Scramjets (supersonic combustion ramjets) are a high-speed propulsion technology, possibly enabling strong performance benefits compared to rockets.
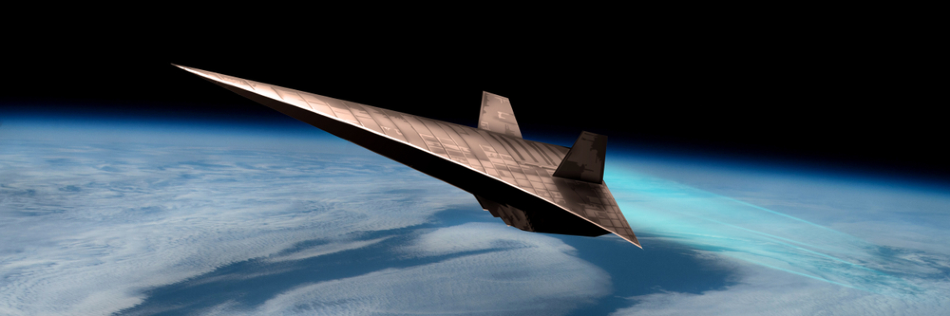
Image Credit: Shutterstock/Marc Ward
Extensive limitations remain in the everyday deployment of scramjets for high speed travel or access to space, despite decades of development.
One major challenge related to scramjets is that of inlet unstart, known as the upstream disgorging or displacement of the first inlet shock system.
The consequent detached shock that develops in front of the inlet results in large flow spillage which decreases performance, and can also create violent, unsteady loading on the engine, possibly creating its destruction.
One potential cause of inlet unstart is irregular operating environments inside of the engine’s combustion chamber, resulting in the upstream propagation of pressure disturbances which can cause the inlet shock system to displace. For example, such a system was named as the reason for the failure of the second X-51 flight.
In order to foresee, identify, and stop such unstart events, it is important to analyze the mechanisms responsible inside of the combustion chamber, and to discover how the transient events that accompany incipient unstart may appear. This is the goal of the current investigation.
Experimental Configuration
All experiments were conducted in the HEG (High Enthalpy shock tunnel Göttingen) facility of the German Aerospace Center (DLR). The HEG is a reflected-shock wind tunnel, able to recreate a large variety of flow environments at Mach numbers from around 6 to 10.
The facility’s test time is restricted to a few milliseconds; while this still enables the analysis of various high-speed flow challenges, it makes visualization, especially of unsteady phenomena, more difficult.
The model arrangement for the current investigation is a full-scale recreation of the fuelled flow path of the HyShot II flight experiment. HyShot II was the first effective investigation in the HyShot program, directed by the University of Queensland in Australia, created to offer reference data on supersonic combustion at hypersonic Mach numbers.
The layout is academic, as opposed to a practical thrust creating engine. The basic design and simple optical access meant that the Hyshot II is a perfect candidate for the current investigation.
The flowpath is demonstrated in the right section of Figure 1. The intake comprises of a basic 18º segment; the boundary layer produced on this surface is consumed by a boundary-layer bleed channel, instead of being able to enter the combustion chamber.
The combustion chamber is a constant-area duct of 9.8 mm height, 75 mm width, and 300 mm length. Hydrogen fuel is injected 58 mm downstream of the intake-side leading edge in the wall-normal direction via four port-holes.
The exhaust comprises of a basic two-dimensional expansion. A schematic illustration of the model inside of the HEG test area is demonstrated in the left hand side of Figure 1.
In the current investigations, the wind tunnel was run in a way that recreates the conditions of flight of the HyShot II flight investigation at 28 km altitude. The free-stream Mach number was around 7.4. Hydrogen fuel was injected at different pressures to generate both steady and unsteady conditions of combustion.
.jpg)
Figure 1: (Left) Schematic drawing of the HyShot II scramjet model in the HEG test section: (a) HEG nozzle; (b) valve for hydrogen injection. (Right) Flow path for the HyShot II scramjet (upside-down relative to the left schematic): (c) intake ramp; (d) boundary-layer bleed channel; (e) injection location; (f) cowl-side combustion chamber wall; (g) injector-side wall; (h) exhaust surfaces.
A critical element of the current investigation was the visualization of the combustion and flow characteristics. Windows were built in the model, allowing optical access to almost the whole combustion chamber.
The first kind of imaging used was Schlieren, in which a traditional Z-type set-up was utilized. The Schlieren method visualizes the first spatial derivative of the flow density, and is beneficial for imaging characteristics for example boundary layers, shear layers, and shocks in compressible flows.
High-speed Schlieren imaging is difficult in facilities like HEG, due to the brief test times and the extensive amounts of self-luminosity generated by the hot gases in the test flow.
The light source can be possibly overwhelmed by this luminosity. The luminosity challenge is aggravated further if the flow is combusting, as in the present example.
The CAVILUX Smart illumination laser being used for visualization in the current experiments solved this challenge, as the light’s monochromatic nature enabled the insertion of a narrow band-pass filter in the light path, successfully taking away the self-luminosity.
The inconsistent nature of the light also removed the speckle and diffraction edges normally occurring with the use of laser light sources.
An additional benefit of this light source was the short pulse duration (in this case ~30 ns), which successfully freezes the flow structures. The CAVILUX Smart was used in combination with a Shimadzu HPV-1 high speed camera, with frame rates of 16 or 32 kfps.
OH* chemiluminescence visualization was the second imaging type, similarly employing the Shimadzu HPV-1 (with no light source).
In the combustion of hydrogen, OH is one of the intermediate products. The concentration of the electronically excited radical, OH*, provides a positive signal of the onset of the flame.
OH* additionally has the benefit of strongly emitting over a narrow wavelength band (near 310 nm). By positioning a narrow band-pass filter of this wavelength before the camera, it is easy to obtain line-of-sight intensity distributions of this radical.
When Schlieren and OH* chemiluminescence visualizations are combined, relationships can be drawn between the combustion and flow characteristics observed within the combustion chamber.
Results
The results acquired for low hydrogen injection pressures will be discussed first, which contributed to the development of steady combustion conditions within the combustion chamber.
Schlieren and OH* visualizations of the flow area near the location of the injection are displayed in Figure 3 (the visualized region is around 80 mm long). The lower left corner of each image is where the injection port-holes are located.
The Schlieren image clearly shows the barrel shock generated by the interaction of the injected hydrogen with the incoming test flow, along with several of its reflections down the duct.
The injection jets themselves are also apparent and the freezing of the turbulent structures by the short laser-pulse duration is presented to good effect.
The depth of penetration is around a half of the duct height by the downstream section of the visualization window.
There is no evidence of combustion happening specifically at the point of injection in the OH* image, instead combustion seems to occur near the injector-side wall by the initial reflection of the barrel shock.
The pressure and temperature rise across the shock appear to be adequate to introduce the hot hydrogen in the boundary layer to the sides of the injection jets to conditions for ignition.
Combustion continues to be exclusive to the boundary layer until the next reflection of the barrel shock, which ‘kicks’ the flame further out into the duct and optimizes the power of combustion. These images demonstrate a distinct relationship between the flow and combustion characteristics.
.jpg)
Figure 2: (Above) Schlieren image of the flow in the HyShot II combustion chamber near the injection location (seen at the bottom left corner) for steady combustion conditions. (Below) OH* chemiluminescence image of the same region.
As the amount of injected hydrogen was made greater, it was found from pressure transducer measurements that a pressure disturbance would be created and begin to evolve upstream, triggering the onset of unstart.
High-speed visualizations recorded the unsteady development as the nature of this disturbance was not apparent. The sequences from these are presented in Figure 3.
A sequence of the flow region near the injection location is displayed in the left column (the same area as in Figure 2).
At first, (1.4 ms) the picture looks the same as the image for the steady combustion case (note that the exposure time for the OH* image is decreased in this example, which describes the evident weakness of the combustion seen).
At 3.5 ms, the arrival of a shock structure on the cowl-side wall in the Schlieren image can be observed, with a coinciding bulging feature in the OH* image.
Until a quasi-steady configuration occurs from around 4.4 ms, these continue to move upstream. The shock is lodged on the cowl-side wall just downstream of the injectors. The primary combustion area resides immediately downstream of the impingement point of this shock on the injector-side wall.
Observations of the OH* structure’s appearance as it travels upstream shows the creation of a separated flow region on the injector-side wall because the enhanced residence time in such regions significantly increases the hydrogen ignition.
The unsteady flow structures in the Schlieren images also verify this argument. In the last image (7.0 ms), the shock structure has continued to travel upstream past the injector, but this is once the steady test time has been completed, and may be a consequence of the irregular inflow conditions that subsequently evolve.
Corresponding images from the central combustion chamber further downstream are demonstrated in the right column of Figure 3.
From 2.5 ms, the creation of a shock train on the cowl-side wall can be observed and this shock train quickly gains power and travels upstream.
One of two mechanisms often cause this type of shock train in scramjet combustors: boundary-layer separation because of the challenging pressure gradient, or thermal choking because of an excess of heat release driving the flow to sonic conditions (at which point a steady flow environment is impossible).
A steady intensification of the combustion is seen in the OH* images, but clearly missing is an OH* feature that follows the motion of the shock train (as reported in the upstream sequence).
This indicates that the development of the shock train is not related to boundary-layer separation, and is instead a result of thermal choking, which opposes the results of previous authors who have analyzed this arrangement.
The boundary-layer separation documented in the upstream sequence must be created at some later point in the generation of the shock train.
.jpg)
Figure 3: Quasi-synchronous Schlieren and OH* chemiluminescence visualizations of the transient flow (near) near the injector and (right) in the central combustion chamber.
Conclusions
High-speed Schlieren visualizations were created with the use of a CAVILUX Smart laser and OH* chemiluminescence imaging, where the combustion phenomena and unsteady flow leading up to unstart in a model scramjet engine were investigated.
Incipient unstart was observed to take the form of a shock train that evolved in the central combustion chamber and consequently grew upstream.
In the comparison between Schlieren and OH* images, boundary-layer separation was ruled out as the main mechanism for this inconsistent development (even though separated areas were seen further upstream); thermal choking because of excessive heat release was isolated as the mechanism responsible.
Acknowledgments
Produced from materials originally authored by Stuart Laurence from the German Aerospace Center (DLR).
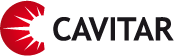
This information has been sourced, reviewed and adapted from materials provided by Cavitar.
For more information on this source, please visit Cavitar.