Background
PI Ceramic can manufacture almost any shape of PICMA® multilayer piezoelectric actuator using the latest production technology. All surfaces are hereby covered with a ceramic isolation layer. Not only are variable basic shapes possible, such as round or triangular cross-sections, but also insulated internal bores on benders, chips or stack actuators, therefore making their integration easier.
Award-Winning PICMA® Technology: A Revolution in Durability
PICMA® multilayer piezoelectric actuators from PI Ceramic are the only monolithic, multilayer, piezoelectric actuators in the world which are completely encapsulated in a ceramic insulation layer. The patented PICMA® technology makes it possible to manufacture components with a particularly long lifetime. Decades of experience with PICMA® series in various applications show that the lifetime has been increased by at least a factor of 10 compared to previously used, conventional, polymer-coated, multilayer piezoelectric actuators.
PICMA® multilayer piezoelectric actuators are based on a special PZT (lead zirconate – lead titanate) ceramic, which ideally combines the desired characteristics of the components such as high stiffness, low electrical capacity, high specific displacement, low load and temperature dependence of the specifications and long lifetime.
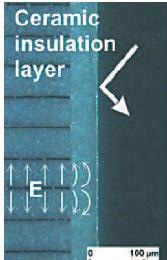
Figure 1.The ceramic insulating layer prevents the ingress of water molecules and reliably protects the sensitive internal electrodes from mechanical damage and dirt.
The internal electrodes and the ceramic are jointly sintered (co-fired technology) to create a monolithic piezoceramic block (Fig. 1). This block is protected against humidity and damage from increased leak current by a ceramic isolation layer. Therefore, PICMA® multilayer piezoelectric actuators are far superior in terms of reliability and lifetime to conventional, polymer-coated, multilayer, piezoelectric actuators. The construction with the ceramic insulation layer results also in a high resonance frequency, making the actuators ideally suited for high-dynamic operation. Large Temperature Range – Optimum UHV Compatibility – Minimal Outgassing – Neutral in Magnetic Fields The particularly high Curie temperature of 320 °C allows for a usable temperature range of up to 150 °C, far beyond the 80 °C limit of conventional multilayer actuators. This and the exclusive use of inorganic materials provide the optimum conditions for use in ultra-high vacuums: No outgassing and high bake-out temperatures. PICMA® piezoelectric actuators even work in the cryogenic temperature range, although at a reduced travel. Thanks to their construction that is based solely on non-ferromagnetic materials, the actuators have an extremely low residual magnetism in the order of a few nanotesla.
Optimized Electrodes for High Electric Currents
Research on the control electrodes led to a further improved design. The patented, meandering form of the external electrodes supplies the electric current evenly to the internal electrodes (Fig. 2). The contact here is chosen so that it remains electrically stable and mechanically flexible even at high currents up to 20 A and more, for extreme dynamic requirements. This improves the lifetime of the actuator in applications with rapidly changing fields.
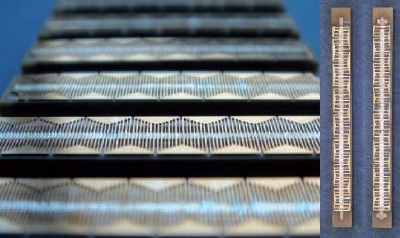
Figure 2. Patented, meander-shaped external electrodes.
Influences on the Lifetime of a Piezo-Ceramic Actuator
Three essential factors affect the lifetime of piezo ceramics in positioning applications: Humidity, operating voltage and temperature. Ingressing moisture and the electric field applied can cause electrochemical transport processes in the component, which are accelerated by higher temperatures. The result is a short circuit between the electrodes, which can cause irreparable damage to the actuator. The actual application determines the extent to which the individual factors have an impact.
Benefits of Low Operating Voltage on Piezoelectric Actuator
In contrast to most commercially available multilayer piezo actuators, PICMA® actuators achieve their nominal displacement at operating voltages significantly below 150 V. This is achieved by using a particularly finegrained ceramic material which allows a lower depth of the internal layers. The products described in this document are at least partially protected by the following patents: German patent no. 10021919 German patent no. 10234787 German patent no. 10348836 German patent no. 102005015405 German patent no. 102007011652 US patent no. 7,449,077. In positioning applications, the piezoelectric actuator is typically operated at constant voltage to maintain one position over an extended period of time. The lifetime of piezoelectric actuators is however affected especially by the voltage and the humidity.
Water Resistance of Polymer-Coated Piezoelectric Actuators
The most important feature which protects PICMA® actuators against ingressing moisture is the monolithic construction with the ceramic insulation layer. The ingression of water molecules is effectively suppressed, which is impressively documented by measurements of the leak current (Fig. 3). Increased values are a sign of deteriorating insulation resistance and thus of a decrease in lifetime, as can be seen with polymer-coated actuators.
Comparison Between Ceramic and Polymer Coated Piezoelectric Actuators
The high reliability makes it virtually impossible to experimentally measure the lifetime of PICMA® actuators under realistic operating conditions. To estimate the lifetime, tests under extreme loading conditions are used. These tests are then confirmed in a long-term series of tests that are carried out under realistic conditions (see “Realistic study”).
Accelerated Degradation of Piezo Ceramics
An increased relative humidity combined with high ambient temperatures and control voltages sometimes above the nominal voltage range leads here to an accelerated degradation of the piezo ceramics. The boundary conditions are subsequently corrected using a mathematical model and this results in a specification for the average lifetime (Mean Time To Failure, MTTF) in a realistic application. Conventional, polymer-coated piezoelectric actuators typically survive continuous use at increased humidity for about 30 days (Fig. 4), whereas PICMA® multilayer piezoelectric actuators are still working reliably after more than four years! The results were obtained from a representative random sample of PICMA® 5 x 5 x 18 (P-885.50) and are typical for the complete PICMA® product range.
![PICMA® piezoelectric actuators (bottom curve, red) compared to polymercoated multilayer piezoelectric actuators. The high insulation resistance of the PICMA® actuators remains stable over several time decades, whereas conventional, polymer-coated actuators exhibit a significantly increased leak current after a few hours. (Test conditions: 100 VDC, 25 °C, 70 % relative humidity [RH])](https://d36nqgmw98q4v5.cloudfront.net/images/Article_Images/ImageForArticle_219_450975079255555542339.jpg)
Figure 3. PICMA® piezoelectric actuators (bottom curve, red) compared to polymercoated multilayer piezoelectric actuators. The high insulation resistance of the PICMA® actuators remains stable over several time decades, whereas conventional, polymer-coated actuators exhibit a significantly increased leak current after a few hours. (Test conditions: 100 VDC, 25 °C, 70 % relative humidity [RH])
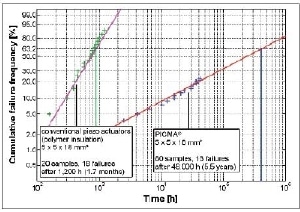
Figure 4. Comparison of PICMA® and conventional piezo actuators insulated with a polymer coating. Results of an accelerated life test with increased humidity for accelerated aging (Test conditions: 100 V DC, 22 °C, 90 %RH). Statistical methods can be used to derive values under normal climatic operating conditions from this. The extrapolated average lifetime (MTTF) for PICMA® actuators is more than 400,000 h (approx. 45 years). All polymer-coated comparison samples fail, at the most, after only 1,600 hours (MTTF = 890 hours, about 1 month)
Lifetime Calculations of Multilayer Piezoelectric Actuators
The DC-test results of PICMA® actuators are the basis for the lifetime calculations under predefined conditions. The individual factors which can have an impact here must be taken into consideration: Temperature, relative humidity and applied voltage. These were gathered through an extensive series of tests still in progress. The dependencies are shown in the adjacent diagrams (Fig. 5).
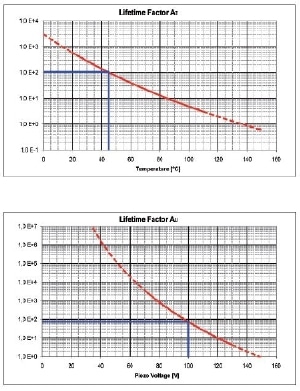
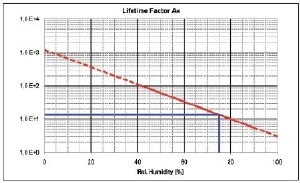
Figure 5. The diagrams show the interdependency between the mean lifetime of a PICMA® actuator and the value of the voltage applied, the ambient temperature and the relative humidity. Important: With decreasing voltage the lifetime increases exponentially. This must always be taken into consideration in an application.
Case Study: Long-Term Cryogenic Test of Multilayer Piezoelectric Actuators
Test on the lifetime of PICMA® actuators for a 10-year cryogenic application were also conducted by Dr. Bosotti, University of Milano, Italy in 2005.
Calculating the Lifetime in the Application
In the selected simplified presentation, the average lifetime of a PICMA® multilayer actuator can be directly derived for the intended operating conditions. The effect on the lifetime of each individual factor can be read off the diagrams. The the lifetime calculated in hours simply results as the product of all three values read off the diagrams. This calculation can also be used to optimize a new application in terms of its lifetime as early as in the design phase. A decrease in the control voltage or the control of temperature and humidity with flushing air or encapsulation can be very important here. The impact that the applied voltage has, is particularly important. The lifetime to be expected at 80 V DC, for example, is 10 times higher than that to be expected at 100 V DC.
The simple formula MTTF = AU * AT * AF provides a quick estimate of the reliability in hours. In concrete terms: The values for 75 % RH (AF=14), 100 V DC (AU=75) and 45 °C (AT=100) result in an approximate average lifetime of 105,000 h, i.e. more than 11 years (see markings on the diagrams).
Multilayer Piezoelectric Actuators Under Dynamic Operation
Dynamic Continuous Operation Cyclic demands with a rapidly alternating electrical field and high control voltages (typically > 50 Hz; > 50 V) are common conditions for multilayer piezoelectric actuators, for example when used in valves, pumps or ultrasonic transducers. The lifetime of the piezo element is in this case dominated by different factors to those affecting DC operation: The impact of the dynamic forces and the changing state of the mechanical stress increases. Therefore, this can lead to the formation of cracks in the stack construction and hence to electrical discharges. The impact of the humidity, on the other hand, is negligible because it is reduced locally by the warming-up of the piezoceramic. The most important factors affecting the lifetime are therefore the voltage and the type of the signal. In AC operation, the lifetime itself is not expressed as a time period but more sensibly as a number of cycles. Extraordinarily Robust: 1010 Working Cycles Due to the stability of the material behavior and their mechanical construction, PICMA® actuators exhibit no signs of wear even after many billions of load cycles (Fig. 6). The target of 1010 working cycles is especially important for industrial use. The proof for the reliability of the PICMA® technology is obtained by means of a test with particularly high control frequency. Preloaded PICMA® actuators with dimensions of 5 x 5 x 36 mm were loaded at room temperature and average humidity with a sinusoidal signal of 120 V unipolar voltage at 1,157 Hz. This produces 108 cycles per day! Even at this high voltage and frequency there was not a single failure and the actuators showed no significant changes in displacement.
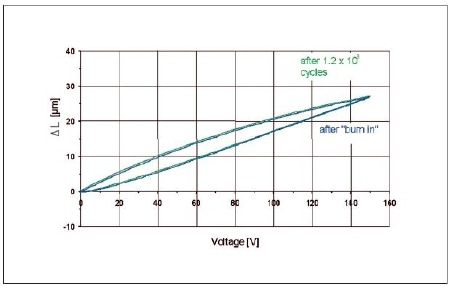
Figure 6. Dynamic test series with eight PICMA® actuators 5 x 5 x 18 mm: Total number of cycles 4.0 x 109 cycles; 116 Hz sinusoidal control (1.0 x 107 cycles per day), 100 V unipolar operating voltage, 15 MPa preloading. Control measurements after each series of 109 cycles. Only insignificant decrease in the displacement.
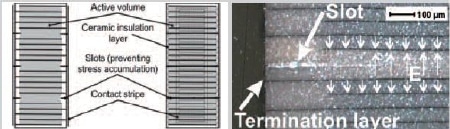
Figure 7. Patented PICMA® design with lateral slots to avoid uncontrolled expansion cracks during dynamic control
Patented Design Reduces Stress Under Dynamic Loads
PI reduces the probability of crack formation by using a particular patented design with lateral slots. These reliably prevent the mechanical tensile stresses in the stack from becoming too high and the formation of uncontrolled additional cracks (Fig. 7). Furthermore, the patented meander-shaped construction of the termination electrodes (see Fig. 2) ensures all internal electrodes have a stable electrical contact even at extreme dynamic loads.
Longer Operating Periods and Higher Control Frequencies
The dynamic operation of PICMA® piezo elements benefits significantly from the large range of operating temperatures of up to 150 °C. The intrinsic warming of the elements when dynamically controlled is proportional to the operating frequency. A higher operating temperature thus also allows higher control frequencies and longer periods of operation. Additionally, the displacement of the PICMA® piezoceramics exhibits only a low dependence on temperature.
Different Types of Piezoelectric Actuators
Ceramic-Insulated High-Power Actuators: Multilayer Piezo Stack Actuators
The benefits of multilayer piezo stack actuators are as follows:
- Superior lifetime even under extreme conditions
- Very large operating temperature range
- High humidity resistance
- Excellent temperature stability
- High stiffness
- Peak current up to 20 A
- UHV compatible to 10-9 hPa
- Sub-millisecond response/Sub-nanometer resolution
- Ideal for dynamic operation
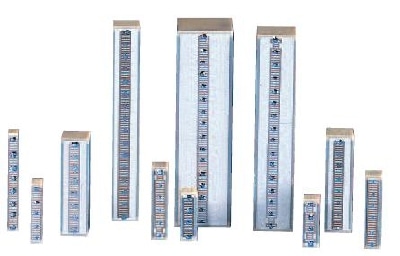
PICMA® actuators achieve positioning resolutions in the sub-nanometer range and response times in the microsecond range. The ceramic surface of the actuators is excellently suitable for mounting sensors, such as strain gauges. In contrast to polymer-coated actuators, the sensor can be applied directly to the ceramic of the PICMA® actuator, allowing for higher stability, linearity and measuring accuracy.
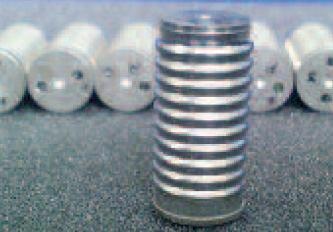
Improved reliability even for permanently high humidity or splash water by hermetic encapsulation with inert gas filling.
PICMA® Bender Actuators: Multilayer Piezo Bender Actuators with High Travel and Low Operating Voltage
PICMA® multilayer bender piezo actuators offers a wide range of features including:
- Ceramic Encapsulation for Better Protection and Longer Lifetime
- Positioning Range up to 2 mm
- Fast Response (10 msec)
- Nanometer-Range Resolution
- Low Operating Voltage
- Vacuum-Compatible Versions to 10-9 hPa
- Available with Integrated Position Sensor
- Special OEM- and Bench-Top Amplifiers Available
PICMA® multilayer bender piezo actuators provide a deflection of up to 2 mm, forces up to 2 N and response times in the millisecond range. These multilayer piezoelectric components are manufactured from ceramic layers of only about 50 ìm thickness. They feature internal silver-palladium electrodes and ceramic insulation applied in a cofiring process. The benders have two outer active areas and one central electrode network dividing the actuator in two segments of equal capacitance, similar to a classical parallel bimorph.
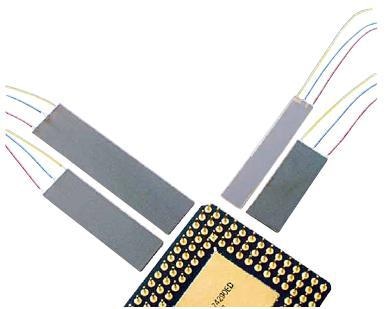
Bender actuators with optional wire leads (order number extension .x1); micro processor for size comparison
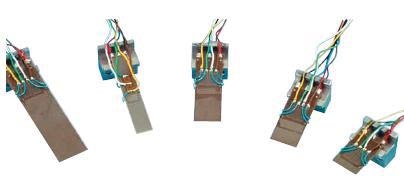
Bender actuators with strain gauge positioning sensors are available with product number P-871
Advantages of Multilayer Piezo Bender Actuators
PICMA® Bender piezo actuators offer several advantages over classic bimorph components manufactured by gluing together two ceramic plates (0.1 to 1 mm thick): faster response time and higher stiffness. The main advantage, however, is the drastically reduced (by a factor of 3 to 10) operating voltage of only 60 V. The reduced voltage allows smaller drive electronics and new applications, such as in medical equipment. Additionally, these devices offer improved humidity resistance due to the ceramic encapsulation.
PICMA® Chip Actuators: Miniature Multilayer Piezo Stack Actuators
The benefits of miniature multilayer piezo stack actuators are:
- Superior Lifetime Even Under Extreme Conditions
- Ultra-Compact: from 2 x 2 x 2 mm
- Ideal for Dynamic Operation
- Sub-Millisecond Response
- Sub-Nanometer Resolution
- Vacuum Compatible to 109 hPa
- High Humidity Resistance
Advantages of Miniature Multilayer Piezo Stack Actuators
PICMA® Chip actuators sized from 2 x 2 x 2 mm are the smallest monolithic multilayer piezo stack actuators available. Providing sub-nanometer resolution and sub-millisecond response, they are ideally suited to high-level dynamic applications.
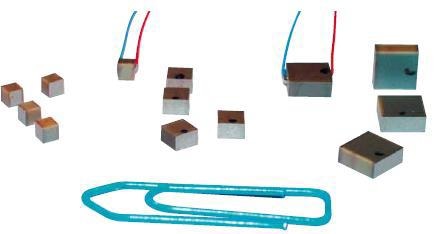
PICMA® chip miniature piezo actuators are the smallest ceramic encapsulated multilayer piezo actuators available, paper clip for size comparison.
Applications of Miniature Multilayer Piezo Stack Actuators
Typical applications of miniature multilayer piezo stack actuators are:
- Static and dynamic precision positioning
- Laser tuning
- Micro-dispensing
- Metrology / Interferometry
- Life science, Biotechnology
- Photonics
For full reference listing please visit Physik Instrumente
Source: Physik Instrumente