Surface metrology deals with the presence of sub-micron thick films, which are currently used on products well beyond semiconductor devices. Sub-micron films may be incidental – for example, oil on a machined part – or may not be important to users who are interested in the top surface. However, the film could be vital, protecting the underlying substrate or providing specific optical characteristics.
Introducing a sub-micron film to a component seldom relaxes prior surface metrology requirements in any situation. Requirements like these will often expand to include film properties such as uniformity, texture, and thickness.
Requirements for Surface Films Analysis
Ideally, surface metrology technology developed to establish sub-micron films will be capable enough to retain its performance for topography. This includes metrics such as resolution and throughput and even extends to configuration flexibility. In the case of microscope-based technologies, this highlights the fact that surface films analysis should not limit the choice of objective or zoom.
As for films metrology itself, it is important that related calibrations are sample-agnostic. A calibration artefact that is specific to a sample, for example a matching bare substrate, may be costly or impractical. It is best if measurements leverage the available optical resolution. Surface metrology that produces high-resolution height maps should do similarly for thickness. Ultimately, surface films analysis should offer definite results across a wide thickness search range. Thickness may differ widely over the measurement area, or users may not know much about thickness.
How to Measure the Surface of a Plano Optic with a ZYGO Laser Interferometer System
The Challenge and Opportunity for Coherence-Scanning Interferometry
Coherence scanning interferometry (CSI) has the potential to provide non-contact areal topography maps with sub-nm precision [1][2] across a variety of surface types, such as flat panel display components [3][4], automotive machined metal parts [5], transparent film structures, MEMS devices, and patterned semiconductor wafers. CSI is capable of measuring surface topography from the localized coherence signal, produced by interference between reflections from the sample and a reference surface. A standard CSI signal for a bare surface (with no film) is depicted in Figure 1(a): surface location basically corresponds to the peak envelope position.
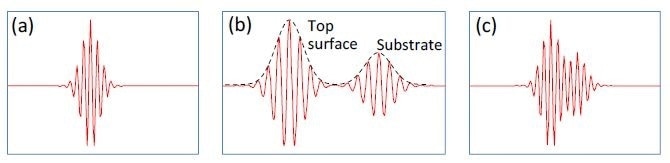
Figure 1. Typical CSI signals for (a) bare surface (no film); (b) thick film (well over 1 µm) with well separated signals from surface and substrate; and (c) sub-micron film with merged surface and substrate signals.
Generally, an extra signal from the substrate will be produced by a transparent film. In the case of thick films (Figure 1(b)), the signals are suitably separated and can be conveniently assigned to the substrate and top surface [6][7]. Conversely, for sub-micron films the substrate and surface signals combine (Figure 1(c)) and cannot be separated. This sensitivity to films presents a new possibility: the distorted CSI signal can be decoded by modeling the film effects, enabling simultaneous measurement of surface and thickness.
Model-Based CSI
Previous Approaches
In this context, model-based CSI replicates signals over a predicted range of film properties, and selects the most appropriate match with the measured signal. It has been shown in various forms [8][9][10][11][12], by using frequency-domain analysis to integrate models for the system and of the part being determined.
There is a caveat with model-based CSI: it is essential that film properties are at least partially known, to bind the search space and prevent degenerate solutions. This is often essential for visible-spectrum refractive indices for film as well as substrate, with the thickness of the film left as the unknown parameter to be evaluated.
Practical trade-offs exist between field of view and throughput in earlier model-based approaches because of intensive computation, and often precluded the use of high-NA objectives. Thanks to the precursor to the method described here, high-NA measurement of samples with complex reflectivity is attained [13][14][15]. This is achieved with the help of a system model derived from the objective pupil to produce signal libraries across the wide search range (Figure 2). The pupil calibration can be performed with the help of a specialized Bertrand tube-lens.
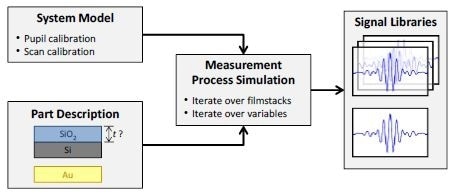
Figure 2. Signal library generation, combining a system model handling arbitrarily high NA with a model of the part being measured.
Presented Approach
While the method illustrated in this article is similar in principle to its predecessor [13], it divides calibration into two parts: an on-tool component and a nominal pupil calibration performed with the preferred measurement configuration. Only standard CSI hardware is used in this procedure, which can be applied with any interferometric objective. The entire measurement sequence is shown in Figure 3.
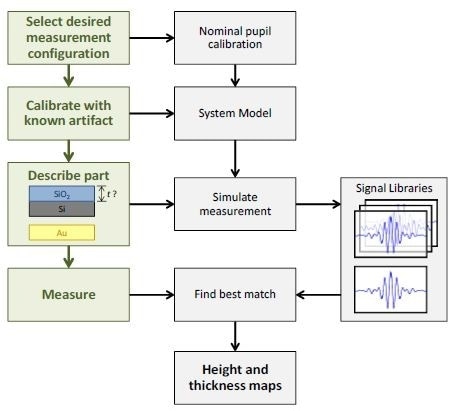
Figure 3. Measurement flow for presented approach. Steps performed by the user are shown in green.
The best-match signal search continues to be unchanged, with the key difference being that optimized processing – enabled by higher computing power – now facilitates full-field analysis at megapixel camera formats. Processing time is usually under 10 seconds for full-field analysis and depends on the pixel count and search range. Any flat artifact with known visible-spectrum refractive indices is used for calibration. There is a need for no part-specific calibration, which is advantageous for parts with difficult geometries or reverse engineering.
Example Measurements
A wide variety of parts with sub-micron films and dissimilar materials were measured using a contemporary commercial CSI microscope [16]. A silicon carbide flat was used to perform calibration for each measurement configuration. This silicon carbide flat is also used for standard-CSI calibrations.
Films Applications Requiring a Wide Search Range
A certain degree of degeneracy, capable of yielding multiple solutions to the same set of model parameters, is possessed by all model-based methods. With regard to films metrology, the result can be incorrect or ambiguous film thickness values that generate apparently acceptable matching signals to the experimental data. A solution can be obtained by limiting the thickness search range, but this may be precluded by inadequate knowledge or major differences in thickness over the measurement area. A more attractive option refers to the detection of small but clear signal details that allow for a wide search range, and make it possible to remove potential degenerate solutions.
Figure 4 illustrates a silicon substrate coated with silicon oxide with center thickness ~1.2 µm. The coating’s outer rim has a thickness gradient down to zero (bare silicon), where the fixture masks the substrate during evaporation. This transition region was measured with a 20X Mirau objective, using an oxide-on-silicon model with a search range of 0 to 1300 nm, and separate processing for all pixels in the field of view.
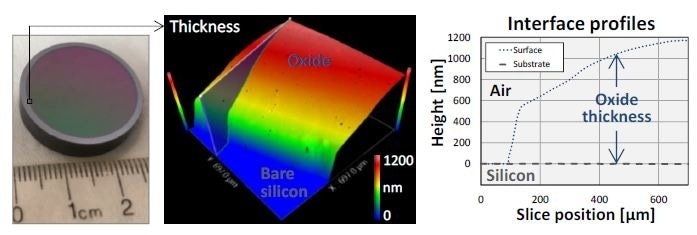
Figure 4. Oxide-gradient sample measured at the film boundary using a 20X Mirau objective. The thickness map ranges from 0 (bare silicon) to ~1.2 µm. The substrate profile, derived by subtracting thickness from the top surface, is flat to ~1 nm.
Figure 4 also shows the resulting thickness map and a cross-sectional slice covering the entire thickness range. The difference in thickness is continuous and monotonic as expected, and indicates that the thickness was explicitly established throughout the wide search range. The silicon substrate derived by subtracting thickness from the top surface is flat and within ~1 nm, as expected.
Films Metrology over a Wide Range of Magnification
The large choice of magnifications of CSI enables a wide range of surface metrology applications, right from measuring form to examining microscopic defects. This flexibility, along with the addition of thin films, remains just as desirable, and should extend to film’s metrology itself. Model-based CSI should ideally work across the whole selection of optical configurations.
Thickness maps, shown in Figure 5, are established for an oxide-on-silicon film standard (NIST certified thickness of 96.6 ± 0.4 nm) using four different combinations of zoom/objective covering a 70X range in magnification.
For all cases, an oxide-on-silicon model with a search range of 0 to 1200 nm was used in the analysis for all pixels in the field of view. The wide search range is intentional in order to validate robustness and mimic the case of film thickness being unknown.
A complete picture of film characteristics is provided by the broad range of magnifications. The 1.4X Zygo Wide Field (ZWF) objective [19] is capable of capturing the whole certified region in a single field of view and reveals slow variations in film thickness. Additionally, the black rings indicate where the oxide is etched down to the silicon substrate, and the concentric rings correspond to deliberate patterning in the film. Smaller-scale thickness differences and even surface scratches that result from handling this laboratory sample are shown by measurements performed at higher magnifications. Details of every single striation defect were revealed by the highest-magnification map, which, in turn, was achieved with a 50X Mirau.
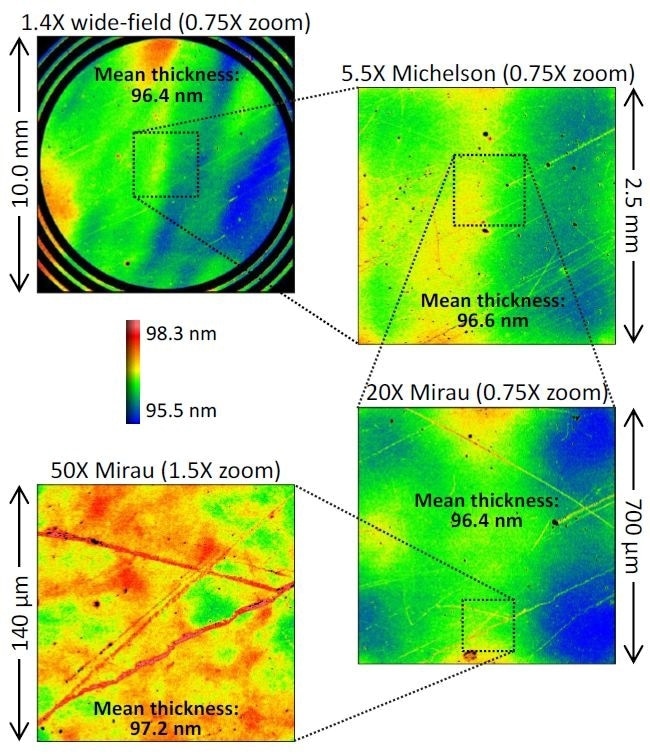
Figure 5. Thickness maps for an oxide-on-silicon film standard (certified thickness 96.6 nm), measured over a 70X range of magnification. The agreement in mean thickness is better than 1 nm across all objectives.
Model-based CSI provides surface maps, together with the thickness maps (Figure 4). A derived map of the substrate surface is created by subtracting the thickness of film from the top surface. Together, these maps allow for additional validation and metrology. Again, the range of magnifications enables complete surface analysis.
Results obtained from the 1.4X ZWF capture the regions of exposed silicon substrate and oxide film (Figure 6). The surface map shows the steps between the oxide and bare silicon. From the manufacturing sequence (blanket thermal oxidation followed by patterned etch down to silicon substrate), surface steps are anticipated to match the thickness of films. Or, equivalently, that the underlying silicon substrate should remain continuous. This is confirmed by the substrate map, validating the overall measurement.
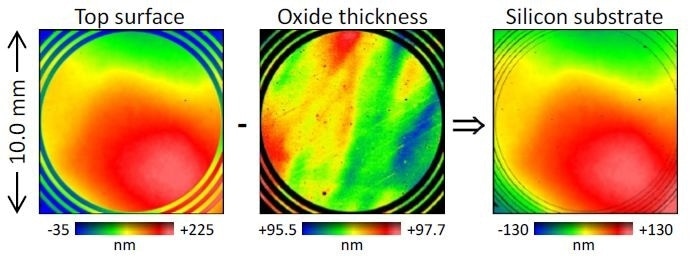
Figure 6. Surface, thickness, and substrate maps for oxide-on-silicon film standard measured using a 1.4X ZWF objective
Textural variations between the surface, thickness, and substrate are shown by measurements carried out at higher magnification. Figure 7 shows interface maps obtained from the 20X Mirau, with form (4th-order polynomial) removed. Both striations and orange-peel texture are shown by the top surface. In the interim, striations dominate the film texture while the substrate shows orange-peel texture but has no striations. Together, these maps show that the orange-peel texture is contributed by the substrate and the striations reside in the top surface of the film (probably from usage, and not an original defect).
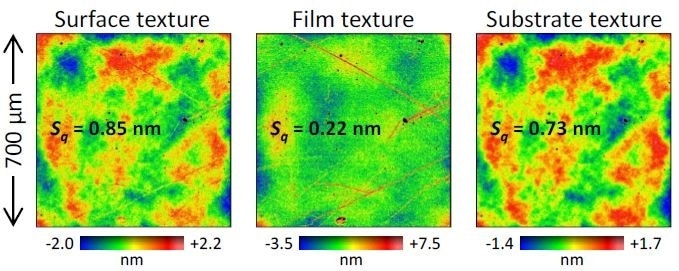
Figure 7. Maps for oxide-on-silicon film standard measured with a 20X Mirau objective, with form removed to reveal texture.
Parts with Dissimilar Materials
If there are differences in phase-change on reflection (PCOR), even bulk materials can confound conventional CSI. This can occur with a variety of materials [13]. For example, a traditional CSI measurement of a glass/metal step will be biased by ~10 to 20 nm, with the metal appearing lower than it really is [18].
Traditionally, a part can consist of bulk, dissimilar materials and films. Figure 8 shows the fabrication sequence for such a sample, in the form of trenched oxide-on-silicon with a partial gold overcoat.
A silicon substrate was first used, and about 1 µm of thermal silicon oxide was grown on it. This was followed by the formation of trenches in the oxide through photoresist masking and a partial etch, and thinner oxides were intentionally left at the bottom of the trench. Finally, trenches were gold-coated by a lift-off sequence (photoresist masking, global gold deposition, photoresist strip). Target gold thickness was about 90 nm, which was sufficient to prevent film effects from the underlying oxide.
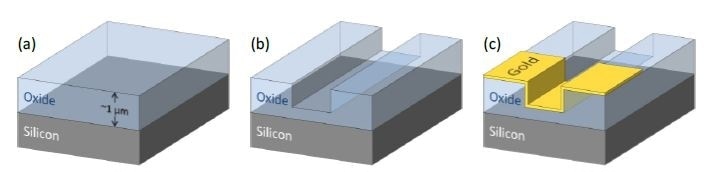
Figure 8. Fabrication sequence for oxide trench sample with partial gold overcoat: (a) grow ~1 µm of thermal oxide on a silicon substrate; (b) form oxide trench; (c) deposit partial gold overcoat.
A 50X Mirau objective was used to determine this sample, with analysis customized to each region: a bulk-gold model (i.e. no film) was used for the gold overcoat and an oxide-on-silicon model with a search range of 0 to 1200 nm was used for the uncoated oxide. Figure 9 shows thickness and surface maps for a pair of trenches over a gold-coating boundary.
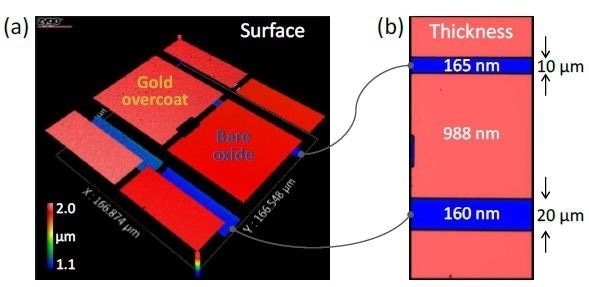
Figure 9. Maps for (a) surface and (b) bare-oxide thickness of trench-oxide sample, measured using a 50X Mirau objective
The thickness of the unetched oxide was determined and identified to be 988 nm. For the trenches, thickness depends on width: 160 nm and 165 nm for the 20-µm trench and 10-µm trench, respectively. By subtraction, thickness results highlight a trench depth of 823 nm for the 10-µm trench and 828 nm for the 20-µm trench.
This is confirmed by the results shown in Figure 10, showing cross-sectional surface-map profiles through both trenches, and on either sides of the coating boundary. That is, with and without gold overcoat. The measured trench depths coincide with thickness-suggested results: better than 1 nm.
Overall, surface and thickness results reveal that the oxide-etch process was about 0.6% slower in the narrower 10-µm trench. To verify this further, it was identified that trench-depth measurements on both sides of the coating boundary – obtained using independent analyses with and without film effects – are better than 1 nm.
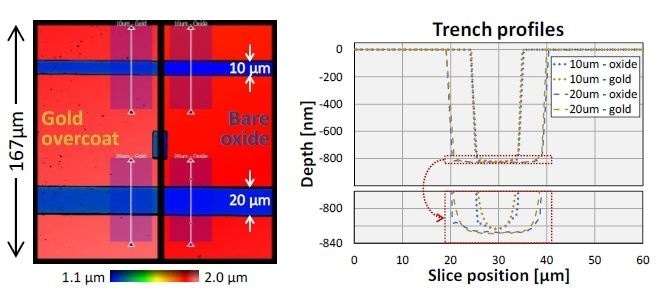
Figure 10. Profiles for trenches with width 10 µm and 20 µm, measured on opposing sides of gold-coating boundary. Measured trench depth is better than 1 nm across the gold-overcoat boundary. The 10-µm trench is ~5 nm shallower than the wider 20-µm trench, consistent with its oxide thickness measuring as 5 nm thicker (Figure 9(b)).
There are specific applications where correct topography is needed across dissimilar regions. For this type of sample, this corresponds to the gold thickness step across the coating boundary.
Figure 11 shows gold-thickness profiles that were determined over dissimilar thicknesses of oxide films: 160 nm inside the 20-µm trench and 988 nm in neighboring unetched oxide. A gold thickness of around 85 nm with agreement to ~1 nm is revealed by both profiles.
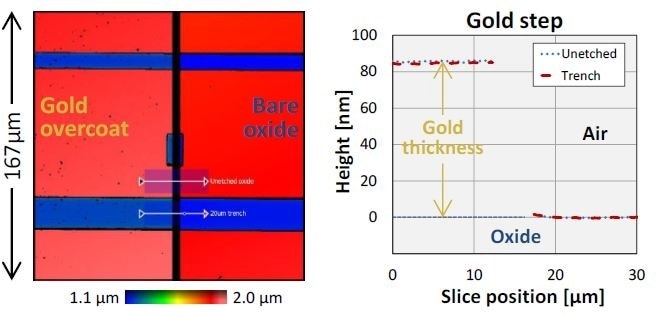
Figure 11. Step profiles across gold-coating boundary, measured within the 20-µm trench and on adjacent unetched oxide. Measured gold thickness is about 1 nm.
Conclusion
This article demonstrates how the presented approach to model-based CSI permits for full-field films surface metrology, across an entire range of interferometric objective magnification. It shows that it produces high-resolution maps of film and surface thickness. Measurement time for most practical search ranges is similar to that of conventional CSI, and calibration is sample-agnostic. PCOR-corrected topography is offered by model-based CSI, beyond transparent films, for all combinations of dissimilar materials with known visible-spectrum refractive indices, including metals.
Additionally, results reveal single-nm self-consistency between thickness and topography maps, if refractive indices are well known. This provides a major caveat with model-based CSI: insufficient knowledge of material properties limit performance, and can even prevent meaningful measurements. For model-based CSI, a natural step should be to extend capabilities to withstand uncertainty in the properties of materials.
Acknowledgments
The original work presented in this paper benefited from key contributions and input from Xavier Colonna de Lega, Jim Kramer and Peter de Groot.
References
[1] de Groot, P., “Principles of interference microscopy for the measurement of surface topography”, Advances in Optics and Photonics 7 (1), 1-65 (2015).
[2] ISO, [25178-604:2013(E): Geometrical product specification (GPS) – Surface texture: Areal – Nominal characteristics of non-contact (coherence scanning interferometric microscopy) instruments] International Organization for Standardization, Geneva (2013).
[3] Grigg, D., Garden, R., Mino, M., Lu, H., and de Groot, P., “New optical metrology techniques for color filter inspection and process control”, Proc. IDW 11th international display workshops, Niigata, Japan (2004).
[4] He, Z., Zheng, J., Garden, R., de Groot, P., “New optical 3D-CD metrology techniques for liquid crystal display manufacture inspection and process control”, Proc. Asia Display, Shanghai, China (2007).
[5] Wyant, J. C., “How to extend interferometry for rough-surface tests”, Laser Focus World, 131-135 (1993).
[6] Flournoy, P. A., McClure, R. W., and Wyntjes, G., “White-light interferometric thickness gauge”, Appl. Opt. 11, 1907 (1972).
[7] Colonna de Lega, X. and de Groot, P., “Transparent film profiling and analysis by interference microscopy”, Proc. SPIE 7064, Interferometry XIV: Applications, 70640I (11 August 2008).
[8] de Groot, P., “Method and apparatus for surface topography measurement by spatial-frequency analysis of interferograms”, US Patent No. 5,398,113 (14 March 1995).
[9] de Groot, P.J. and Colonna de Lega, X. “Signal modeling for low-coherence height-scanning interference microscopy”. Appl. Opt., 43, 4821-4830 (2004).
[10] Kim, S.-W. and Kim, G.-H. “Thickness-profile measurement of transparent thin-film layers by white-light scanning interferometry”, Appl. Opt. 38, 5968 (1999).
[11] D. Mansfield, “The distorted helix: thin film extraction from scanning white light interferometry,” Proc. SPIE 6186, paper 23 (2006).
[12] D. S. Wan, “Measurement of thin films using Fourier amplitude,” US Patent No. 7,612,891 (3 November 2009).
[13] de Groot, P. and Colonna de Lega, X., “Optical Topography Measurement of Patterned Wafers”, AIP ULSI Conference Proceedings 788, 432 (2005).
[14] Colonna de Lega, X., “Generating model signals for interferometry”, US Patent No. 7,619,746 (17 November 2009).
[15] Colonna de Lega, X. and de Groot, P., “Characterization of materials and film stacks for accurate surface topography measurement using a white-light optical profiler”, Proc. SPIE 6995, 69950P (2008).
[16] Zygo Corporation, [Nexview Optical Profiler], Specification sheet SS-0095 09/12 (2013).
[17] Biegen, J. F., “Determination of the phase change on reflection from two-beam interference”, Opt. Lett. 19, 1690-1692 (1994).
[18] Park, M.-C. and Kim, S.-W., “Compensation of phase change on reflection in white-light interferometry for step height measurement”, Opt. Lett. 26, 420-422 (2001).
[19] de Groot, P. and Biegen, J.F., “A new class of wide-field objectives for 3D interference microscopy”, Proc. SPIE 9525, Optical Measurement Systems for Industrial Inspection IX, 95250N (2015).
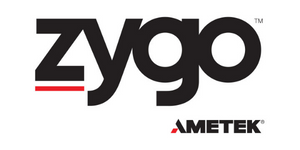
This information has been sourced, reviewed and adapted from materials provided by Zygo Corporation.
For more information on this source, please visit Zygo Corporation.