A Computer-Generated Hologram (CGH) is a precise optical component capable of altering the test-leg wavefront from an interferometer. It facilitates the measurement of surface and wavefront properties for a wide range of optical shapes or optical system wavefronts.
Typical CGHs are extremely accurate binary diffractive optics made by lithographic methods. Additionally, they allow the creation of wavefronts of almost any form, depending on how the diffractive pattern is designed. This combination of flexibility and accuracy makes the metrology of complex optical surfaces possible, such as aspheres, freeforms, conics, and off-axis sections.
Users can integrate a complete metrology system for surface or wavefront testing to advance their CGH application.
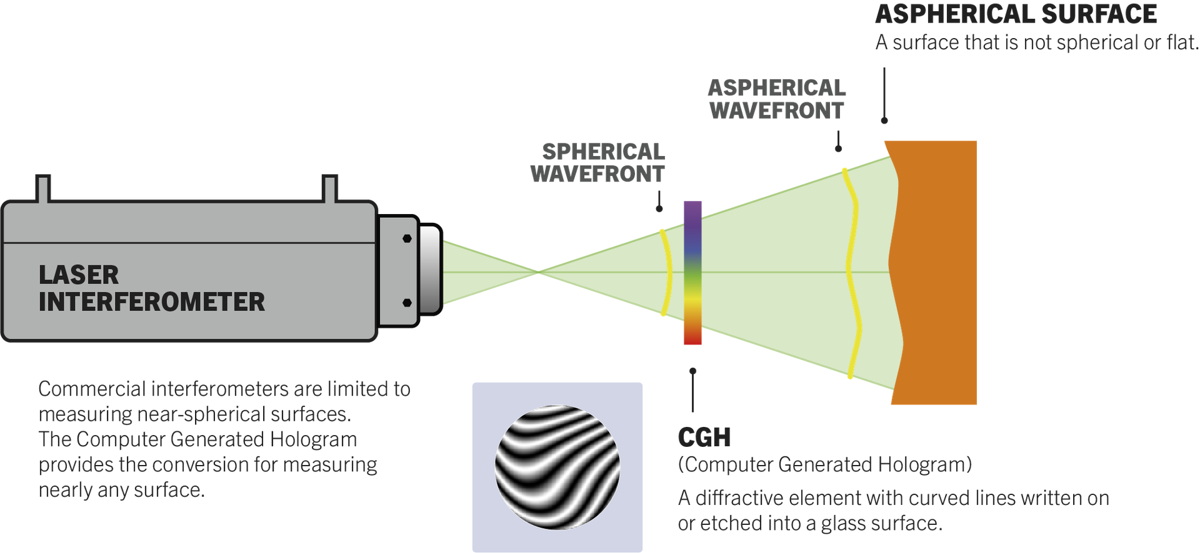
Image Credit: AOM - Arizona Optical Metrology LLC
CGH Benefits
Interferometry can obtain excellent metrology for optical surfaces. However, the surface or wavefront types that can be measured by interferometers natively are restricted to spherical and flat shapes.
Computer-generated holograms (CGHs) circumvent this shape constraint, allowing measurements of aspheres, freeforms, conics, and off-axis sections while retaining the many advantages of interferometry.

Image Credit: Safran Reosc
- Fast, non-contact, high accuracy, high resolution, and full aperture measurement are a unique and useful combination in optical metrology.
- Flexible - measures almost any optical surface shape.
- Production friendly - Amortize the cost of a CGH across the volume of units produced.
- Create a design that can accommodate almost any interferometer wavelength.
- Cost-effective: Use currently available interferometry and only purchase CGHs for specific test optics when necessary.
- Easy to obtain—Custom CGHs from AOM can be obtained in eight weeks or less.
Custom CGH Technical Details
CGHs are incorporated into conventional size and mechanical interface formats. CGHs are made of a fused silica substrate that has been etched or printed with a diffractive pattern.
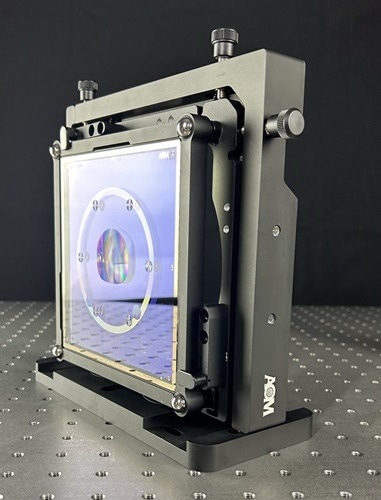
Custom CGH and alignment stage from AOM. Image Credit: AOM - Arizona Optical Metrology LLC
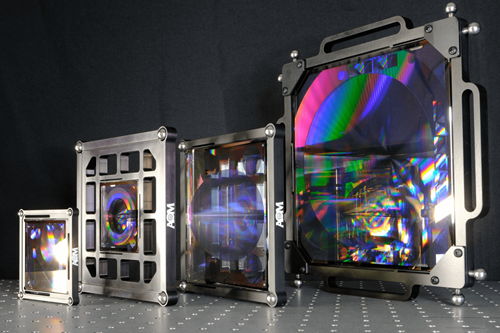
Custom CGHs are offered in 3-inch, 6-inch, and 9-inch sizes. Image Credit: AOM - Arizona Optical Metrology LLC
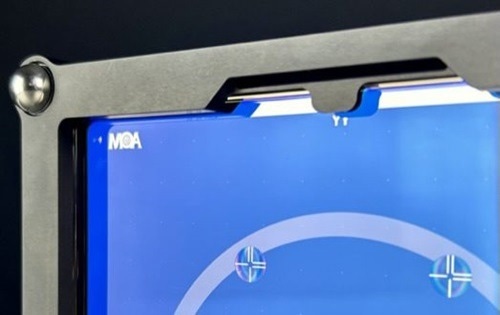
CGH with AR-coated back surface. Image Credit: AOM - Arizona Optical Metrology LLC
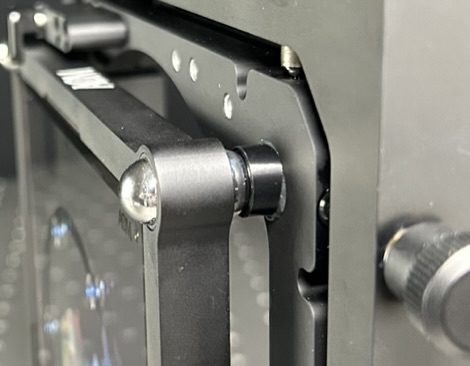
CGH cell kinematic mounting to AOM alignment stages. Image Credit: AOM - Arizona Optical Metrology LLC
Custom CGHs are available with:
- Square 3-inch, 6-inch, and 9-inch substrates to accommodate various test optic sizes. Every CGH substrate has a polished, parallel surface that maintains accuracy during an interferometric test. It is even possible to custom-core or shape substrates to fulfill the demands of a given application.
- An AR coating on the CGH back surface removes unwanted reflections in the interferometric test.
- CGHs are installed in a mechanical cell that offers an easy-to-mount mechanical alignment step and a low-stress mounting interface.
- An optional .cgh file and Morpheus™ software - enables measurement data post-processing to calibrate out the substrate error, analyze and remove misalignment errors in the test, lateral mapping distortion correction, and even a measurement uncertainty analysis
- Final reports of as-built parameters and verified QC checks are included in custom CGHs.
How to Specify a CGH Test
Various optical surface designs, sizes, optical materials, and even the quantity of surfaces that have to be examined can be selected for a computer-generated hologram. Defining the following is crucial when specifying a CGH test:
- The optical prescription defines the surface to be created and evaluated.
- Test uncertainty: How precisely must the surface figure inaccuracy be known?
- Optical surface reflectivity or material- Surface reflectivity at the test wavelength determines the type of CGH (Amplitude or Phase) to apply.
- Alignment requirements - Does the optical surface require alignment to mechanical datums such as an OD or mounting holes/pins?
- System requirements: Is the optic employed in a system that requires alignment with other optics?
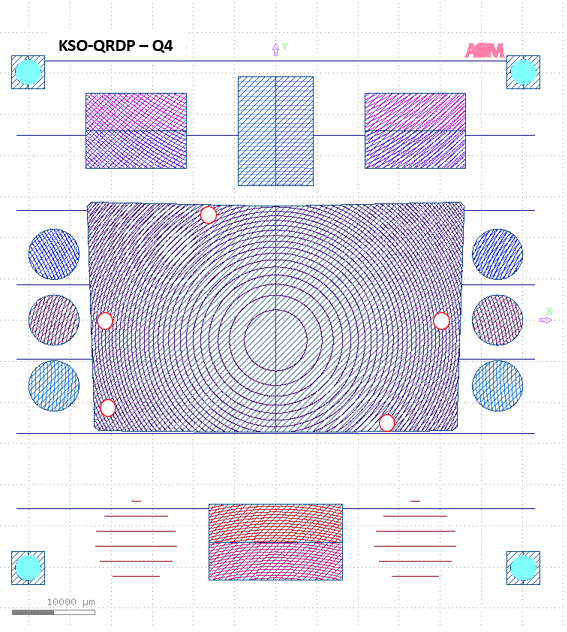
Image Credit: AOM - Arizona Optical Metrology LLC
After delivering the information above to AOM as part of a CGH test design, its engineering team will generate a preliminary CGH test design for evaluation and discussion, with the option of making adjustments, adding requirements, or considering a Metrology System for a comprehensive metrology solution.
Other CGH Tests
CGHs can be used to examine more than just aspheric lenses and mirrors.
With test configurations made possible by CGHs, more intricate optical surfaces can be qualified to extreme precision.
Users can test the optical system wavefront, surface-to-surface alignment of optical elements, and wavefronts at varied field angles using CGHs.
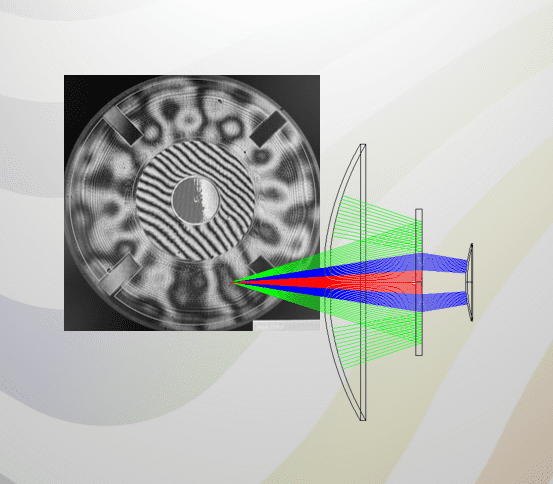
Image Credit: AOM - Arizona Optical Metrology LLC