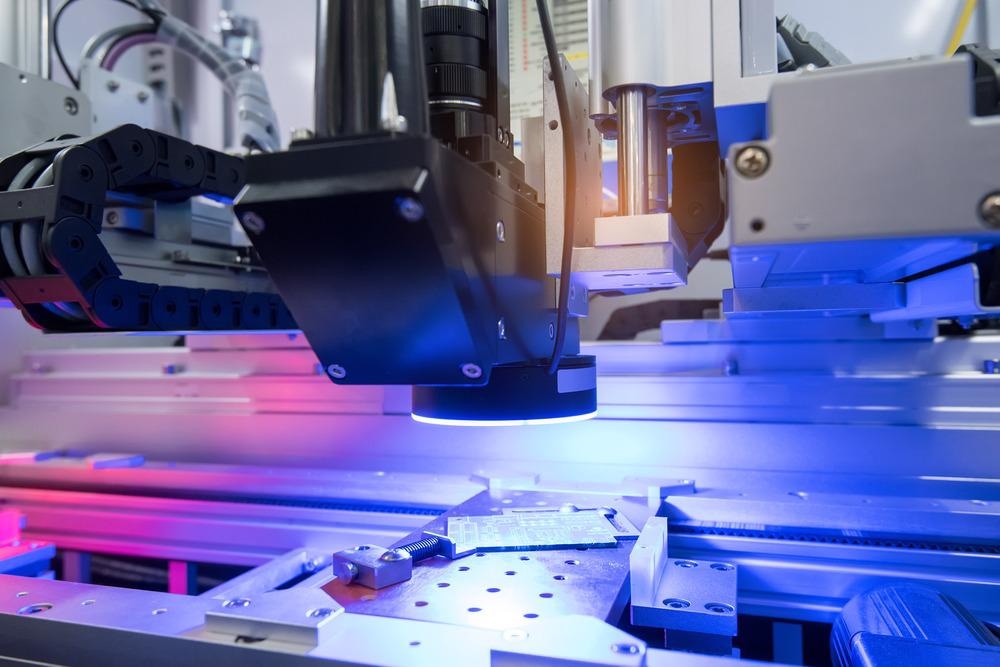
Image Credit: asharkyu/Shutterstock.com
Commonly found in manufacturing, machine vision systems create and analyze digital images to guide automated production and quality operations. A new cost-effective 3D machine vision system from Cognex Corporation uses a novel camera device to enable a range of engineering and production functions.
Machine Vision System Applications
Machine vision systems have a significant position in modern, automated production operations. These systems perform assembly proof and inspection functions through their capability to steer material handling machinery to place products, parts, or raw materials as required in a particular process.
Machine vision systems have a wide range of uses across various industries and help automate repetitive tasks that can become exhausting to a human. For example, the application of machine vision systems enables the complete inspection of raw materials, parts, or products, leading to superior yields, lower numbers of defects, greater quality, reduced costs, and higher consistency of results.
The Cognex Automated 3D Vision System for High-Quality Inspection
The new 3D-L4000 system from Cognex brings together speckle-free blue laser optics and a broad selection of true 3D vision tools. According to Cognex, the system rapidly captures and processes 3D images with high-quality inspection and guidance functions.
The system's vision tools enable greater accuracy than more conventional systems, increasing the kinds of assessments that could be performed. Furthermore, because evaluations are in 3D, users can see how the vision tools work on actual parts.
The next-generation automated inspection system contains all the conventional 3D measuring tools end-users expect, including height and plane finding. It also includes a wide-ranging collection of 3D vision tools for making use of assessments in a true 3D space.
The system's spreadsheet interface facilitates the combination of 2D and 3D vision tools, resulting in quicker deployments.
The Cognex system is available in three different fields of view and is suited to operations across various industries, including food production, automotive, and electronics.
How Machine Vision Systems Work
When conducting a common function, such as product evaluation, the process begins with a sensor detecting if an object is present. If it does detect an object, the sensor triggers a camera that captures an image and offers a source of light to highlight the most important features. A digitizing unit converts the camera’s image into a digital file, which is then saved in a computer system for viewing and or software processing.
Before processing an image file, the image must first be decreased in gradation to a black and white format. The image is then reviewed by the system to recognize proper components or flaws according to established criteria. After the system reviews the image, the object can be manipulated, rejected, or accepted by the production system.
Also known as the automated inspection of the manufacturing process, machine vision systems typically have multiple components, including lighting, an optical system, a sensor, a vision processing system, and a communications platform. Machine vision systems could be made up of distinct parts or a singular unit, such as Cognex's new smart camera system.
What is a 3D Machine Vision System?
Machine vision systems capable of seeing in two dimensions have been in use for decades, and they do an adequate job in a wide variety of applications. However, there are several production line situations where 2D vision is inadequate.
With a 2D vision system, the image of a three-dimensional object is essentially the view of a single plane: data for an X-axis and a Y-axis, but not for a depth of field Z-axis. A result is a 3D object seen from a particular point of view. Because different viewpoints can produce completely different planar views, 2D machine vision has limited use in situations where form information is crucial to conducting a task.
Since a 2D machine vision system can only identify certain visible edges and surface features, it has difficulty accurately capturing objects that are too dark or shiny. In addition to a severe lack of contrast, object movement in the Z-plane can also cause errors.
There are four primary methods for 3D machine vision: stereo vision, laser triangulation, structured light, and time-of-flight. In laser-based triangulation systems, such as the one found in the new Cognex device, a thin band of light scanned onto a 3D surface generates a strip of illumination that appears distorted at a perspective different from that of the projector. Analysis of the generated line images can then be utilized to obtain a precise geometric image of the target object's shape.
The quality and capabilities of various 3D machine vision solutions make it difficult to select the best tool for a given job.
Resources and Further Reading
Cognex Corporation. Cognex Introduces the In-Sight 3D-L4000 Vision System. Cognex Press Preleases. [Online] Available at: https://www.cognex.com/company/press-releases/2021/in-sight-3d-l4000-launch
Edwards, E. An Introduction to Machine Vision Systems. Thomas Guides. [Online] Available at: https://www.thomasnet.com/articles/automation-electronics/machine-vision-systems/
Schumann-Olsen, H. Why 3D machine vision? What’s wrong with 2D machine vision? Zivid blog. [Online] Available at: https://blog.zivid.com/why-3d-machine-vision-whats-wrong-with-2d-machine-vision
Disclaimer: The views expressed here are those of the author expressed in their private capacity and do not necessarily represent the views of AZoM.com Limited T/A AZoNetwork the owner and operator of this website. This disclaimer forms part of the Terms and conditions of use of this website.