Feb 19 2020
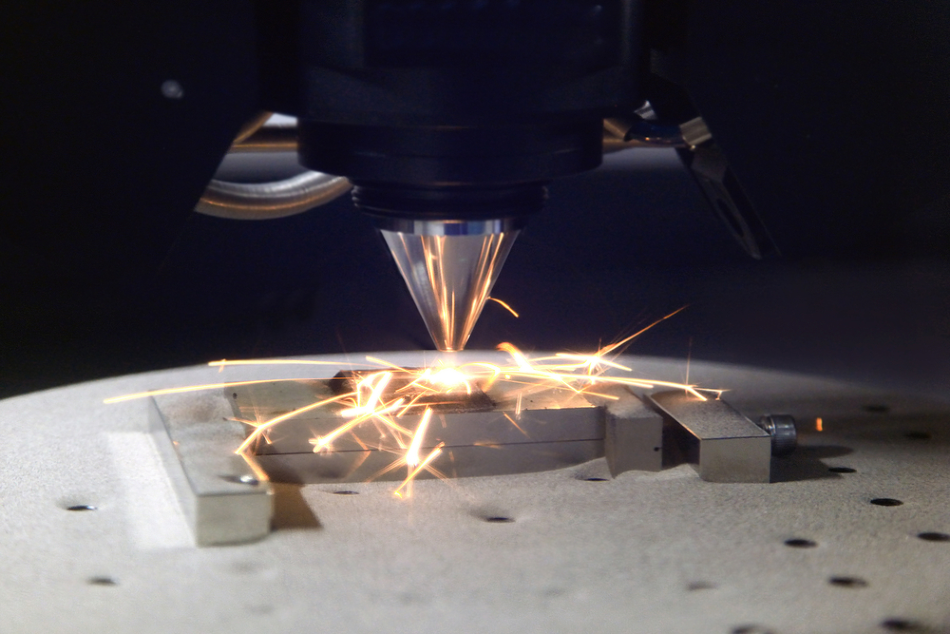
Image Credit: sspopov/Shutterstock.com
From its beginnings in the mid-1980s, 3D printing, or as it is also increasingly referred to, additive manufacturing, has promised many advantages over conventional manufacturing methods.
The initial limitation was the range of materials available and the scale of built objects. However, the advantages of additive manufacturing are being exploited by many manufacturing sectors in materials as diverse as concrete in building projects to glass lenses in optics. Now, being able to manufacture 3D printed parts in metal is revolutionizing the way things are made.
Techniques for 3D Printing Metals
Currently, there are two methods used to produce 3D printed objects in metal. The first is referred to as Selective Laser Sintering(SLS),or sometimes Direct Metal Laser Sintering(DMLS). The second is Selective Laser Melting (SLM) or Direct Metal Laser Melting (DMLM).
The difference between the two is straightforward and it is related to the temperature to which the printed material is heated. Selective Laser Sintering heats the material, a finely powdered metal, to the point where the particles, typically between 20 and 40 micrometers, are welded or fused.
As its name suggests Selective Laser Melting heats the material to the point where it becomes molten, producing metal parts that can be treated in the same way as conventionally produced items.
Both systems produce parts that can be machined, heat-treated or given various surface finishes.
Issues with Additive Manufacturing
The problem is, according to researchers in the field, not all alloys take to additive manufacturing very well. For example, some alloys will not melt and if they do, they can crack once you try to manufacture a part.
Some of the most common and reliable metals for 3D printing are stainless steel, aluminum, titanium, cobalt, chrome and Inconel, a nickel-chromium-based superalloy. Choosing the most appropriate material is vital for ensuring parts will perform as needed.
Additive manufacturing in metal has been useful in producing complex high-value items. Once the object has been designed and successfully manufactured, it is highly reproducible and of very consistent quality. The need to produce items for very specialist applications has led to research into specialist “designer alloys” that are both suitable for the process and the function.
Titanium alloy powders currently used in 3D printing have an issue that often occurs in 3D printed metals. They cool and bond together in column-shaped crystals during the printing process, making them prone to cracking or distortion.
Additives called inoculants, which cause nuclei to form in the melt, have been incorporated into metal-alloy powders used in additive manufacturing.They increase the density of nuclei and refine the microstructure.
However, to date, there has not been a suitable inoculate for use with titanium. Researchers at the School of Engineering at RMIT University in Australia have developed a titanium copper alloy that could solve the problem. When printed the alloy crystals grow equally in all directions forming a strong bond.
"Alloys with this microstructure can withstand much higher forces and will be much less likely to have defects, such as cracking or distortion, during manufacture,” said Mark Easton from the team involved in its development.
Focus on Steel
While there has been a focus on titanium alloys for additive printing, some researchers believe there is a need for further study into steel. The Air Force Research Laboratory has developed a steel alloy powder called AF-9628. It has the strength and toughness needed for aerospace parts and printed parts met benchmarks for porosity, strength, and impact toughness without any post-production.
While the alloy costs less than some other high-performance steel alloys, including Eglin Steel and HP-9-4-20, it is only available in small quantities and probably won’t be cost-effective while demand is low.
Meanwhile, a team from the NASA Marshall Space Flight Center (MSFC), Alabama, and the NASA Glenn Research Center (GRC),Ohio, have developed and 3D printed a new high strength, high conductivity, copper-based alloy, GRCop-42, for use in rocket propulsion components. It can be used to produce near-fully-dense 3D printed parts such as combustion chamber liners and fuel injector faceplates.
Conclusion
As more is understood about the shortcomings of current alloys used in the additive manufacture of metal, research into advanced alloys that resolves these issues will help ensure that the technology achieves all that it initially promised.
References and Further Reading