The use of software-supported camera image evaluation is highly beneficial in the early detection of irregularities and defects in production processes. How can image data contribute to zero-defect production?
Early defect detection is a significant contributor to overall quality assurance, leading to increasing numbers of production lines being equipped with state-of-the-art camera technology. The primary objective of these production lines is to get as close to zero-defect production as possible.
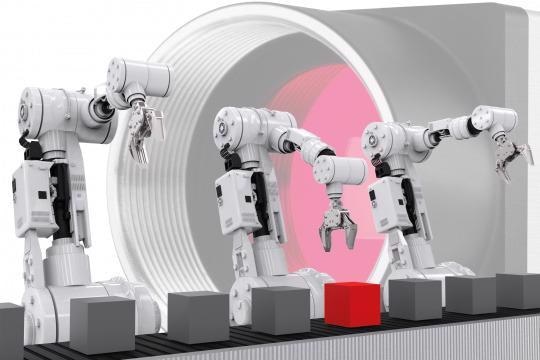
Image Credit: IDS Imaging Development Systems GmbH
The goal of improving process and product quality has resulted in manufacturing procedures existing in a state of constant change. A considerable amount of energy is invested in automating test steps as manufacturers work to accelerate throughput while reducing waste, driven by the desire to save time and money.
There is no way that humans will achieve these objectives without the help of machines, and as more quality assurance functions are automated, essential yet cost- and time-intensive lab tests are steadily being replaced by product inspections inline and on the shop floor.
These inspections see modern camera technology used to maintain an overview of test objects and their properties at all times, as well as in almost any location as production progresses. This is done without actively intervening in the production process.
The use of camera images offers a number of key advantages and options for use, particularly when used in conjunction with image processing technologies. The use of optical measurement and test procedures allows exceptionally fast, wear-free, quality tests to be performed during the manufacturing process.
While standard barcode readers can read the content of a code, industrial cameras can read the content of the code while also determining and evaluating its quality, size, alignment, color, surroundings and more.
This added functionality expands test capabilities and test quality while also making the further automation of quality assurance simpler. Cameras enable the early detection of defects, often detecting these before they cause irreparable aftereffects.
When implementing camera technology, it is important to choose instrumentation that is able to adhere to the stringent standards of measurement and test equipment required to make autonomous decisions. This technology is required to provide humans with the best possible assistance, potentially even replacing them.
With 3D image processing, the flexibility and accuracy of measurement and test processes can be improved immensely.
Dr. Martin Hennemann, Product Manager for ENSENSO, IDS
Current 3D camera technology allows robots to analyze their environment, providing them with the information they need to respond to different situations autonomously.
In addition to monitoring the position and dimensions of objects on the shop floor, this data may also facilitate the drawing of precise conclusions around deviations or imperfections with respect to reference objects. In these applications, inline inspections will show whether the correct product components are being assembled.
There is an especially high potential for error in the automotive industry due to typical production processing involving a significant number of variants. Customers are able to customize vehicles according to their individual specifications, for example, selecting specific engine variants, tires, chassis or interior equipment.
Production personnel in these organizations benefit from automated systems which alert them well before a wrong, or defective part is installed. This additional quality assurance also reduces the labor and time required for inspections after production, reducing the risk of production downtimes due to errors.
The high degree of individualization in the configuration of cars inevitably results in an immense range of variants, which is practically impossible to manage and check without the assistance of camera technology.
Dr. Martin Hennemann, Product Manager for ENSENSO, IDS
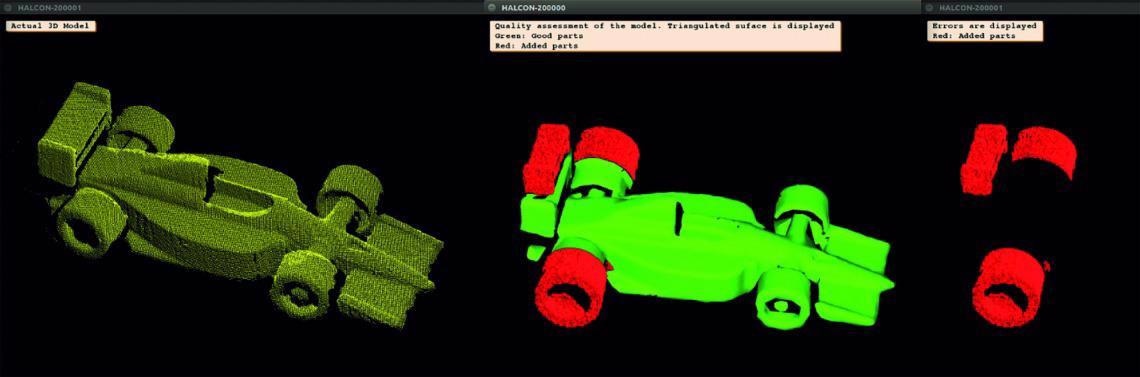
With HALCON 3D image processing, even the tiniest differences between the object and the reference model can be detected. Image: Demo by IDS, Control, captured with an Ensenso 3D stereovision camera. Image Credit: IDS Imaging Development Systems GmbH
IDS demonstrated an example of 3D object verification at the Control international trade fair for quality assurance in Stuttgart. The demo system was designed to reconstruct objects using an Ensenso N35 3D camera before employing HALCON image processing to perform a comparison of data.
The 3D data generated were compared against a reference model, allowing any imperfections or deviations to be detected. The 3D image processing was able to identify irregularities in test objects which had not been visible to the human eye.
This technology allowed the quality of manufactured objects to be significantly improved for subsequent process steps. This was achieved via ultrahigh precision digitization using Ensenso 3D cameras, followed by image processing for object verification.
3D complements 2D camera technology. Each technology has its own advantages. The combination of 2D and 3D performs the tasks of today and tomorrow while effectively minimizing production errors.
Dr. Martin Hennemann, Product Manager for ENSENSO, IDS
Three dimensional technology is a valuable supplement to 2D camera technology. When used in combination, these two approaches can be used to perform an ever-increasing range of functions.
Each of these two technologies offers key advantages for specific applications. The analysis of 3D data enables the determination of shapes, surface structures, or the position of objects in space.
Meanwhile, 2D data allow the precision detection of edges and colors, as well as markings. In the 2018 IDS control demo, 3D data was used to perform an object comparison.
If part codes are present, these can be decoded via 2D camera images and used for identification. Car manufacturers will also typically utilize camera-based inspection methods with combined 3D and 2D technology for final inspection.
This allows them to acquire clearance dimensions on a finished car body in order to precisely test or measure these against specifications.
Camera technology opens up many possibilities in helping manufacturers move towards the ideal of zero defect production. Effectively minimizing production errors may require the use of 2D or 3D technology, or even a combination of the two, depending on exactly what is being tested.
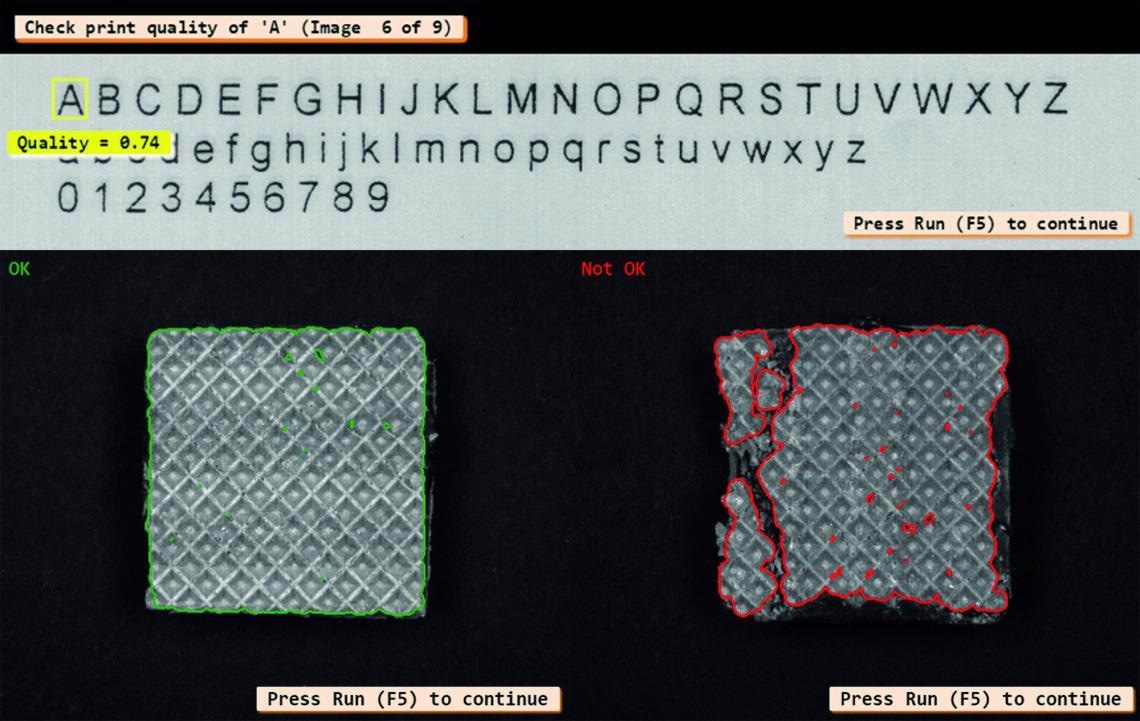
For text recognition (OCR) and edge detection, classic 2D image material is the best source material for image processing. Image Credit: MVTec HALCON.
Camera systems are also useful in supporting manual manufacturing processes. They can be used to monitor manual workflows at manual workstations, with image evaluation taking place to confirm that the operator has selected the correct parts, that a production step has not been missed or that the correct number of screws have been fitted to a part.
A downstream system may be used to indicate whether operations have been performed correctly or incorrectly via audible or visual alerts, providing a vital quality control step during production.
Both camera and production technologies are constantly developing, but the advent of a new camera technology will not immediately render the existing one obsolete.
New 3D technology has advanced a great deal in recent years and is now able to display different features of an object. This has led to new applications becoming viable, allowing 3D technology to serve as a valuable supplement to 2D camera technology without completely replacing it.
Cameras have evolved from basic image delivery machines to smart and adaptable image processing solutions.
A robust combination of camera, sensors, communication intelligence, and versatility has enabled machine-vision systems do not only offer the functionality of 2D and 3D cameras but also represent a notable contribution to the prevention of errors as part of an overall quality assurance program.
Still, perfect production with no defects or reworking required remains the ideal aspiration. While this goal is unattainable, even with huge investment and the latest technology, the use of camera and evaluation technology is now an invaluable tool for any organization looking to take significant steps towards the ultimate goal of zero defect production.

This information has been sourced, reviewed and adapted from materials provided by IDS Imaging Development Systems GmbH.
For more information on this source, please visit IDS Imaging Development Systems GmbH.