend on visual evaluations to assess material surfaces. One problem with this approach is that a high degree of effectiveness requires significant experience on the part of the inspector. The other problem is that is the process is fairly time-consuming.
Numerous systems are capable of gauging surface roughness, but many are costly, slow, and prone to defect-causing vibration, like those found on a production floor. These other instruments are normally designed for use in highly controlled laboratory environments, making it very challenging to evaluate large components or hard-to-reach components. It is possible to create synthetic replicas of surfaces for testing, but this a method can take a relatively long amount of time and is subject to issues in the replication process.
Combining Two Techniques
The PSL technique merges two techniques: fringe projection and dynamic interferometry. Also referred to as “structured light”, fringe projection is a technique founded the projection of a known light pattern onto a test surface, which is then reflected at another angle onto a receiver. Any distortions in the known pattern observed in the projected pattern can be used to digitally model the test surface in three dimensions. The main problem with fringe projection is that numerous readings are needed to generate a useful outcome. Also, the time to data acquisition is quite long, and minor vibrations can seriously affect test outcomes.
Dynamic interferometry makes use of polarization to encode a light beam, and a special detector to decode the projected signal. Data to be used for 3D reconstruction of a test sample can be gained in microseconds, making it possible for a handheld instrument to generate precise measurements in busy surroundings. However, dynamic interferometry has typically been used to gauge extremely smooth surfaces with sub-nanometre precision, not larger micrometer-scale features.
PSL fuses the two procedures in a high-speed method with a large range for gauging vertical features: .005mm to 2.5mm. Its resistance to vibration enables the use of handheld PSL testing devices. The sub-micrometer resolution of these devices is adequate for quantifying defects caused by common machining processes, corrosion and standard wear. These devices are capable of a measurement cycle that lasts just a few seconds.
Uses
Quick, convenient, high-resolution surface assessment is crucial to ensuring the performance and safety of machined parts, and for cutting down on needless scrapping and refinishing of parts. By allowing production floor measurement, a PSL device offers a cost-effective option for fast, precise, traceable assessment of surfaces.
A typical PSL device can inspect extremely smooth and intricate surfaces alike. This process can also be used to evaluate surfaces with varying reflectivity and smoothness. In addition to quantifying defects, a PSL gage can also gauge desired surface features, like laser etching and paint thickness. A PSL device can assess several defects concurrently, like numerous tiny pits caused by corrosion, and quantify each pit individually.
Sources: