When procuring optics for use in critical applications such as aerospace, defense, semiconductor, research, and life/health sciences, risk mitigation is vital. Risks are events affecting timeline, cost, and technical performance. This article outlines four key capabilities to look for in optical coating suppliers in order to minimize program risks.
1. Vertically Integrated Manufacturing
Timeline and Transportation
The fabrication, testing, coating, and assembly of optics by a single manufacturer has a number of advantages. An overall reduction in project completion time is the most obvious advantage.
By coordinating all activities, a single supplier takes full responsibility for the completion of the project. This eliminates the requirement to transport optics to a coating supplier, then back to the originator for final acceptance testing and perhaps a third supplier for assembly, saving both expense and time.
After receiving the optics from Supplier A, ultimately you are responsible for ensuring damage does not happen when sending the optics on to Supplier B. In these cases, it is a prudent choice to insure high quality optics.
Most optics represent a significant financial expenditure, so any delays in reimbursement by the insurance company will only lengthen the project delays, completely derailing a program schedule.
Technical Performance: Taking Responsibility
When working with multiple suppliers, establishing who is at fault when an optic fails to meet the specifications is a risk which is not immediately apparent. For instance, a high aspect ratio optic with a demanding surface figure. Did coating stress distort the optic or did the fabricator fail to meet specifications?
If the root cause of the failure is ambiguous or unknown, assigning responsibility and taking corrective action is impossible. The substrate will need grinding, polishing, and recoating services from additional suppliers even if one supplier is willing to take responsibility.
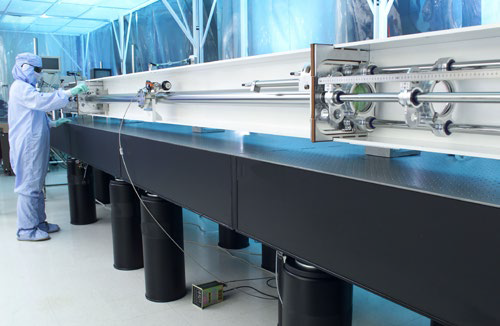
A single source supplier of coated optics and optical assemblies takes full ownership of all manufacturing processes. Image Credit: Zygo Corporation
For over 45 years, ZYGO has been fabricating cutting-edge optics. Before developing their own coating capabilities in the 1980s, they had to learn this painful lesson first hand. It was those situations that inspired them to develop the broad range of coating capabilities they now possess.
ZYGO’s customers know that they can rely on a single supplier who has the technical expertise to choose the most appropriate substrate material and then fabricate, coat, assemble, and carry out metrology on their unique optics.
Keeping it Clean
If applied to a substrate that is not properly cleaned, then a durable, high quality coating design is subject to failure. When looking at potential coating suppliers, it is vital to enquire about their cleaning processes, facilities, and packaging capabilities.
ZYGO’s facilities include Class 1000 and Class 100 cleanrooms which are set up to process optics sensitive to Airborne Molecular Contaminants. Cleaning standards are certified by the National Ignition Facility (NIF) and per MIL-STD-1246. They can ship completed assemblies and optics in vacuum or nitrogen purged packaging.
2. Experienced In-House Design Team
Theory vs. Real Life
It is standard practice to model initial designs using a number of software applications when designing sophisticated coatings. Yet, when real-world variables clash with textbook theories, will these coatings perform as expected?
If a high performance coating is required for your application, it is crucial to ask prospective suppliers about their prior experience in applying similar coatings to similar substrates.
For example, when coating very large optics, it is vital to understand the supplier’s level of experience in handling, cleaning, and controlling coating uniformity. Understanding the variables involved is crucial to ensuring the finished product meets or exceeds specifications. Decades of experience enable ZYGO’s design team to use out-of-the-box thinking to solve complex, unique problems.
In addition to designing coatings, ZYGO’s in-house research and development engineers possess the skill set to design and fabricate proprietary fabrication equipment and fixtures for optics. Their production staff has techniques in place to control post-coating figure, surface quality, and uniformity — even with unusually shaped or large optics.
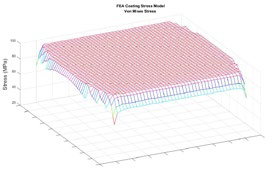
Coating stress simulated in FEA. Image Credit: Zygo Corporation
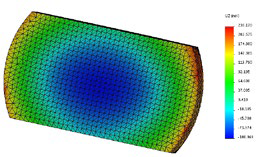
Coating stress from left used to predict figure change. Image Credit: Zygo Corporation
Environmental and Durability Factors
A custom coating design could be needed in order to meet the durability and environmental specifications for an application. Usually, the end-users of coated optics are not interested in the type of deposition technology employed to apply a coating onto a substrate.
Even so, a strong argument can be made that top tier coating suppliers must have a number of deposition technologies at their disposal to balance the requirements of a coating’s spectral performance and durability with schedule and cost.
ZYGO uses a number of deposition technologies which enable them to optimize their manufacturing processes. They use enabling technologies like resistive sputtering and ion-assisted deposition, in addition to more conventional processes.
It is crucial to use a coating supplier that has in-house testing capabilities for your durability and environmental requirements. Coating designs are tested by utilizing witness samples throughout the development phase and during production for performance verification.
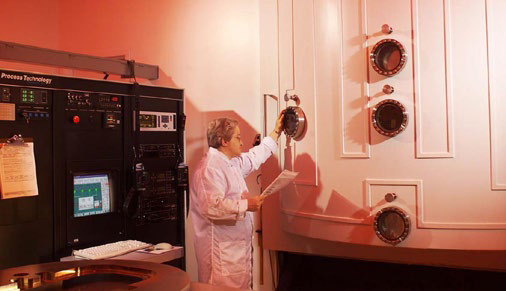
High reflective, antireflective and specialty coatings are applied in 72-inch coating chambers. Image Credit: Zygo Corporation
Outsourcing these tests both increases costs and slows down the coating design and production processes significantly. Typical requests include ISO and military specifications for temperature cycling, salt fog, humidity, adhesion, and abrasion.
ZYGO maintains the capability to carry out all of the testing listed here, so they can develop advanced coatings in an efficient and cost-effective manner.
Stress Affects Optics – Not Just Engineers
When certain types of coatings are applied an optic is at risk for deformation. This risk is dependent on the coating materials, deposition technique used, layer count, substrate material, and aspect ratio.
The stress that is applied can distort an otherwise perfect substrate so that it will no longer adhere to transmitted wavefront or flatness requirements. The proprietary coating design is almost never shared with the fabricator when choosing different suppliers for fabricating and coating an optic.
The fabricator is unable to anticipate and compensate for the stress induced on the optic by the coating without that information. Choosing a single supplier, like ZYGO, to fabricate and coat an optic enables the engineering and manufacturing teams to share coating design information freely to create an optic that meets specifications both before and after the coating is applied.
Always be sure to ask suppliers if they have established methods for coating stress compensation and if they will verify specifications both before and after coating is applied.
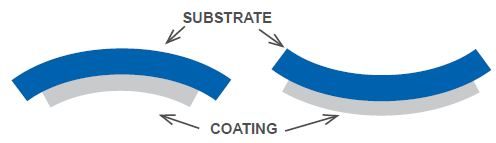
ZYGO utilizes various techniques to prevent substrate deformation due to tensile or compressive coating stress. Image Credit: Zygo Corporation
3. Sophisticated Metrology
If You Can’t Measure An Optic, You Can’t Produce It
It is crucial to understand the metrology capabilities of potential coating suppliers. A coating supplier must possess a spectrophotometer that can measure reflectance and transmission at various angles of incidence and polarizations.
The chosen supplier must have interferometric testing equipment on hand to ensure an optic meets all specifications before and after coating. It is particularly desirable that the interferometer is large enough to test the optic at full aperture. In order to ensure that accurate results are acquired, ask suppliers if their equipment is in a climate-controlled environment.
Can the Supplier Design Appropriate Holding Fixtures and Provide an Error Budget Based on Your Testing Requirements?
ZYGO’s metrology equipment and expertise are recognized around the globe. Their equipment includes interferometers up to 32 inches (813 mm) diameter, enabling them to make full aperture measurements on large optics without the requirement to use stitching.
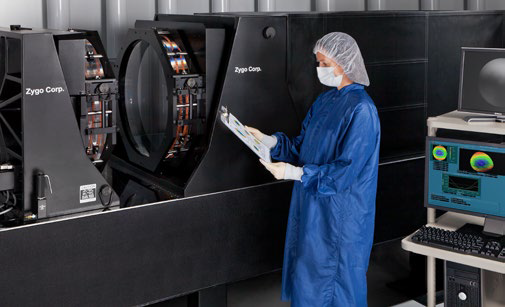
Large aperture interferometry ensures optics meet specifications before and after coating. Image Credit: Zygo Corporation
4. Refurbishment Services
Repolishing and Recoating at One Location
Program risks do not end with the delivery of a new assembly or optic. A premier coating supplier must be able to support their optics after they leave a facility and face the wear and tear of the real world, whether that is after extended use in an ultra-high power laser system or from the battlefield.
By definition, high-durability coatings cannot simply be chemically stripped and reapplied. Grinding the substrate to remove the damaged coating and repolishing to meet specifications prior to recoating is necessary for rework. Make sure that the chosen coating supplier has the in-house capabilities to carry out all of the required refurbishment steps.
Typically, extensive delays happen when the substrate requires transportation to different facilities to complete the rework process when working with a coating supplier that does not possess ZYGO’s full in-house capability to manufacture substrates. Choosing the right coating supplier ensures support is available over the life of a program.
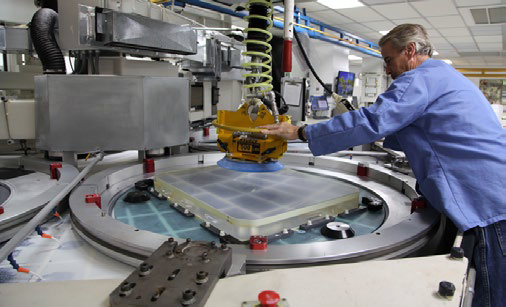
Refurbishing highly durable coated optics requires in-house grinding and polishing capabilities. Image Credit: Zygo Corporation
Acknowledgments
Produced from materials originally authored by Michael Albrecht from Zygo Corporation.
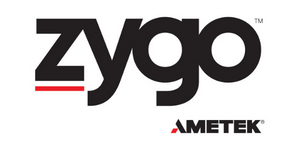
This information has been sourced, reviewed and adapted from materials provided by Zygo Corporation.
For more information on this source, please visit Zygo Corporation.