The most essential thermal joining technology for metals is Gas Metal Arc Welding (GMAW).
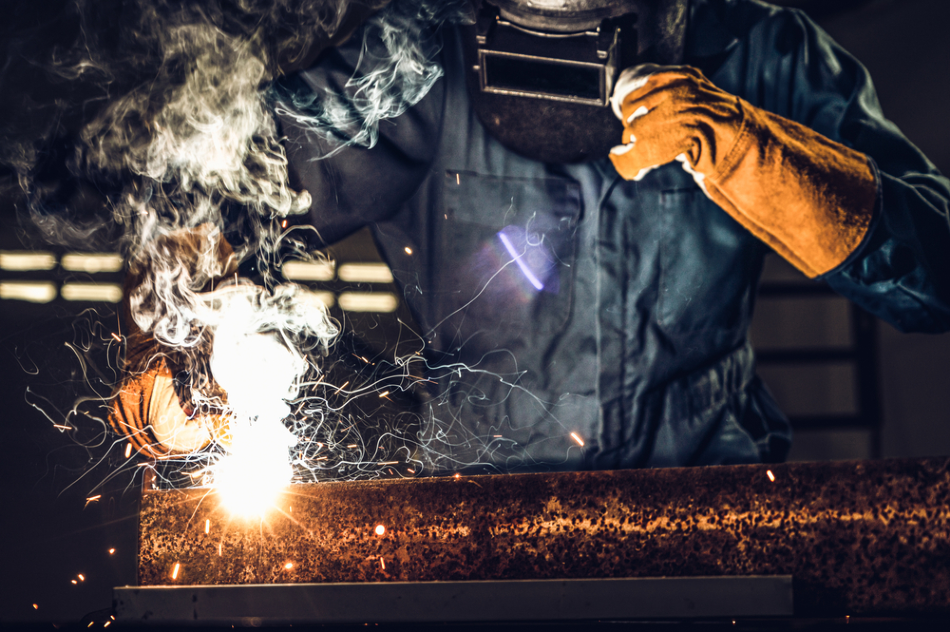
Image Credit: Shutterstock/Blue Planet Studio
GMAW is of critical importance particularly for medium and small sized companies (SME) because of its versatility and inexpensive costs. During the welding arc, the weld pool and heated workpiece are shielded against interactions with the atmosphere by a protecting gas cover.
The gas is supplied externally and is introduced to the process utilizing a welding torch. At the welding torch, and especially in the gas nozzle, the flow of gas is produced to create a uniform and potentially laminar free jet flow around the process and the arc.
Welding Torches
The manufacture of welding torches is mostly a result of experience and it has been produced experimentally so far. Schlieren shadowgraphs have been utilized to evaluate the turbulence of the shielding gas-free jet at welding torches without an arc since the 1960s.
The gas flow throughout welding and its interactions with the arc are very difficult to analyze with traditional flow analysis, because the high temperature of up to 20000 K, strong electromagnetic fields and radiation limit the usage of the majority of standard flow measurement systems in arc welding.
This article describes a PIV setup, which was specifically tailored to measurements of the shielding gas flow in GMAW.
Particle Image Velocimetry
The Particle Image Velocimetry (PIV) is an optical technique that is non-intrusive, which allows for flow analysis in arc welding systems with considerably high temporal and spatial resolution.
The information which describes flow in the pictures is based on tracer particles, which are lit up by a laser light twice within a specified, brief time interval while following the flow.
The set-up of the measurement is comprised of a high-speed camera and a synchronized CAVILUX HF diode pulse laser system. CAVILUX HF creates laser pulses with high pulse power and high frequencies.
For the first time, this laser unit allows for time-specific investigations of the gas flow in arc welding. The laser unit and its optics are both highly compact and are convenient to transport and utilize in industrial applications.
The Measurement Method and Setup
The PIV measurement system was tailored in order to provide measurements at GMAW welding processes.
A Photron SA4 High-speed camera was used with a frame rate of 5000 or 10000 fps and pictures of 768 x 1024 or 768 x 512 pixels respectively.
The laser unit is coupled with a special optics (prototype) by Cavitar Ltd. that spreads the laser beam to a laser light-section with a thickness of around 0.5 mm across a measuring field with a width of 40 mm.
In combination with a small band-pass interference filter of 808 ± 3 nm, the tracer particles are only lit up by the laser and not by the arc.
The camera optics and the laser are shielded against spatters made of metal by protective classes. In the organization, the workpiece is transported under a fixed welding torch.
Once each measurement has been taken, the torch is dismantled and is cleaned with compressed air. The torch, in this case, was transported by a robot between fixed service and operating positions. This setup is displayed in Figure 1.
.jpg)
Figure 1. Scheme and photograph of the experimental setup.
When employing the PIV system for flow measurements at arc welding processes, two key adjustments are required. These changes are in relation to the tracer particles utilized and to the strong characteristic radiation of the arc.
The tracer particles conventionally utilized in PIV are comprised of oil or a test fluid, for example, DEHS produced by compressed air. The diameter of such particles is 0.5 to 50 micrometers.
The use of oil or water in arc welding is not possible because of metallurgical and procedural limitations. Magnesium oxide particles with a maximum diameter of 1 µm were employed for PIV at GMAW because of this.
The particles have a density of 3.65 g/cm3, a melting temperature of 2640 °C, and increased chemical stability at high temperatures. The microscopic evaluation suggests that the particles are highly porous and bumpy.
The true density of the particles in the air should be even smaller and the particles’ ability to follow the flow run is very good.
Tests with a welding arc and a powder doped flow show that only a small portion of particles are melted in the arc and deposited as slag onto the welding bath. Most of the particles go past the flow field without being evaporated or melted by the arc.
.jpg)
Figure 2. Laser, control unit, and prototype of light sheet optics.
The radiation of the arc is the next challenge after adequate tracer particles have been selected. In GMAW, the arc generates around 1 to 2 kW of radiation which affects all particles and overexposes the camera.
The majority of the radiation generated is from metal vapor and is of wavelengths below 650 nm. Argon emission from the shielding gas is not as powerful, but there are some concentrated ranges of atomic argon at 800 and 810 nm.
A narrow band interference filter of 808 nm central wavelength was utilized as a means to blank the arc radiation. The filter has a full width of half maximum (FWHM) of ± 3 nm. The interference filter ensures that the particles are almost solely illuminated by the laser and that the pictures are not overexposed by the arc.
Therefore, the maximum pulse length of the laser, the exposure times of the camera were chosen with ~2.4 µs for 10 000 Hz and a laser pulse length of 2 µs and 1 mJ pulse energy, and an exposure time of ~5.6 µs for 5 000 Hz and a laser pulse length of 4 µs and 2 mJ laser energy.
The initial measurements taken employing traditional light sheet optics showed that the laser intensity in the light sheet was too small. An enhanced light sheet optics was produced by Cavitar in response to this, which offers greatly improved exposure of the particles in the sheet (Figure 2).
The welding process investigated was a pulsed GMAW process with a base current of 40 A, a pulse frequency of 100 Hz, and a peak current of 420 A.
A mild steel filler wire (G3Si1) was utilized with an Argon-CO2-gas mixture (M21-ArC-18) with a range of gas flow rates.
Two torches were analyzed. Torch B was a manual torch with a ø 16 mm gas nozzle and Torch A was a manual torch with a ø 13 mm gas nozzle. The torches are designed very differently as shown in Figure 3.
.jpg)
Figure 3. CAD sketches of the investigated torches A (left) and B (right).
The PIV investigations were completed utilizing the FlowManager 4.7 (Dantec Dynamics Ltd.) along with a combined MatLab-LabView-tool programmed by TU Dresden.
The correlation evaluation of the recorded images can be done directly in both software. A multi-pass correlation with a final interrogation area size of 16 x 16 pix and three refinement steps were used in this analysis.
A velocity range validation algorithm is employed once PIV investigations have been completed, which omits all vectors under 0.2 and higher than 5 m/s.
Results
Figure 4 presents an example of particle images and a calculated PIV vector map of the shielding gas flow at torch B with a gas flow rate of 10 slm and without an arc.
The images show that the flow analysis is only accurate in the free jet where particles are evident. The flow analysis demonstrates an irregular backflow region between the workpiece and the wire tip.
.jpg)
Figure 4. Examples of particle image (left) and the calculated vector field at torch B without arc (right).
In Figure 5, the mean flow profiles of the free jets of the shielding gas at torches A and B are displayed in the left and right image respectively. Each of the mean flow profiles was determined from 125 single cross-correlations.
The comparison particularly shows the influence of the lower diameter of the gas nozzle of torch A and the much smaller flow cross-section between the contact tube and the gas nozzle.
The maximum flow velocities in the free jet of torch A are increased by a factor of 4 as a consequence. A definite ‘dead water’ area can be seen under the contact tip of torch A.
High vorticity at the fringes and in the center of the shielding gas-free jet is shown by the high gradient of the flow velocity. The flow profile of torch B is much more uniform in contrast, and the flow separation region under the contact tube is less distinct.
The comparison of the flow map at torch A, with and without an arc, shows that the arc impacts the flow mostly in the direct area of the process and above the workpiece. With and without an arc, the mean flow profiles are highly alike.
.jpg)
Figure 5. Mean flow profiles of the free jet with a flow rate of 20 slm (ref. vector = 1 x 1 m/s): torch A without an arc (left) and with an arc (middle), and torch B without arc (right).
Figure 6 demonstrates a calculated PIV vector map of arc welding process with pulsed current and an example of the particle images. The images can be related to the base current phase.
The droplets are apparent because of the thermal-induced infrared radiation. The time-dependent evaluations have shown that the flow in the gas-free jet is highly influenced by the arc.
The electric current is enhanced from 40 to 420 A in 0.6 ms at the beginning of the pulse. The PIV analysis shows that the gas in the arc region instantly expands and there is a powerful increase in the velocity immediately next to the process and above the workpiece.
The gas within the free jet along with the shielding gas towards the arc is accelerated during the pulse phase.
Increased flow velocities were determined for the shielding gas flow between the arc and the gas nozzle at the end of the pulse phase. The diameter of the free jet was slightly decreased at the same time.
A large swirl also formed on the left-hand side of the arc. The diameter of the swirl and the vortex velocity alter according to the current and the pulse time.
.jpg)
Figure 6. Examples of particle image (left) and the calculated vector field at torch B in a 45° pushed position with arc (right).
PIV of GMAW welding with CAVILUX HF illumination
Figure 7. Video of the calculated vector field at torch B in a 45° pushed position with arc.
Conclusions
PIV investigations of the shielding gas flow in arc welding systems require important adjustments to the technique of PIV measurement in order to consider the requirements in relation to the process and the material, along with in regards to the intense radiation emission and high temperatures of the arc.
It is a requirement to utilize tracer particles with a high-melting temperature. A strong laser with light-sheet illumination optics is necessary in order to thoroughly illuminate the particles.
The utilization of pulsed diode lasers for PIV measurements provides new capabilities for time-specific flow evaluation of the gas flow in arc welding.
It provides flow analysis up to a frame rate of 10000 fps on gas metal arc welding (GMAW) along with gas tungsten arc welding (GTAW).
The arc can be faded out throughout the base current phase and almost faded out during the pulse current phase because of the high laser power. Flow evaluations were possible at short arc (dip transfer mode), spray arc (spray transfer mode), and pulsed arc.
The results show that the free flow run of the shielding gas jet is seriously affected by the arc. The flow field at a torch without an arc is consequently very different to the flow field within an arc.
The flow is instantly influenced by changes to the electric current, particularly for short arc and pulsed arc welding.
Employing a diode pulse laser for PIV measurements provides new approaches in scientific research for the optimization of the gas shield quality in GMAW. The measurement system can be transported and customized to industrial welding applications.
Acknowledgments
Produced from materials originally authored by Michael Schnick from the Institute of Surface and Manufacturing Technology, Technische Universität Dresden, Germany.
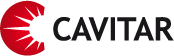
This information has been sourced, reviewed and adapted from materials provided by Cavitar.
For more information on this source, please visit Cavitar.