In a pre-proof article posted in Acta Materialia, researchers have proposed a novel method for applying Bragg edge neutron imaging to evaluate mechanical surface treatment by deducing lattice spacing distributions with the help of energy-resolved radiography.
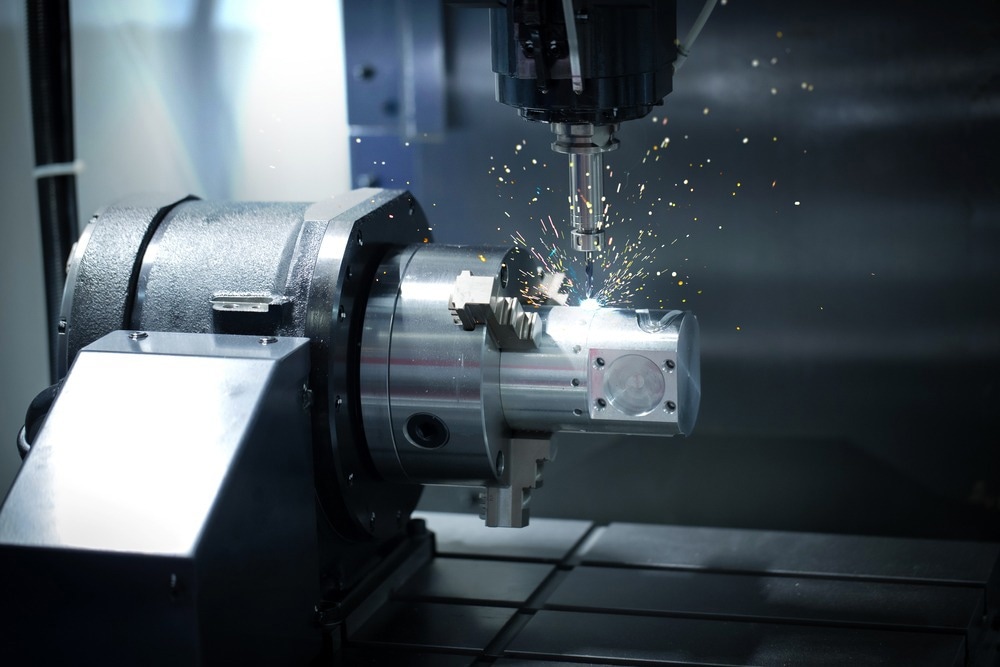
Study: Mechanical Surface Treatment Studies by Bragg Edge Neutron Imaging. Image Credit: Red ivory/Shutterstock.com
Mechanical surface treatment technologies such as cavitation peening and laser peening optimize their processing parameters by conducting a thorough characterization, including residual stress analysis. Recent advancements at neutron facilities enable non-destructive, two-dimensional residual stress mapping by Bragg edge neutron imaging, which has distinct advantages over more conventional methods.
In the current work, three different examples were used to illustrate the unique abilities of the Bragg edge neutron imaging method, particularly for providing relatively high spatial resolution near-surface residual stress maps within samples with complex geometries. The researchers highlighted the viability of Bragg edge neutron imaging radiography as a technique for surface treatment by presenting a comparative analysis of the X-ray and neutron diffraction results.
Neutron Imaging and Non-Destructive Residual Stress Mapping
Various mechanical surface treatment techniques can be employed to improve engineering components' fatigue and mechanical performance. Using a laser-induced shockwave in laser peening, which produces results akin to shot peening but with higher compressive residual stress fields and superior surface polish, has gained popularity as a surface treatment technique. Other new peening techniques, such as cavitation peening that employs cavitation peening bubble impacts, have also been developed.
In addition to other benefits, the surface treatment techniques produce compressive residual stress close to the surface of the components, which balances the applied force and prolongs the component's service life. The quantitative assessment of residual stress produced by these techniques is crucial to their development and design since the presence of compressive residual stress is the main reason for enhancing fatigue performance by mechanical surface treatment.
Recent advancements in energy-resolved neutron imaging, novel detector technologies, and access to specialized time-of-flight (TOF) neutron imaging devices have created opportunities for neutron imaging of residual stress with high spatial resolution in engineering components. The method explores Bragg edge, which are sharp increases in transmission at specific wavelengths brought on by the removal of neutrons via Bragg edge diffraction.
In contrast to non-destructive direct scanning of diffraction signals using traditional neutron and X-ray diffraction techniques, Bragg edge neutron imaging produces relatively extensive stress maps across many millimeters within a transmission geometry in a single exposure. Bragg edge neutron imaging eliminates the pseudo-strains issue of neutron diffraction for near-interface or near-surface residual stress measurement due to a gauge volume's partial immersion in a sample.
The current work illustrated the benefits and drawbacks of the Bragg edge neutron imaging approach for surface treatment by employing the technique in three study scenarios. Bragg edge neutron imaging and the other traditional techniques were compared for correlations between residual stress measurement. The researchers believe that the present demonstration could inspire further work into the potential of Bragg edge neutron imaging as an analysis tool for surface treatment.
Experimental Setup for Bragg Edge Neutron Imaging
A Bragg edge transmission pattern exhibited a series of sharp leaps as a function of neutron wavelength l. A polychromatic beam on a TOF device from a pulsed neutron source was used to obtain the necessary Dl/l resolution for Bragg edge neutron imaging studies, which demanded a wavelength-resolving setup. A time- and spatial-resolving neutron detector was necessary for conducting the studies.
Large-scale research facilities worldwide offer Bragg edge neutron imaging. The current study was conducted on the RADEN beamline at J-PARC in Japan and the IMAT beamline at ISIS in the UK. IMAT's sample positioning stage consisted of a rotation stage and two perpendicular tilt alignment axes. Various peening research aspects, including peening techniques, peened surface geometry, and peening coverage, were also carried out.
The unique capabilities of the Bragg edge neutron imaging approach were demonstrated using three separate cases. The first case studied the effects of three peening techniques -submerged laser peening, cavitation peening, and water jet-accelerated shot peening - on JIS SKD61 steel samples.
Submerged laser peening produced peening results from the collapse of cavitation bubbles produced after laser ablation and the plasma created following the ablation of the sacrificial layer.
In cavitation peening, the sample’s surface was peened by cavitation peening impacts produced by a submerged high-speed water jet and was utilized to peen relatively hard steel.
The second study case dealt with the use of laser peening on complex geometries. Laser peening was proposed to extend the fatigue performance of highly stressed turbine blade components, particularly the turbine blade's fir-tree root.
Test specimens that resembled complexly structured fir tree samples were used for the laser peening measurements. Three coupons were created using 12%Cr martensitic stainless steel, frequently utilized in steam turbine blade applications. The coupons were specifically peened and manufactured to resemble the laser peening process on the root of a fir-tree-shaped turbine blade consisting of convex and concave features.
Five blocks of aluminum manufactured of 7050 aluminum were used in the third study. The samples, which were offcuts from an original wingtip device of an aircraft, measured 75 mm ´ 17 mm ´ 15 mm. The objective of this measurement was to examine the residual stress in samples that had undergone extensive laser peening and cavitation peening in terms of both intensity and coverage.
Bragg Edge Neutron Imaging and the Future of Surface Treatment
The current work demonstrated the application of Bragg edge neutron imaging for mapping near-surface residual stress, particularly for mechanical surface treatment.
The Bragg edge neutron imaging approach revealed compressive residual stress fields caused by various peening techniques such as cavitation peening and laser peening. Both the introduction of the inertial confinement overlay (water) and the laser angle of incidence impacted the performance of the laser peening method. In contrast, the surface geometric features impacted the ensuing hydrodynamic processes for the cavitation peening method.
The abundance of data obtained from the stress maps highlighted the effectiveness of Bragg edge neutron transmission for residual stress mapping over traditional diffraction-based techniques. It was also observed that even a highly textured sample could provide stress information. According to the authors, further research is required to ascertain whether a textural alteration that altered the height and structure of Bragg edges could result in a false stress reading.
Data from other tests, including fatigue crack initiation and growth, was complemented and correlated with the results from Bragg edge imaging. The plastic deformation region generated by very high peening coverage demonstrated plasticity, another helpful information that could be obtained through Bragg edge imaging.
Reference
R.S. Ramadhan et al. (2022) Mechanical Surface Treatment Studies by Bragg Edge Neutron Imaging. Acta Materialia. https://www.sciencedirect.com/science/article/pii/S1359645422006395
Disclaimer: The views expressed here are those of the author expressed in their private capacity and do not necessarily represent the views of AZoM.com Limited T/A AZoNetwork the owner and operator of this website. This disclaimer forms part of the Terms and conditions of use of this website.