Surface quality specifications refer to the type of imperfections and the number of perfections allowed on all of the coated and uncoated surfaces of an optical component. While some of these surface imperfections are purely cosmetic, many of these imperfections can introduce undesired scattering or even make the optical filter more vulnerable to damage caused by the laser, which can lead to the performance of the system suffering as a result.
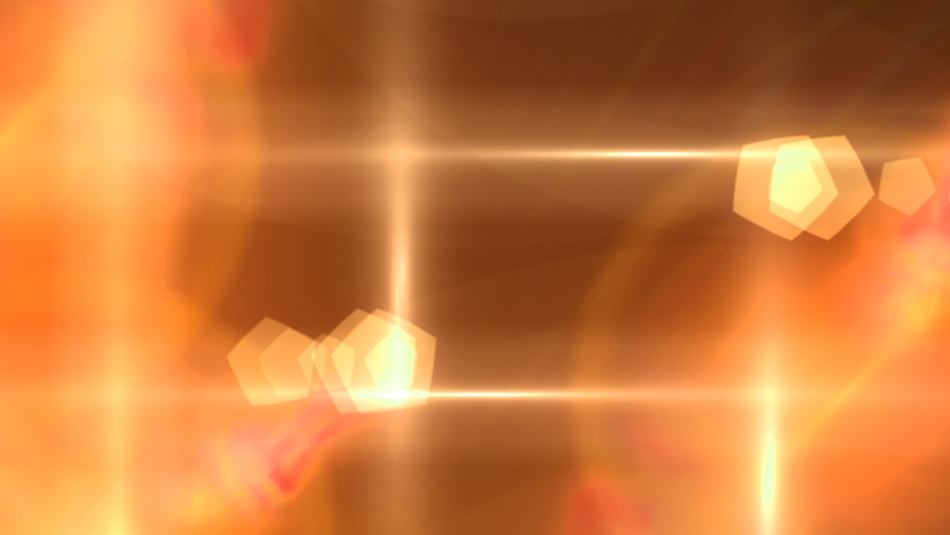
Image Credit: Shutterstock/emu_melo
Surface quality specifications are typically defined according to standards set by the United States Military, the American National Standards Institute (ANSI), or the International Organization for Standardization (ISO). The definitions, methods of evaluation, and the time needed for evaluations can differ between these standards.
MIL-PRF-13830B
Most military and ANSI standards define the scratch-dig surface quality specifications as a series of numbers that are linked to the size of the scratch or dig itself. With MIL-PRF-13830B, evaluation is carried out with visual comparisons between the imperfections, using an optical filter and a reference part with specific lighting conditions outlined in the document.
The dig value roughly matches the diameter of the imperfection. However, the scratch value only refers to the apparent width of the scratch when it is compared to the standard. For example, a scratch-dig specification of 60-40 is commonly used. This means there cannot be any scratches that appear wider than the ‘60’ comparison standard, and no digs can be of a diameter larger than 0.4 mm.
When all of the scratches and digs found on an optical filter have been classified, the MIL-PRF-13830B document lays out additional requirements concerning scratches and digs that are found to adhere to the maximum allowable category that has been defined by the specification.
These requirements are as follows:
- The sum of the length of maximum size scratches has to be less than one quarter of the diameter of the part
- When a maximum size scratch is found, the ratio of the scratch length to the part diameter is multiplied by the corresponding category number for each scratch. The sum must also be less than half of the maximum category number, or less than the maximum category number if no maximum size scratches are present.
- The number of maximum size digs has to be less than the part diameter divided by 20
- The sum of the diameters of all of the digs must be less than twice the product of the number of maximum size digs, multiplied by the maximum dig category number.
Recommended specifications vary by application and system requirements, but overall, a sufficient scratch-dig specification is defined as 80-50 for filters operating at low to moderate performances. High-performance filters are typically specified as 60-40 or better. Filters used in laser applications often require a specification of 40-20 or better.
ANSI/OEOSC OP1.002-2009
ANSI/OEOSC OP1.002-2009 was produced to be a more universal alternative to the military standards set out in the MIL-PRF-13830B. The ANSI/OEOSC OP1.002-2009 also offers the option of calling out specifications with two alternatives: the visibility method and the dimensional method.
The visibility method is almost identical to the methods detailed in MIL-PRF-13830B, but it is clearer about test procedures. The dimensional method gives a particular specification letter to each scratch width and dig size category. These letter categories correspond to those outlined in MIL-C-48497A, but ANSI/OEOSC OP1.002-2009 furthers these categories by including the option to call out the specifications according to maximum values other than those included in the pre-defined categories. Overall, it is the visibility method that is used far more widely than the dimensional method.
ISO 10110-7
ISO 10110-7 sets out surface quality specifications that are purely quantitative, in contrast to the standards set out in MIL and ANSI. The ISO standard does not make distinctions between scratches and digs, and instead classifies them more generally as surface imperfections.
These surface imperfections are specified according to the total number allowed and the maximum grade number, which is equal to the square root of the measured area of the surface imperfection, and measured in millimeters. The ISO does give the option to use the prefixes C, L, and E to call out imperfections in the coating, long scratches (>2 mm), and edge chips respectively.
It is important to note that surface quality specifications can have a substantial effect on costs. Although it is essential to choose surface quality specifications according to the requirements set out by the particular system, over-specifying can cause decreased yield and increased financial outgoings. Similarly, opting for a labor-intensive surface quality standard can also increase the overall cost.
Alluxa’s Custom Thin-Film Optical Filters
Alluxa’s team of experts has delivered key innovations to the field of optical thin-films. Along with designing and constructing all of their own custom optical thin-film coating equipment, Alluxa invented a new plasma deposition coating process that both improved the performance of their optical filters and decreased production times.
By taking these innovations and pairing them with state-of-the-art automation, proprietary control algorithms, and precision monitoring during the coating process, Alluxa can produce affordable, high-performance, custom thin-film optical filters fit for all applications.

This information has been sourced, reviewed and adapted from materials provided by Alluxa.
For more information on this source, please visit Alluxa.