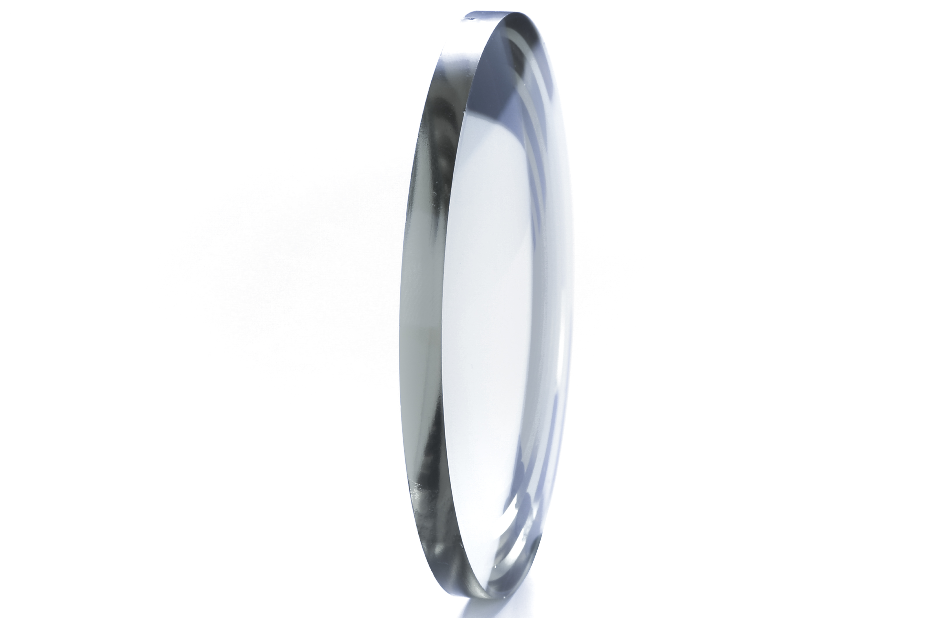
xiaorui / Shutterstock
Offering superior performance and operational flexibility, freeform optics are the next generation in modern optics.
Historically, symmetric optical surfaces were used to maintain a beam of focused light, ideally with minimal aberrations. Having had a minimum of one freeform surface without translational or rotational symmetry about axes normal to the mean plane, freeform optics are lighter, smaller, and more effective than conventional optics. Traditional optics also had the benefit of simplistic design and manufacturing, but advances over the past two decades, including high-speed micro milling and computer-aided lens polishing processes, have made creating freeform optical surfaces more viable.
Freeform optics are currently being used in many different fields, including in energy and aerospace.
Designing Freeform Optics
A major problem with freeform optics is design, specifically figuring out which surfaces work most effectively in a specific arrangement of mirrors and lenses. This aspect of freeform optics design has been time-consuming and costly, typically involving a lot of trial and error.
Although current optical design technology is effective enough to create intricate optical systems, there is still a robust need for new design processes to establish primary configurations of freeform optics.
In a 2018 paper published by the journal Nature, scientists described a step-by-step technique that eliminates a great deal of trial and error from the design process of freeform optics. The technique described in the paper starts by delving into the primary positioning of mirrors and lenses, and then, pertinent to an assessment of the various aberrations generated by that alignment, the technique predicts if and how freeform surfaces could reduce those disruptions. The researchers said their technique allows designers to investigate countless potential geometries.
Manufacturing Freeform Optics
For freeform optics to realize its full potential, manufacturing must keep up with design technology. Standard manufacturing operations like grinding and ultraprecision turning only have two degrees of freedom, insufficient for creating freeform surfaces. Fabrication operations with more degrees of freedom, like coordinated axis diamond turning and deterministic micro-grinding, are necessary to produce the surfaces needed for freeform optics. One major drawback of additional degrees of freedom is greater positioning uncertainty, which makes it more difficult to meet requirements for form and surface roughness.
There are substantial difficulties regarding the measurement of freeform surfaces, as existing metrology platforms also have challenges concerning precision.
Measuring Freeform Optics
As the design and manufacturing tactics for freeform optics get better, so must the measurement capacity to evaluate them.
The specifications for the measurement of freeform optics can vary significantly. Some of the fundamental demands for freeform measurement include the capability to gauge surface irregularity, location on a surface, and mid-spatial frequency flaws. Also, based on the freeform optics' surface-tolerance specifications, a high degree of accuracy may be necessary.
A popular tool for assessing freeform optics is called a coordinate measurement machine (CMM). This device has a probe tip and a scanning head that is used to gauge a surface relative to the ideal features, or fiducials. Fiducials are critical for defining freeform optics as conventional optical parameters, like center thickness, are problematic for optics with little or no symmetry. Fiducials are typically used in a coordinate system that can be assessed by the CMM and supply data surrounding locations and orientations of the surface.
Fringe reflection, also called deflectometry, is a process to gauge the various slopes of an optical surface. In this process, a camera captures images of light reflections coming off the test surface to map the various surface slopes. The surface form can then be visualized by integrating the slopes.
Every measuring tool for measuring freeform optics has its advantages and drawbacks, which are based on certain applications. As the design and fabrication of freeform optics carry on evolving, so do the tools used to measure them.
Sources:
Disclaimer: The views expressed here are those of the author expressed in their private capacity and do not necessarily represent the views of AZoM.com Limited T/A AZoNetwork the owner and operator of this website. This disclaimer forms part of the Terms and conditions of use of this website.